On Continuous Improvement
Core principles of continuous improvement are (1) process orientation, (2) improving and maintaining standards, and (3) people orientation. What are the fundamental behaviours for developing a culture of improvement?
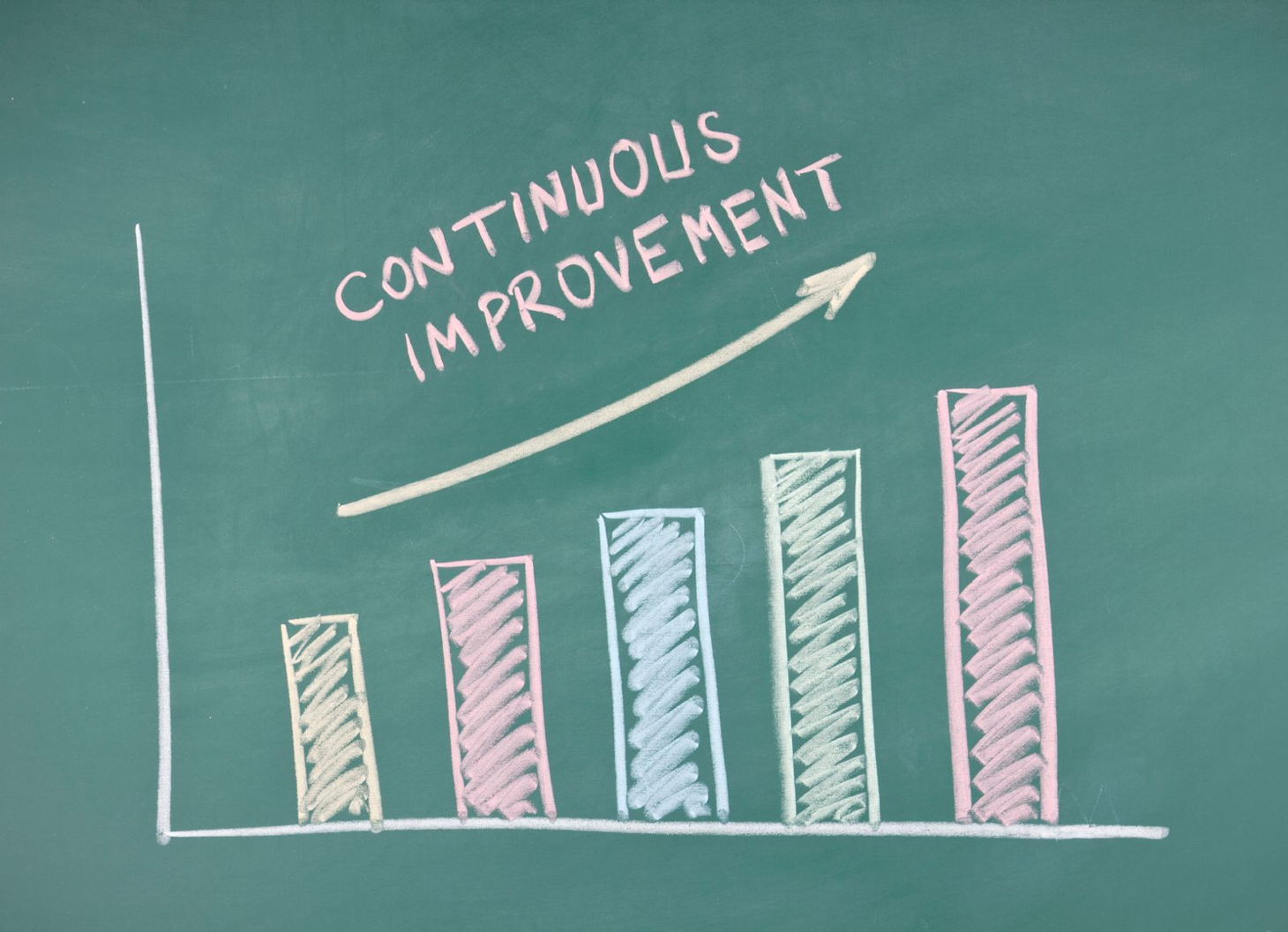
During the Second World War, U.S. government initiated an improvement programme “Training Within Industry” with aims of providing education regarding the importance of continuous improvement (CI). After the war, CI was taught to post-war Japan through works of Deming and Juran (Shingo and Robinson, 1990). Based on those lectures, Japanese developed their own way of CI thinking, nowadays known as kaizen (Imai, 1986).
Defining Continuous Improvement
Some suggest that CI is fork of the existing quality initiatives (TQM for example), while others suggest that it is a standalone approach to achieving excellence (Gallagher et al., 1997; Caffyn, 1999; Oakland, 2001). Let’s take a look at some definitions of CI:
Principle of improvement. – Lillrank and Kano (1989)
A company-wide process of focused and continuous incremental innovation. – Bessant et al. (1994)
A philosophy consisting of improvement initiatives that increase successes and reduce failures. – Juergensen (2000)
Culture of sustained improvement targeting the elimination of waste in all systems and processes of an organization. – Bhuiyan and Baghel (2005)
Core principles of Continuous Improvement
Berger (1997) uses work of Imai (1986) to map out three core features of CI.
Principle 1 – Process orientation
Kaizen is process-oriented, i.e. before results can be improved, processes must be improved, as opposed to result-orientation where outcomes are all that counts.
Principle 2 – Improving and maintaining standards
Lasting improvements can only be achieved if innovations are combined with an ongoing effort to maintain and improve standard performance levels.
Principle 3 – People orientation
Kaizen is people-oriented and should involve everyone in the organization from top management to workers at the shop floor. Further more, Kaizen is based on a belief in people’s inherent desire for quality and worth, and management has to believe that it is going to “pay” in the long run.
Implementing Continous Improvement
Bhuiyan and Baghel (2005) have identified three levels at which CI is usually implemented, and suggest that implementation should be done at all levels in order to maximize gains. Three aforementioned levels are management, group and individual level. Although CI has been developed in organizations with highly standardized products and processes, it can be applied in various work environments. Berger (1997) classifies five organizational designs (Table 1) for CI based on dimensions of task design (individual or integrated) and improvement task (parallel or integrated).
Table 1: Classifications of organizational design for CI
Organizational design | Description |
---|---|
Quality control circles | A group of workers who do the same or similar work, who meet regularly to identify, analyze and solve work-related problems |
Organic CI | Multifunctional work groups integrated with improvement activities |
Expert task force CI | Temporary expert task force |
Wide-focus CI | Combination of organic CI and expert task force CI for temporary operations |
Individual CI | Individuals present ideas, specialists implement them |
A set of generic CI behaviours has been identified in works by Caffyn (1999) and Bhuiyan and Baghel (2005). Those behaviours are considered to be the fundamentals for development of CI capability within an organization, regardless of its type or size. These elements are as follows:
- Employee demonstrates awareness and understanding of the organization’s aims and objectives
- Individual groups use the organization’s strategic goals and objectives to focus and prioritize the improvement activity
- The enabling mechanisms used to encourage involvement in CI are monitored and developed
- Ongoing assessment ensures that the organization’s structure, systems and procedures, and the approach and mechanism used to develop CI, constantly reinforce and support each other
- Managers at all levels display active commitment to, and leadership of, CI
- Throughout the organization people engage proactively in incremental improvement
- There is effective working across internal and external boundaries at all levels
- People learn from their own and from other’s experience, both positive and negative
- The learning of individuals and groups is captured and deployed
- People are guided by a shared set of cultural value underpinning CI as they go about their everyday work
Juergensen (2000) proposes seven critical concepts (Figure 1) for successful CI practices which should be applied cyclically. These concepts are sequenced strategically and appropriately as follows:
- Leaders accept that improvement is necessary
- Leaders agree on a proven continuous improvement process and approach
- Leaders engage and educate a guiding coalition of key stakeholders to lead improvement initiatives
- Leaders work with key stakeholders to define improvement aims, initiatives, and values
- Key stakeholders lead the design of improvement solutions
- Key stakeholders lead the implementation and appraisal of improvement solutions
- Leaders and stakeholders sustain the continuous improvement cycle
The best known CI methodologies, according to Bhuiyan and Baghel (2005), are lean manufacturing, six sigma, the balanced scorecard and lean six sigma. I’ll write more about Lean, Six Sigma, and Lean Six Sigma in future posts.
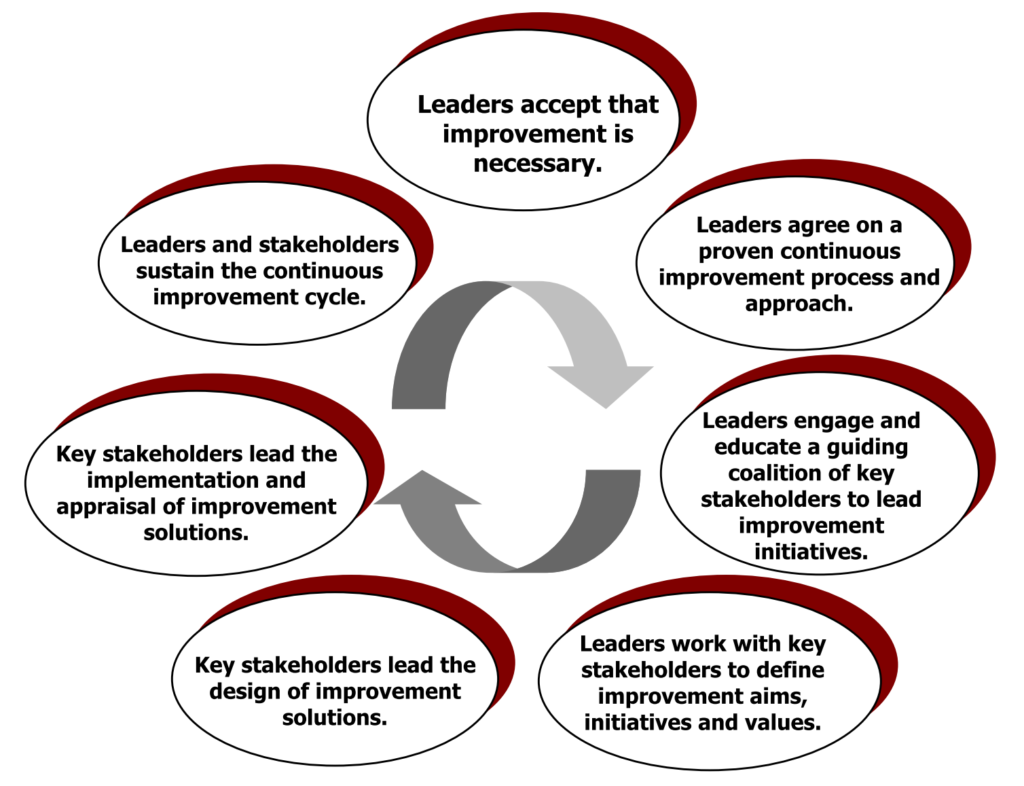
Redefining Continuous Improvement
During my literature review of Continuous Improvement, I found most definitions of it lacking. Conceptual definitions should show evidence of inclusivity, exclusivity, differentiability, clarity, communicability, consistency and parsimony (Hempel, 1970). Based on conducted literature review, I propose a new definition for Continuous Improvement:
Continuous improvement is a company-wide proactive approach to improvement utilizing incremental and breakthrough changes with aim of achieving business excellence. – Pešec (2012)
Key points of proposed definition are:
- company-wide,
- proactive,
- incremental changes,
- breakthrough changes, and
- business excellence.
With terms company-wide and proactive it is emphasized that improvement should be an organizational effort actively searching for improvement opportunities. Terms incremental changes and breakthrough changes emphasize that itinerary for improvement should be both short and long term. Instituting a quality culture with emphasis on incremental improvements supports innovations achieved by breakthrough changes. If changes are only incremental there is danger of losing opportunities due to lack of innovations, while focusing only on breakthrough changes there is danger of losing opportunities due to unsustainable innovations. Hence, synergy between incremental and breakthrough improvements would yield better results. Term business excellence emphasizes that opportunities for improvement should be sought in all elements and at all levels of business, from operations to management, and that ultimate goal is achieving excellence.
Concluding Remarks
In this post I presented several definitions of Continuous Improvement, three core principles that Continuous Improvement shares with Kaizen, ten generic behaviours you need to develop Continuous Improvement capabilities within your organisation and seven critical concepts for successful Continuous Improvement practices. At the end I propose a new definition for Continuous Improvement, in an attempt to satisfy Hempel’s (1970) requirements for conceptual definitions.
References
Berger, A., 1997. Continuous improvement and kaizen: standardization and organizational designs. Integrated manufacturing systems, 8(2), pp.110-117.
Bessant, J., Caffyn, S., Gilbert, J., Harding, R. and Webb, S., 1994. Rediscovering continuous improvement. Technovation, 14(1), pp.17-29.
Bhuiyan, N. and Baghel, A., 2005. An overview of continuous improvement: from the past to the present. Management Decision, 43(5), pp.761-771.
Caffyn, S., 1999. Development of a continuous improvement self-assessment tool. International Journal of Operations & Production Management, 19(11), pp.1138-1153.
Gallagher, M., Austin, S. and Caffyn, S., 1997. Continuous Improvement in Action: The Journey of Eight Companies: Strategies for Successful Implementation and Operation. Kogan Page.
Hempel, C.G., 1970. Methods of concept formation in science. Formations of the Unity of Science. University of Chicago Press, Chicago, IL.
Imai, M., 1986. Kaizen (Ky’zen), the key to Japan’s competitive success. Random House Business Division.
Juergensen, T., 2000. Continuous improvement: Mindsets, capability, process, tools and results. Unpublished manuscript.
Lillrank, P.M. and Kano, N., 1989. Continuous improvement: quality control circles in Japanese industry (No. 19). Center for Japanese Studies University of Michigan.
Oakland, J.S., 2001. Total organizational excellence: Achieving world-class performance. Routledge.
Pešec, B., 2012. Implementing Lean Six Sigma: The effective integration of two improvement methodologies. Specialization project, Norwegian University of Science and Technology.
Shingo, S., and Robinson, A., 1990. Modern approaches to manufacturing improvement : the Shingo system. Productivity Press.
This article is a part of Quality Management series:
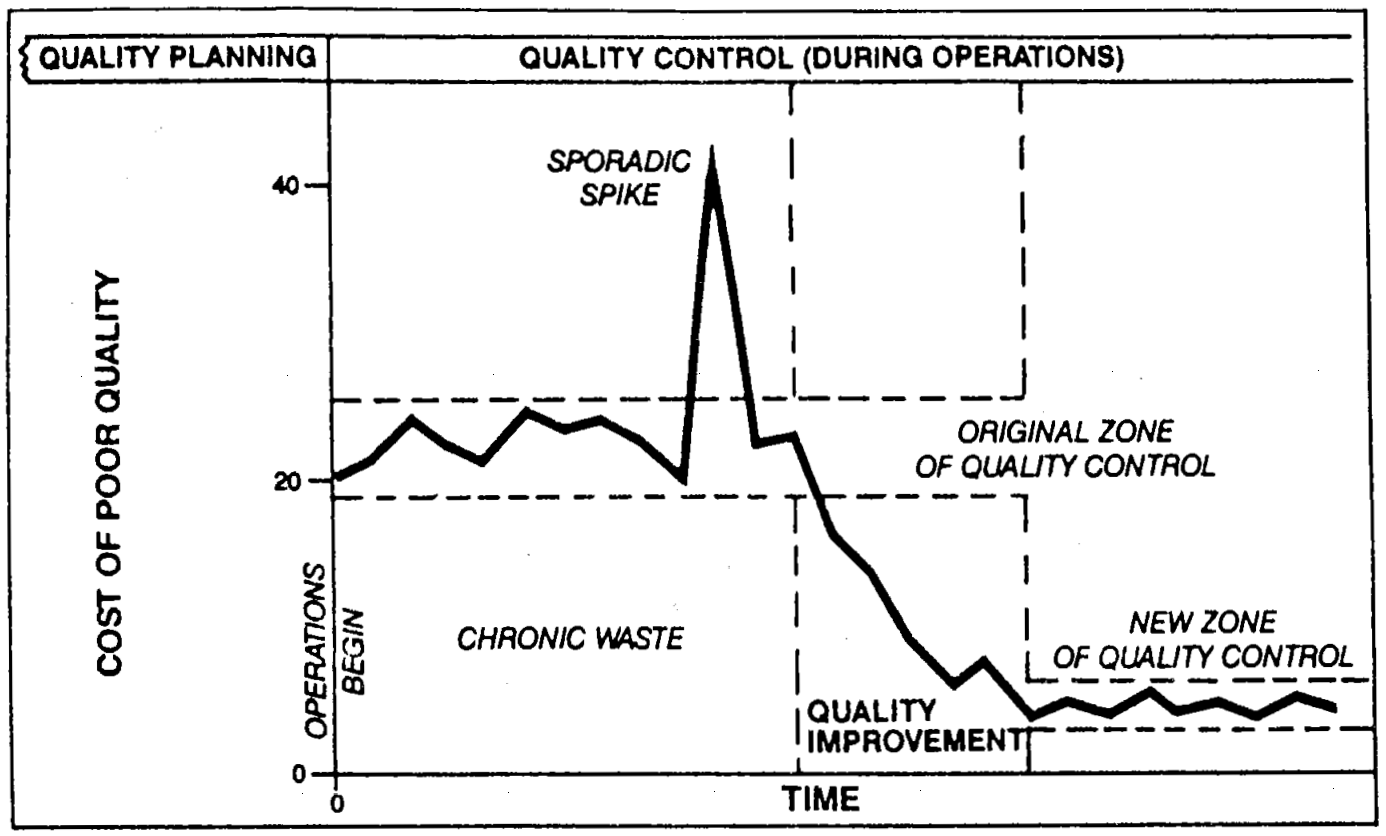
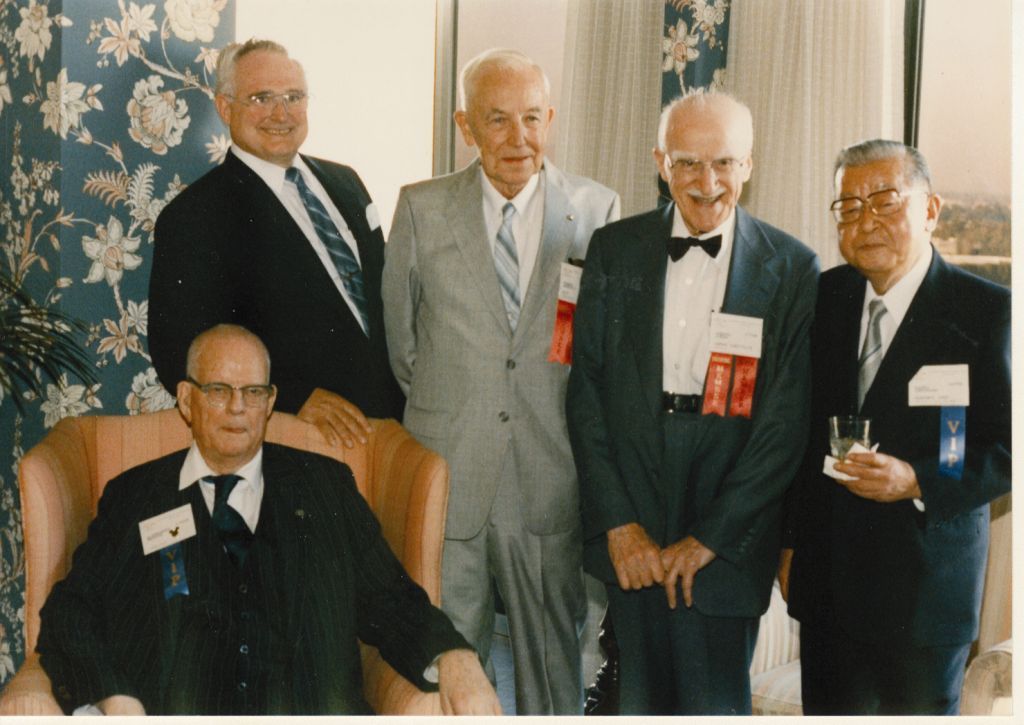
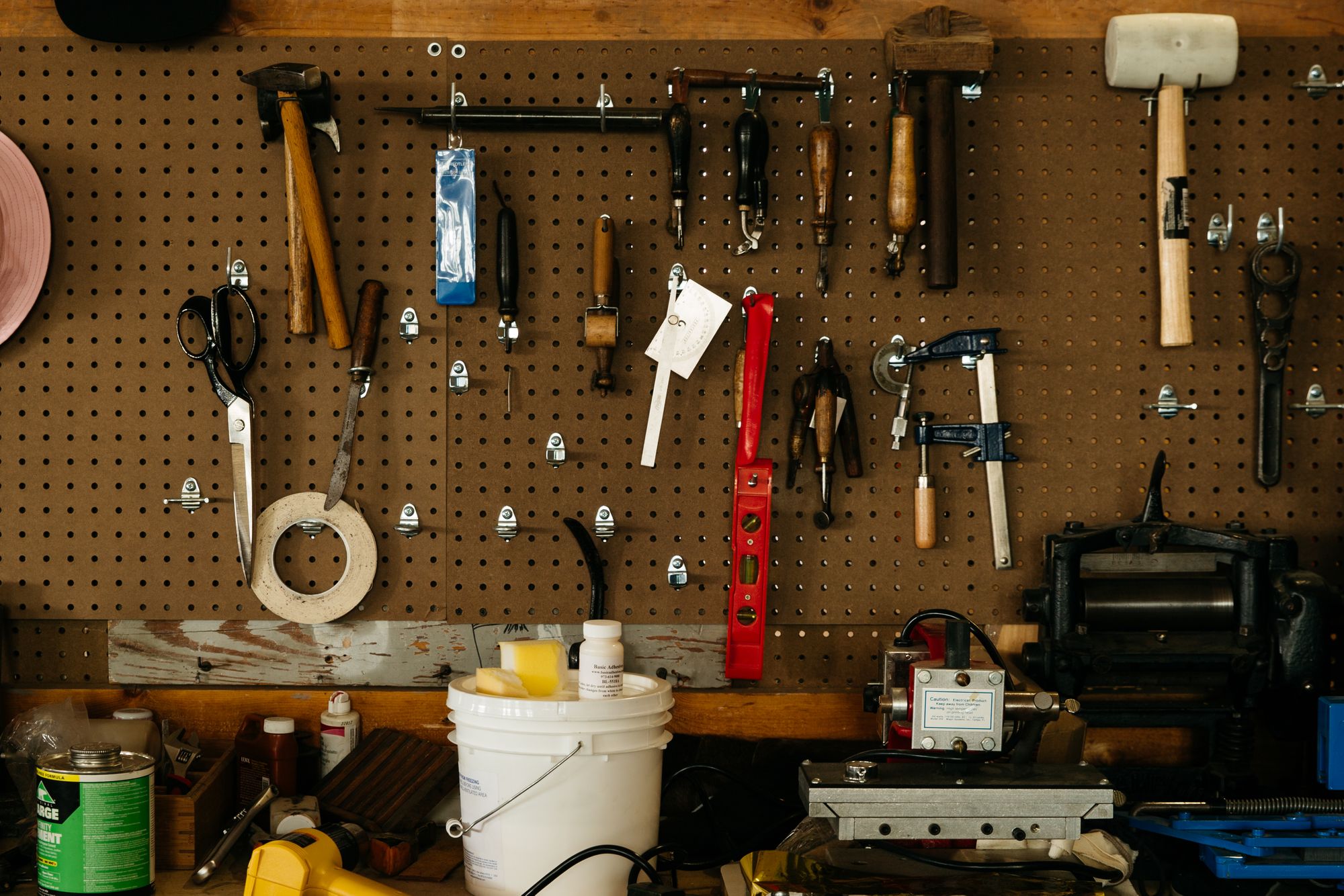
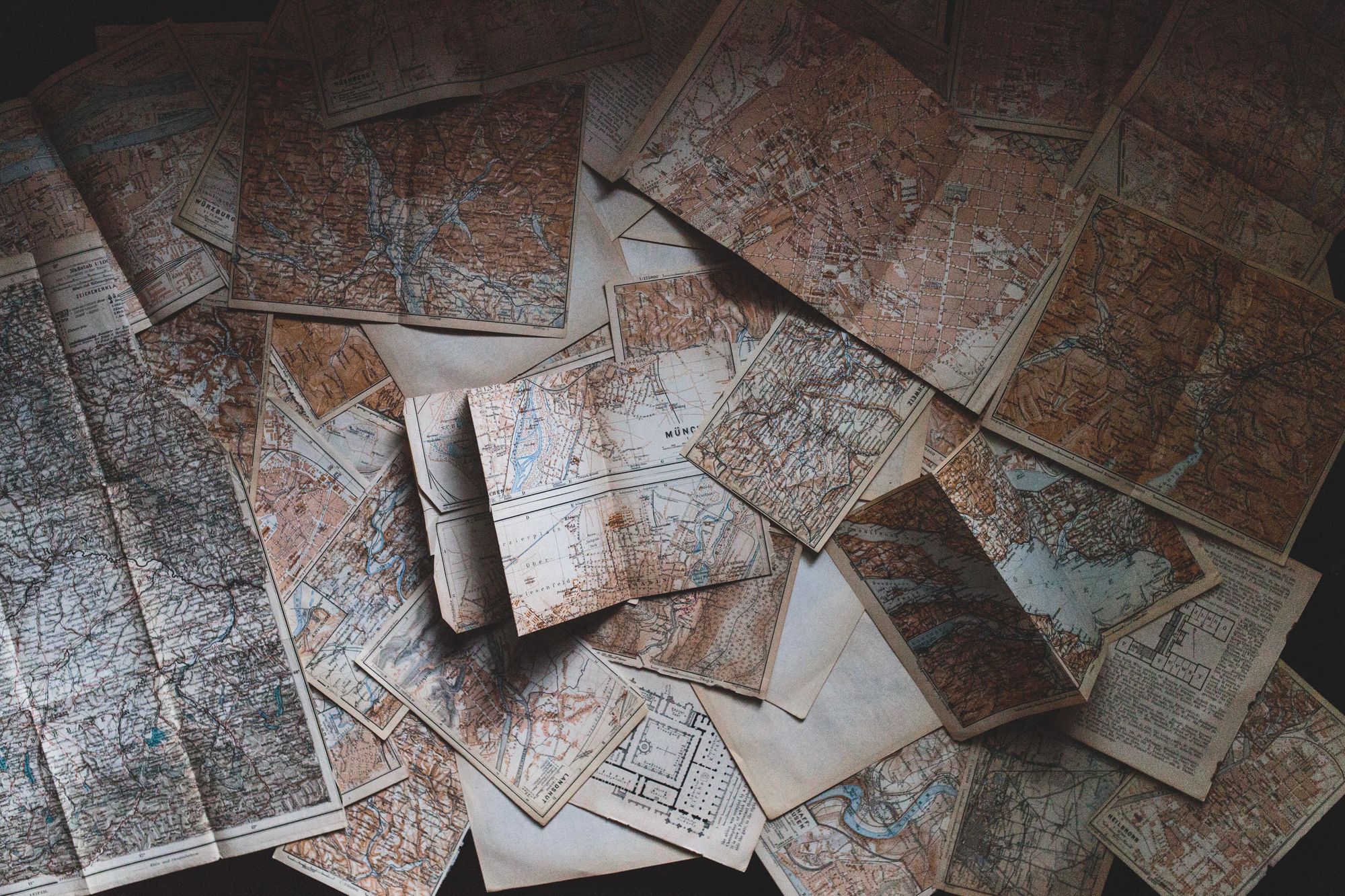
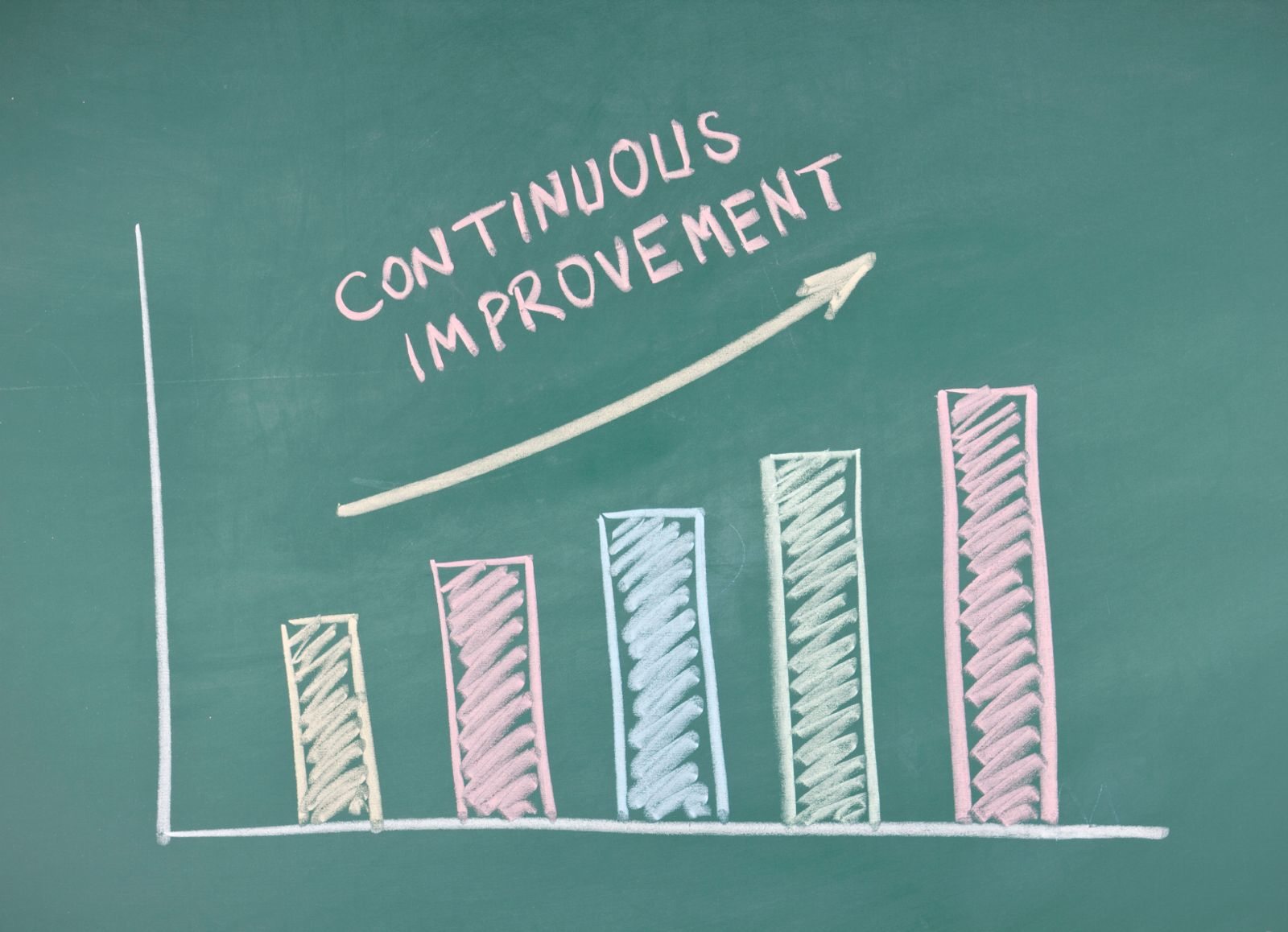
Bruno Unfiltered
Subscribe to get the latest posts delivered right to your inbox. No spam. Only Bruno.