Quality Philosophers
Deming, Juran, Ishikawa, and Crosby changed the world of quality management forever. These are their most significant contributions.
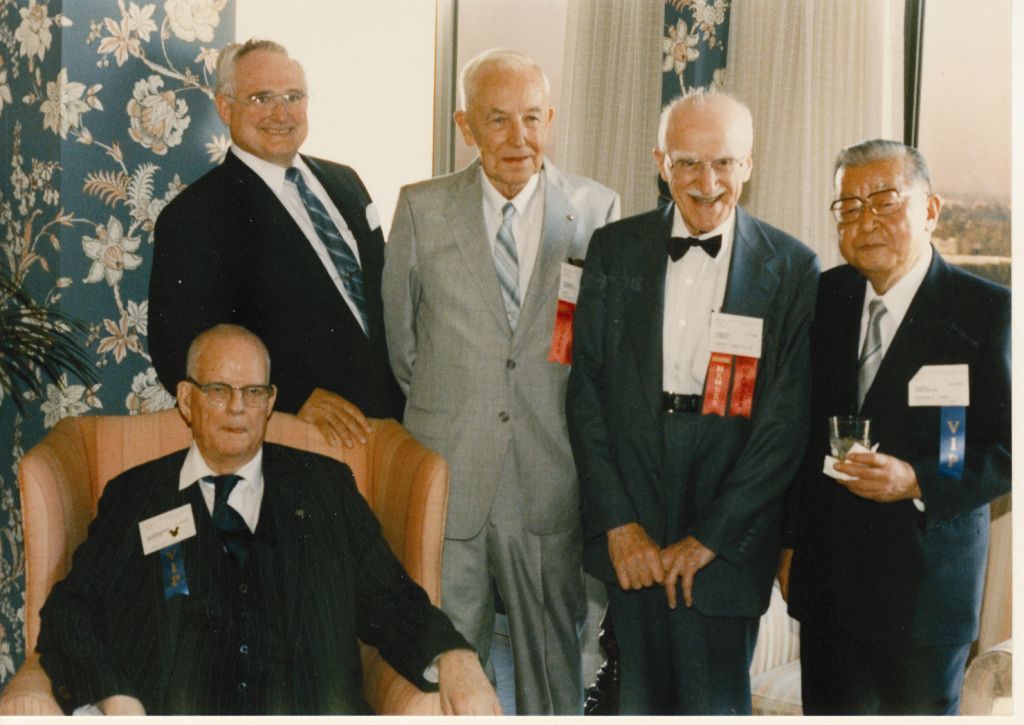
Previously presented definitions of quality could be considered new, but philosophy of quality is far from new. Well known Greek philosopher and polymath Aristotle considered qualities as hylomorphically formal attributes, and described four types of qualitative opposites: correlatives, contraries, privatives and positives (Whitaker, 1996). Hylomorphism is a philosophical theory developed by Aristotle, which conceives substance as a compound of matter and form.
This post presents some of the philosophers who are considered as the greatest contributors to quality management thinking. Their work is presented concisely, summarising their major contributions.
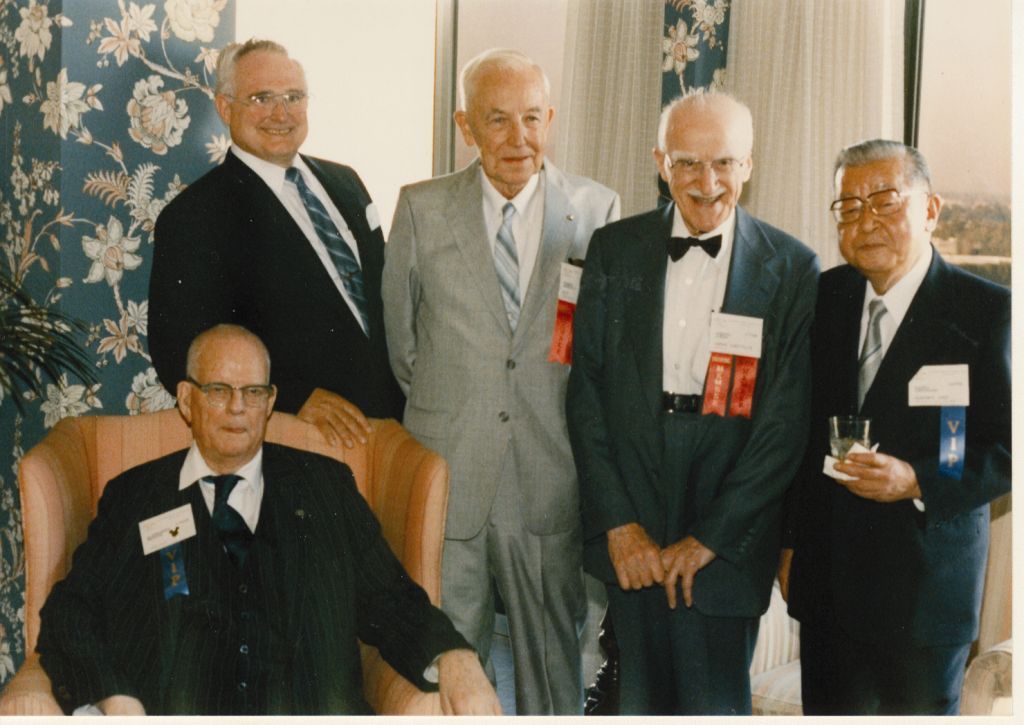
William Edwards Deming
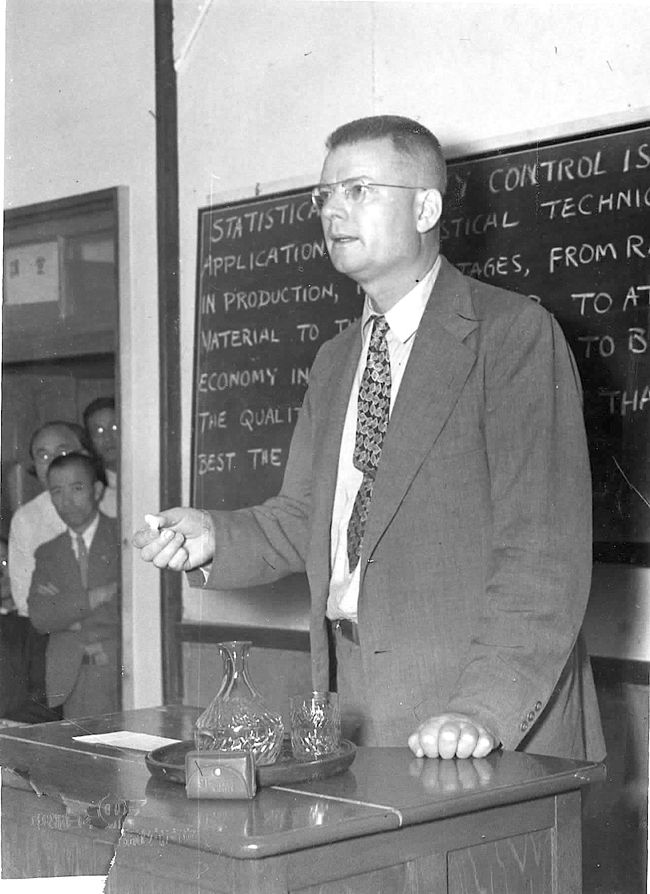
William Edwards Deming is considered to be the pioneer and the founder of the quality movement (Graeme, 2011; Goetsch and Davis, 2014). After Second World War he was involved in planning of the Japanese Census. At that time Japanese engineers were studying Shewart’s methods and techniques. Since Deming was a student of Walter Andrew Shewhart, they decided to invite him help them rebuild the Japanese economy.
Deming’s work in Japan resulted in Japanese factories dominating the manufacturing sector with high quality and low cost. The domination lasted for approximately two decades, from 1970s to 1990s. Ironically, his methods gained recognition in United States after his death (Deming and Petty, 1991). His major contributions to the quality management field are:
- The Fourteen Points
- The Deadly Diseases
- The System of Profound Knowledge
- Deming Wheel
The Fourteen Points
In Out of the Crisis (1982), Deming summarizes his management philosophy in 14 points for the transformation of traditional management of the organisation:
- Create constancy of purpose
- Adopt the new philosophy
- Cease dependence on mass inspection
- Cease award of business on price tag alone
- Improve constantly and forever the system of production and service
- Institute training
- Institute leadership
- Drive out fear
- Break down barriers between departments
- Eliminate slogans, exhortations, and targets
- Eliminate numerical quotas for the workforce and numerical goals for management
- Remove barriers that deny people pride of workmanship
- Institute a vigorous program of education and self-improvement
- Take action to accomplish the transformation
The Deadly Diseases
The deadly diseases represent threats to successful implementation of the aforementioned Fourteen Points of transformation, preventing companies from achieving world class excellence:
- Lack of constancy of purpose
- Emphasis on short-term profits
- Evaluation by performance, merit rating, or annual review of performance
- Mobility of management
- Running a company on visible figures alone
- Excessive medical costs
- Excessive costs of warranty, fuelled by lawyers who work for contingency fees
In addition to the major threats represented, he also laid out minor threats:
- Neglecting long-range planning
- Relying on technology to solve problems
- Seeking examples to follow rather than developing solutions
- Excuses, such as “our problems are different”
- Obsolescence in school that management skill can be taught in classes
- Reliance on quality control departments rather than management, supervisors, managers of purchasing, and production workers
- Placing blame on workforces who are only responsible for 15% of mistakes where the system designed by management is responsible for 85% of the unintended consequences
- Relying on quality inspection rather than improving product quality
The System of Profound Knowledge
The System of Profound Knowledge is the basis for application of The Fourteen Points of transformation. With its four points it advocates holistic approach: (1) appreciation of a system, (2) knowledge of variation, (3) theory of knowledge and (4) knowledge of psychology.
The prevailing style of management must undergo transformation. A system cannot understand itself. The transformation requires a view from outside. The aim of this chapter is to provide an outside view—a lens—that I call a system of profound knowledge. It provides a map of theory by which to understand the organizations that we work in. – Deming (1982)
Deming Wheel
Deming Wheel was based on the Shewhart Cycle (Moen and Norman, 2010). In his book (Shewart and Deming, 1986), Shewart presented the first version of Shewart circle, consisting of three steps: specification, production and inspection. In 1951 Deming modified it for his lecture at the Japanese Union of Scientists and Engineers (JUSE), presenting it with four steps: design, production, sale and research. Japanese executives called it Deming Wheel, and transformed it into PDCA cycle (Imai, 1986). In his later work Deming modified PDCA cycle to PDSA cycle, substituting Check phase with Study phase (Deming, 1982). PDCA cycle is still used today, both in original form and in its variations.
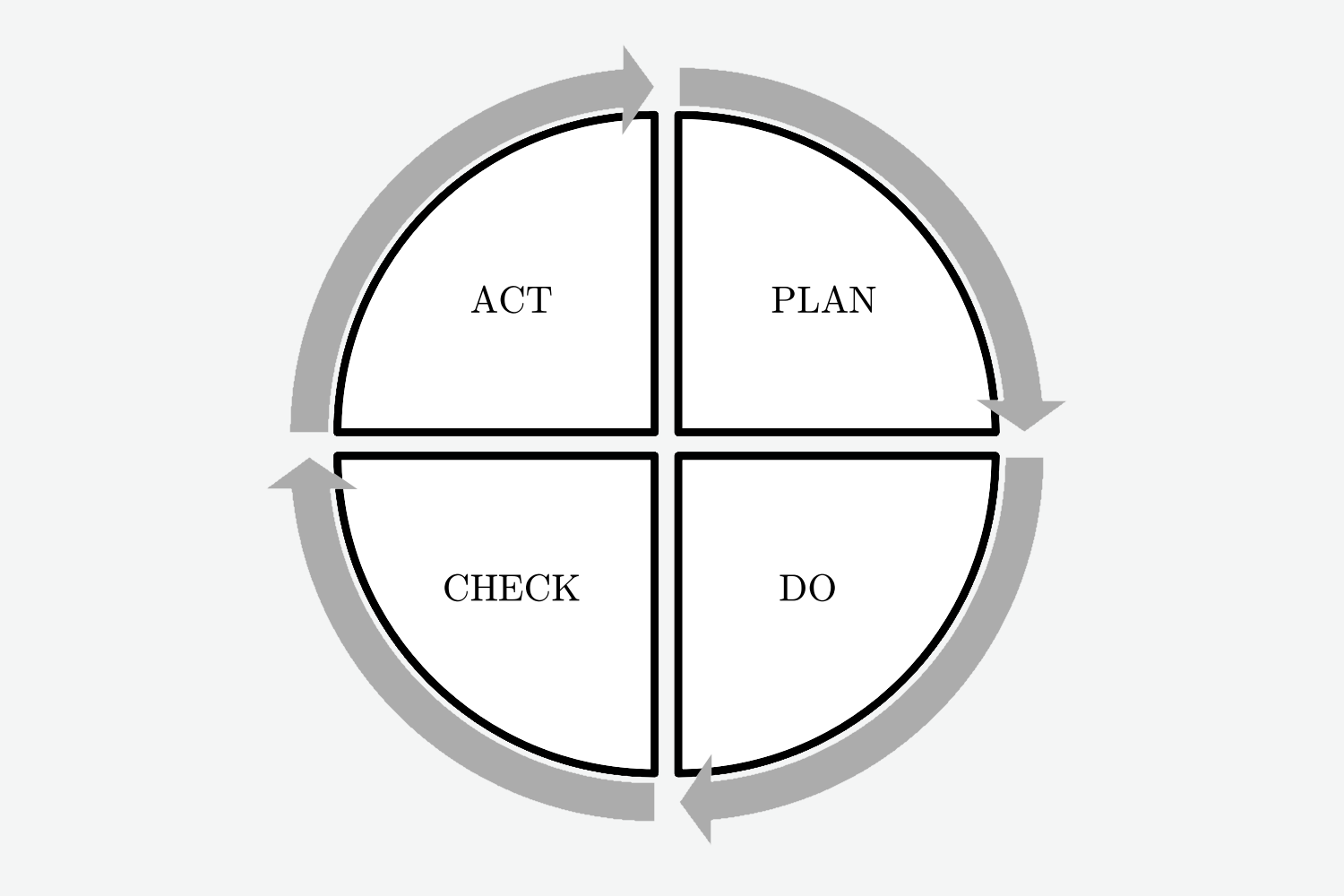
Joseph Moses Juran
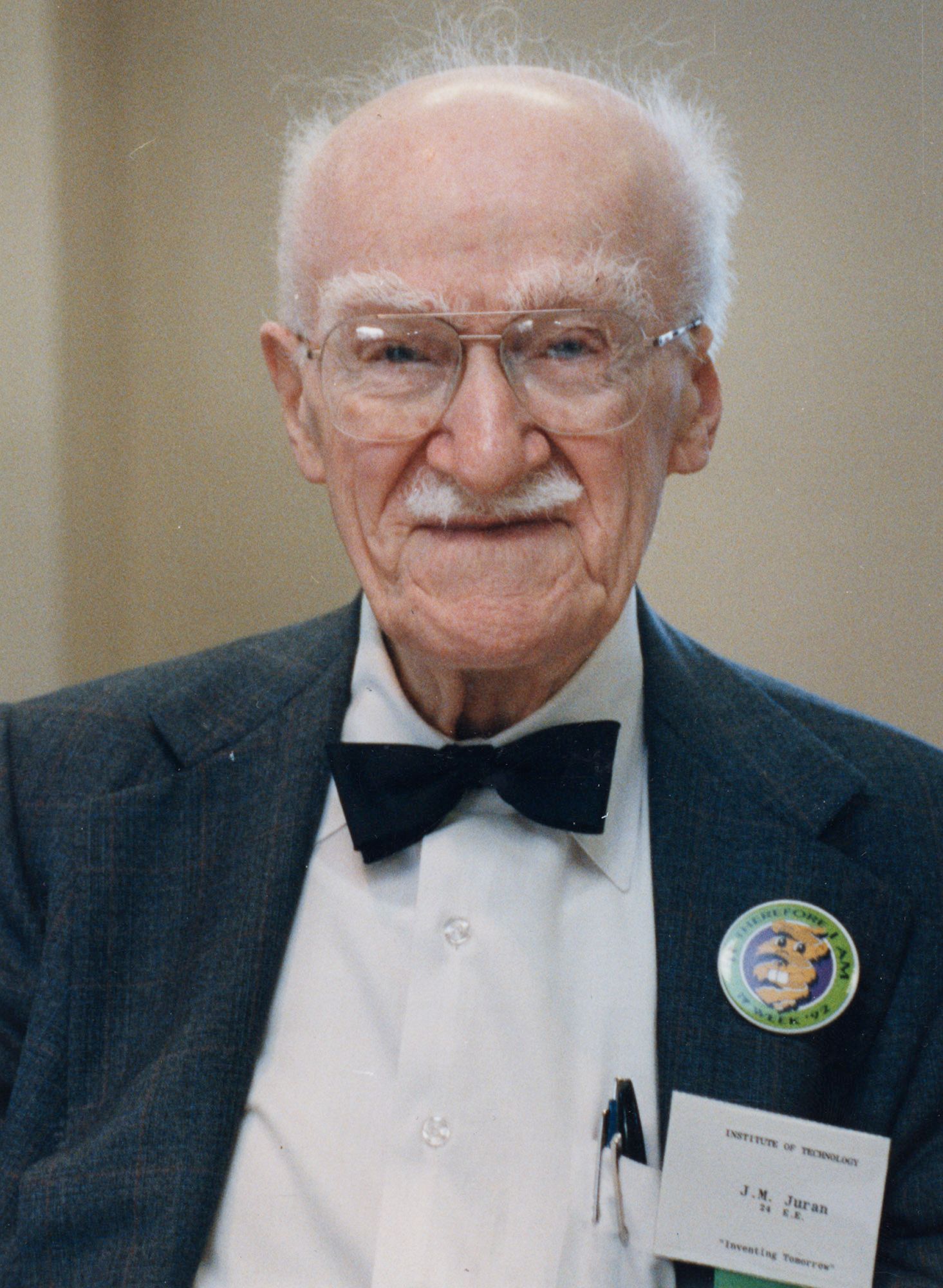
While Deming focused more on the statistical approach to control, Juran focused on managing for quality. Although he was also invited to help the Japanese rebuild their economy he never collaborated with Deming.
The Quality Trilogy, cost of poor quality (COPQ) approach, popularisation of the Pareto principle and Quality Circles, and adding human dimension to quality management are considered to be his major contributions (Phillips-Donaldson, 2004). In his work he advocated embedding quality into the corporate culture, creating quality habit, through a four-stage approach (Juran and Godfrey, 1999):
- Goals – establish specific goals for an organization
- Plans – detail ways to achieve these goals
- Responsibilities – assign tasks for executing the plans
- Rewards – base rewards on results
The Quality Trilogy
As I’ve written before, Juran was inspired by financial processes of (1) budgeting, (2) cost control, expense control, and (3) cost reduction, profit improvement. He created parallel processes for quality, namely (1) quality planning, (2) quality control, and (3) quality improvement. I recommend reading Juran’s original article: A universal approach to managing for quality.
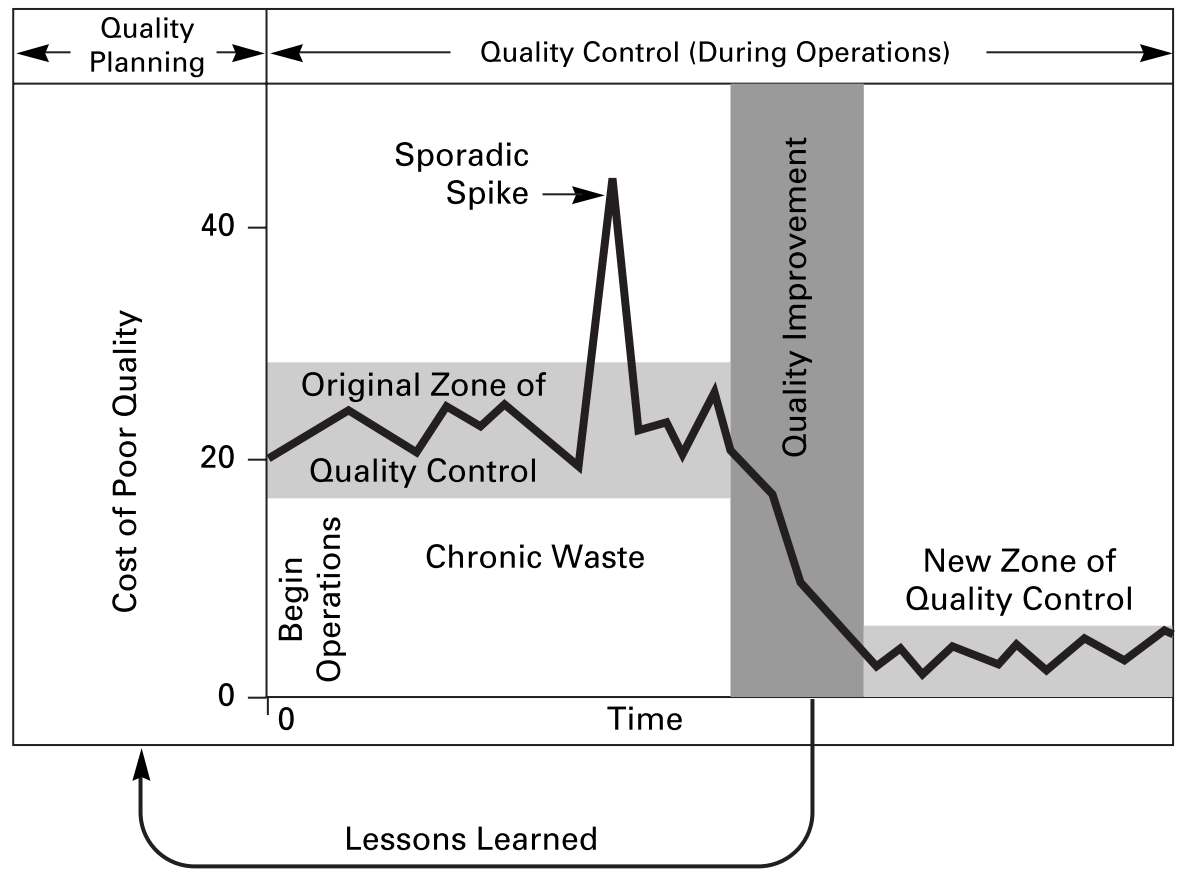
Cost of Poor Quality
In the 1950s Juran developed a Cost of Quality approach (Feigenbaum, 1961; Juran and Godfrey, 1999), which enabled companies to asses the costs related to quality. He divided cost of poor quality into cost of nonconformities, cost of inefficient processes and cost of lost opportunities for sales revenue (Figure 6).
Some of the benefits are:
- quality issues are translated into financial measures,
- indicates the scale of opportunity presented by current poor quality performance, and
- effective measurement of improvement.
Some of the issues are:
- inaccurate costs,
- requires trust to be effective,
- re-calculation has to be consistent,
- recurring costs,
- there are unknown elements, and
- benefits from cost of quality usage diminish with the maturity of the quality system (Sower et al., 2007).
If you wish to dig more into cost of quality I recommend The Cost of Quality – A Primer by Austenfeld Jr.
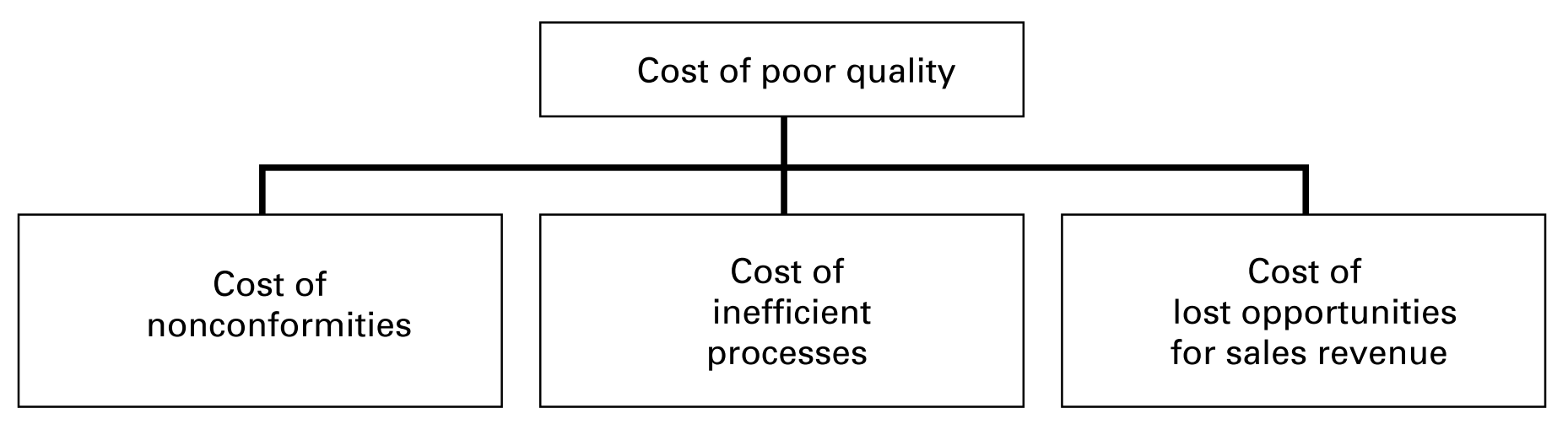
Knowledge transfer
During his work Juran popularised the Pareto principle, named after Italian economist Vilfredo Pareto, and Quality Circles. Juran applied the Pareto principle to the cost of quality, highlighting that costs of failure of control usually account for approximately 80% of total cost of quality. Furthermore, Juran and Godfrey (1999) explain that:
Under the Pareto principle, the vital few projects provide the bulk of the improvement, so they receive top priority. Beyond the vital few are the useful many projects. Collectively they contribute only a minority of the improvement, but they provide most of the opportunity for employee participation. Choice of these projects is made through the nomination-selection process.
Simplest definition of the Pareto principle is as follows:
The Pareto principle (also known as the 80–20 rule, the law of the vital few, and the principle of factor sparsity) states that, for many events, roughly 80% of the effects come from 20% of the causes.
Regarding the Pareto principle, it should be noted that it was based on observation and not on mathematical model. Newman (2005) presents mathematical explanation for Pareto distribution.
Philip Bayard Crosby
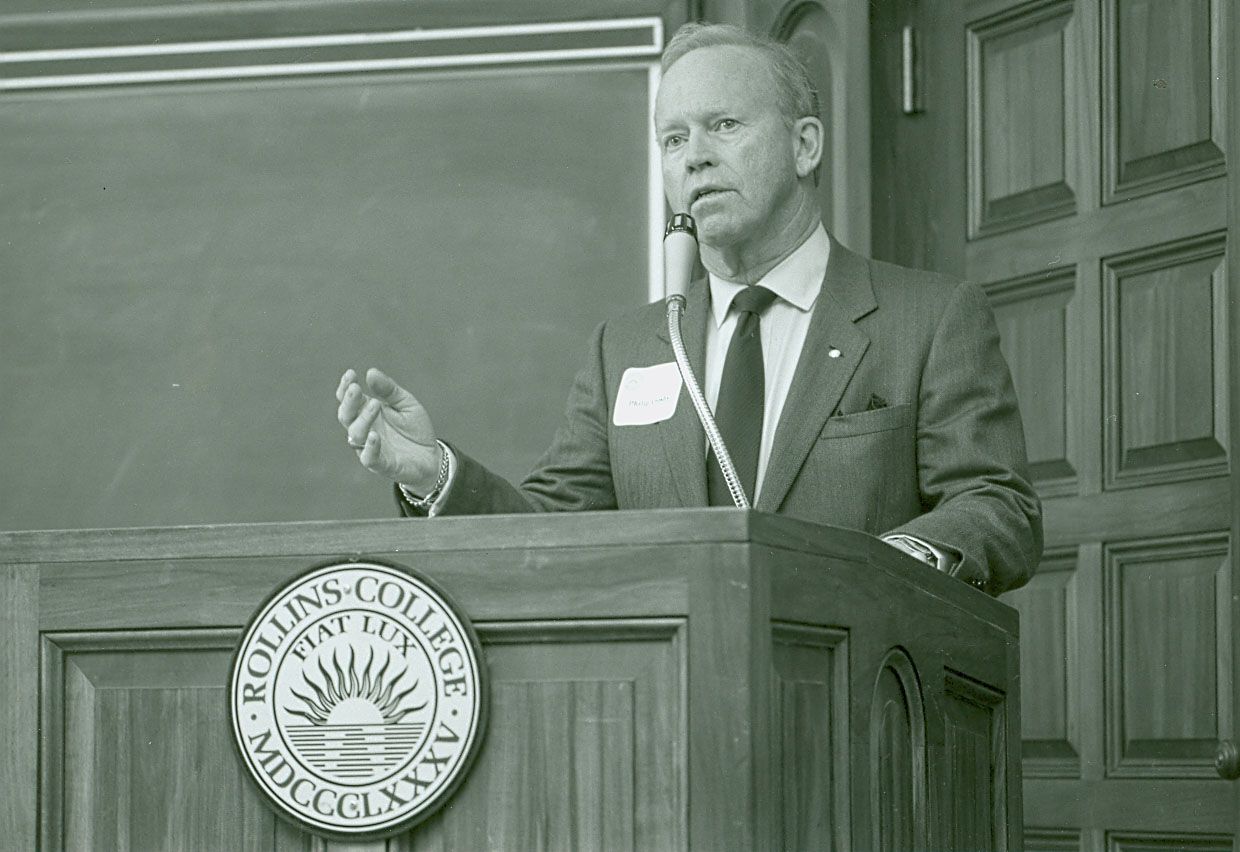
Crosby developed quality is free and zero defects concepts (Crosby, 1980; Harwood, 1993), and believed that appropriate quality management would contribute to growth and survival of a company. He emphasized that investments in the quality program would be significantly lower than saving returns resulting from implementation of such program, hence resulting in free quality. Also, he considered that the costs of quality are as high as 20% of sales. Quality crisis in North America occurred between 1970s and 1980s, due to increased market share of Japanese high quality products. In those times, Crosby proposed DRIFT (Do It Right the First Time) principle, supported by four major principles. Those principles were (Creech, 1994):
- The definition of quality is conformance to requirements (requirements meaning both the product and the customer’s requirements)
- The system of quality is prevention
- The performance standard is zero defects (relative to requirements)
- The measurement of quality is the price of non-conformance
Besides aforementioned principles, he also proposed a 14-point plan for improving quality (Crosby, 1980; Crosby, 1992):
- Management must be clearly committed to the importance of quality
- Quality improvement programmes need to be supported by a multifunctional team
- Quality measures need to be in place
- The cost of quality needs to include the price of non-conformance as well as the price of conformance so as to help prioritize action
- Quality awareness needs to be promoted throughout the organization
- Improvements and ideas need to be actioned at the appropriate level of an organization
- The goal is to achieve a position of zero defects
- Education and training should form the basis of any quality programme
- A specific future date should be established as zero-defects days
- Management needs to set goals
- Everyone is to be responsible for identifying the source of defects and errors
- A quality programme should receive public, non-financial recognition
- A quality council should be formed to help share experiences, problems and ideas
- To highlight the never-ending process of quality programmes, companies then need to return again to Step 1
Kaoru Ishikawa
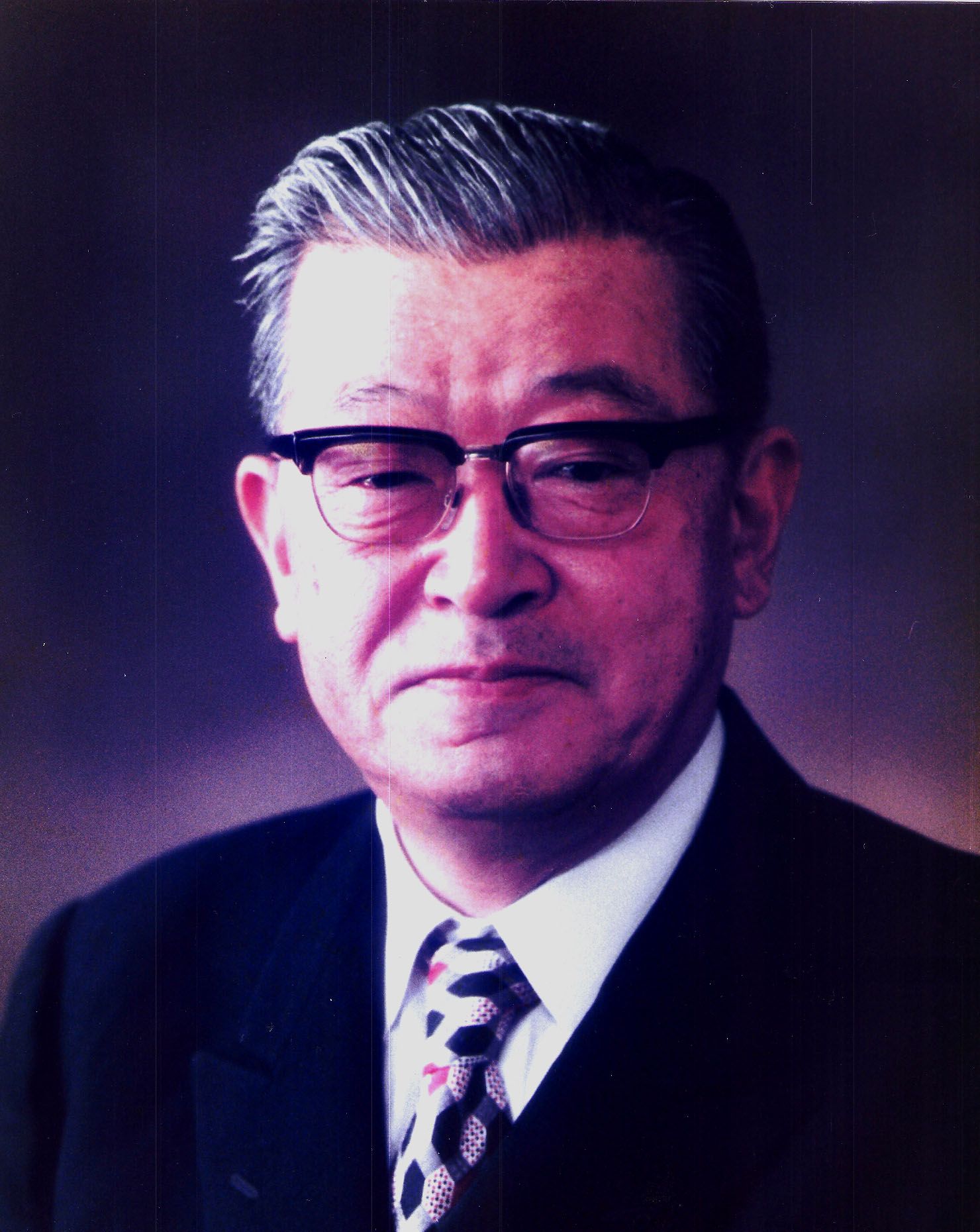
Kaoru Ishikawa is credited for the creation of cause and effect diagram and quality circle concept. In his work Ishikawa (1986) emphasized defining quality from the perspective of the customer and empowering the workforce (Watson, 2004). He believed that quality should come first, and proposed a holistic approach to the quality which he called an integrated quality.
Quality Circles
“Quality Circle” is a small group between three and twelve people who do the same or similar work, voluntarily meeting together regularly for about an hour per week n paid time, usually under the leadership of their own supervisor, and trained to identify, analyse, and solve some of the problems in their work, presenting solutions to management, and where possible, implementing the solutions themselves. – Hutchins (1985)
Juran and Godfrey (1999) compared quality circles with traditional multifunctional teams in terms of purpose, scope and size of project, membership, hierarchical status of members, and continuity. Differences are presented in Table 1.
Table 1: Contrast, quality circles, and multifunctional teams
Feature | Quality circles | Project teams |
---|---|---|
Primary purpose | To improve human relations | To improve quality |
Secondary purpose | To improve quality | To improve participation |
Scope of project | Within a single department | Multidepartmental |
Size of project | One of the useful many | One of the vital few |
Membership | From a single department | From multiple departments |
Basis of membership | Voluntary | Mandatory |
Hierarchical status of members | Typically in the workforce | Typically managerial or professional |
Continuity | Circle remains intact, project after project is completed | Team is ad hoc, disbands after project |
Cause-and-effect diagrams
Cause-and-effect diagrams (also called Ishikawa diagrams, fishbone diagrams, herringbone diagrams, or Fishikawa) are causal diagrams that show the causes of a specific event. – Ishikawa (1986)
Cause-and-effect diagrams are a useful and simple tool for root cause analysis. On the right-hand side of the diagram we have a single effect, usually a problem. From it stems a main line (trunk, spine), from which other lines stem (branches, bones). Every line represents a cause, and it is up to you to decide how deep you want to go. Useful rule of thumb is to categorise causes, e.g. 5M+E (Machine, Method, Material, Man Power, Measurement, and Environment) for manufacturing industry or 4S+E (Surroundings, Suppliers, Systems, Skills, and Environment) for service industry. Figure 9 presents and example with multiple causes and sub-causes.
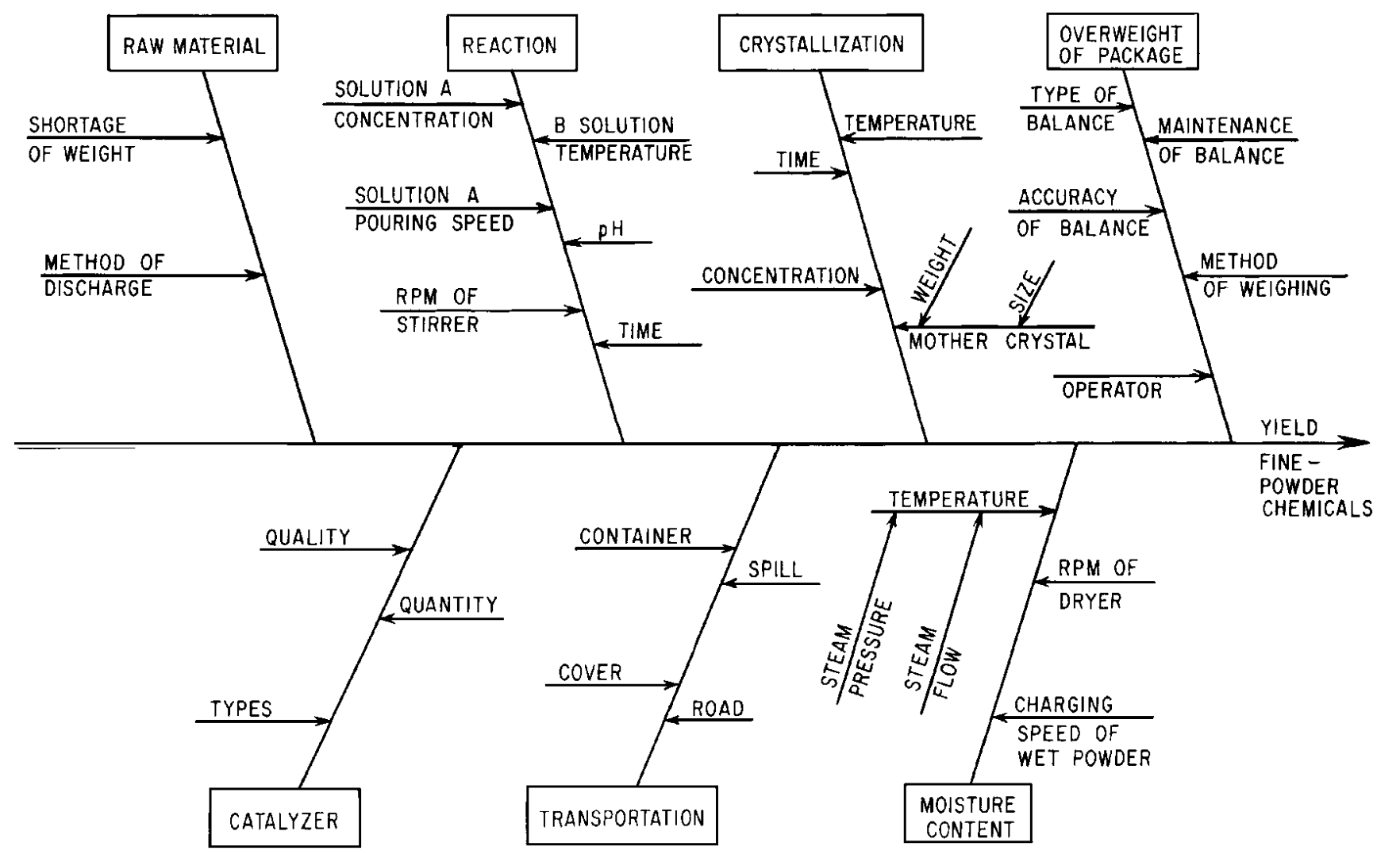
Concluding Remarks
In this post I wrote about some of the most influential figures in the quality management field: William Edwards Deming, Joseph Moses Juran, Philip Bayard Crosby, and Kaoru Ishikawa. Others include Walter Shewart, Armand Vallin Feigenbaum, Genichi Taguchi, Shigeo Shingo, Eliyahu Moshe Goldratt, and Taiichi Ohno. Each of these gurus bodies of work are worth your time, regardless of your industry.
Next post will compare six management systems, Japanese Total Quality Control, Total Quality Management, Deming’s System of Profound Knowledge, Business Process Reengineering, Lean Thinking, and Six Sigma, from quality management perspective.
References
Austenfeld Jr, R.B., 2006. The Cost of Quality – A Primer. 修道商学, 46, pp.149-198.
Creech, B., 1994. The five pillars of TQM : how to make total quality management work for you. Truman Talley Books/Dutton.
Crosby, P.B., 1980. Quality is free: The art of making Quality certain. Signet.
Crosby, P.B., 1992. Completeness: Quality for the 21st century. Penguin.
Deming, W. E., 1982. Out of the Crisis. MIT Press.
Deming, W. E., and Petty, P., 1991. The Deming of America. Petty Consulting/Productions.
Feigenbaum, A. V., 1961. Total Quality Control. McGraw-Hill.
Goetsch, D.L. and Davis, S.B., 2014. Quality Management for Organizational Excellence. Pearson.
Graeme, K., 2011. Quality Management. Ventus Publishing.
Harwood, W. B., 1993. Raise heaven and earth : the story of Martin Marietta people and their pioneering achievements. Simon & Schuster.
Hutchins, D.C., 1985. Quality circles handbook. Nichols.
Imai, M., 1986. Kaizen (Ky’zen), the key to Japan’s competitive success. Random House Business Division, 1986.
Ishikawa, K., 1986. Guide to Quality Control (Tokyo, Asian Productivity Organization). Ann Arbor, MI: UNIPUB.
Juran, J.M. and Godfrey, A.B., 1999. Juran’s Quality Handbook. 5th edition. McGraw-Hill.
Moen, R.D. and Norman, C.L., 2010. Circling back. Quality Progress, 43(11), p.22.
Newman, M.E., 2005. Power laws, Pareto distributions and Zipf’s law. Contemporary physics, 46(5), pp.323-351.
Phillips-Donaldson, D., 2004. 100 years of Juran. Quality progress, 37(5), p.25.
Shewhart, W.A. and Deming, W.E., 1986. Statistical method: from the viewpoint of quality control. Dover.
Sower, V.E., Quarles, R. and Broussard, E., 2007. Cost of quality usage and its relationship to quality system maturity. International Journal of Quality & Reliability Management, 24(2), pp.121-140.
Watson, G., 2004. The legacy of Ishikawa. Quality progress, 37(4), p.54.
Whitaker, C.W.A., 1996. Aristotle’s De interpretatione: contradiction and dialectic. Oxford University Press.
This article is a part of Quality Management series:
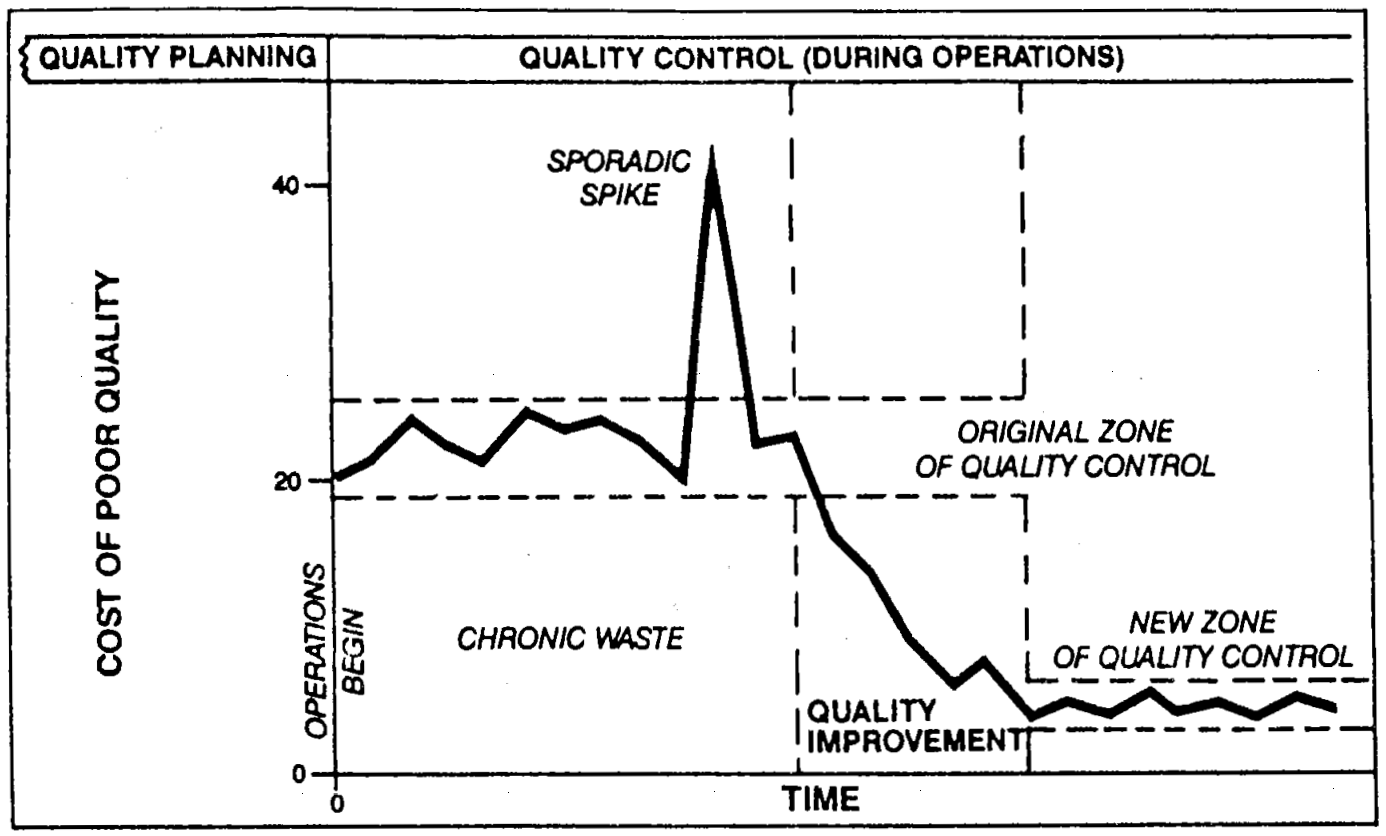
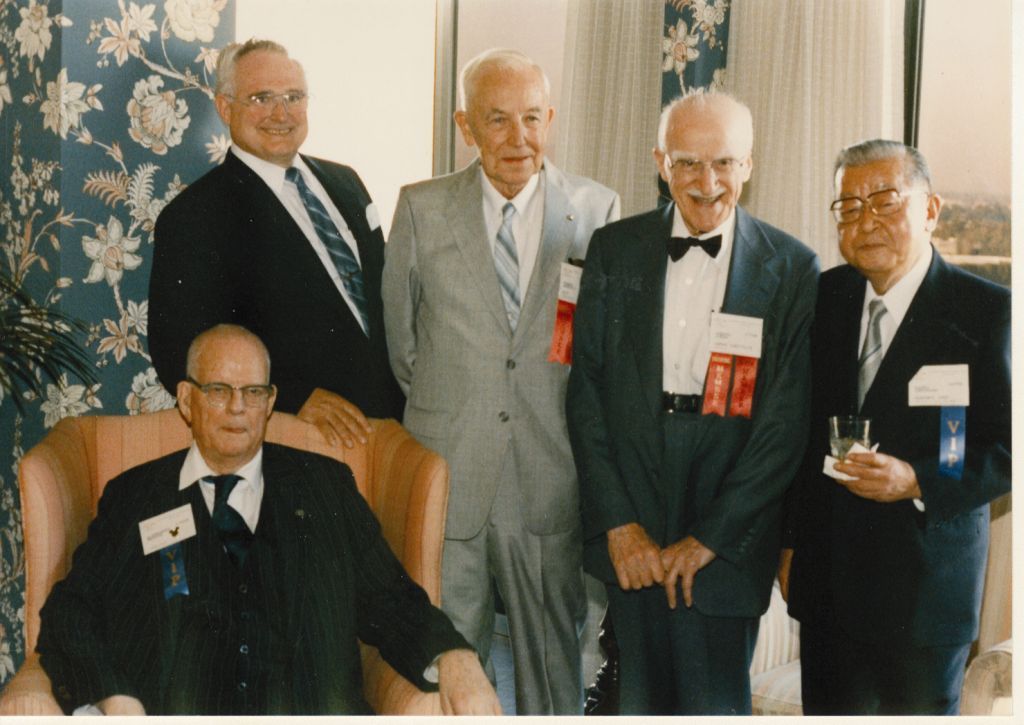
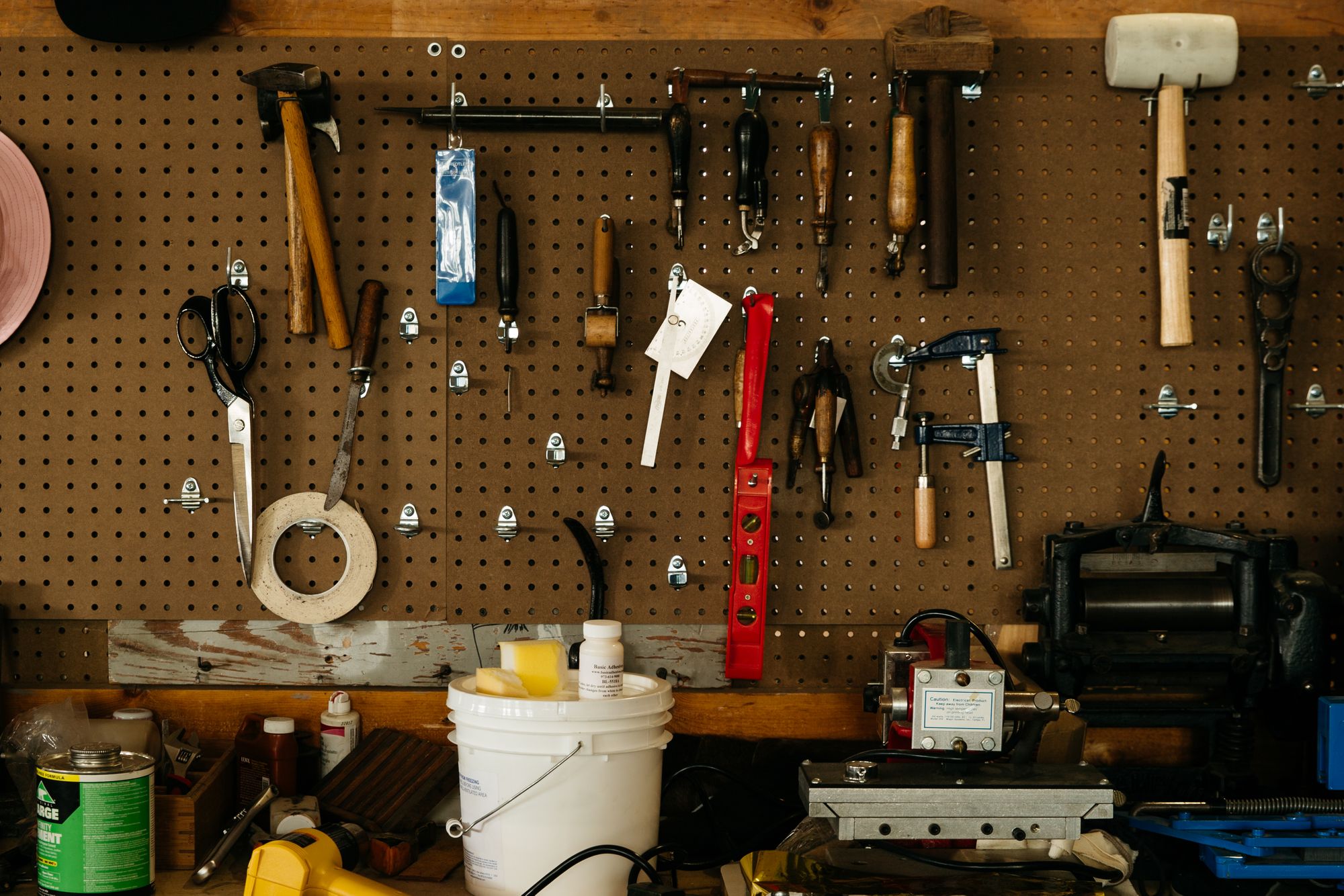
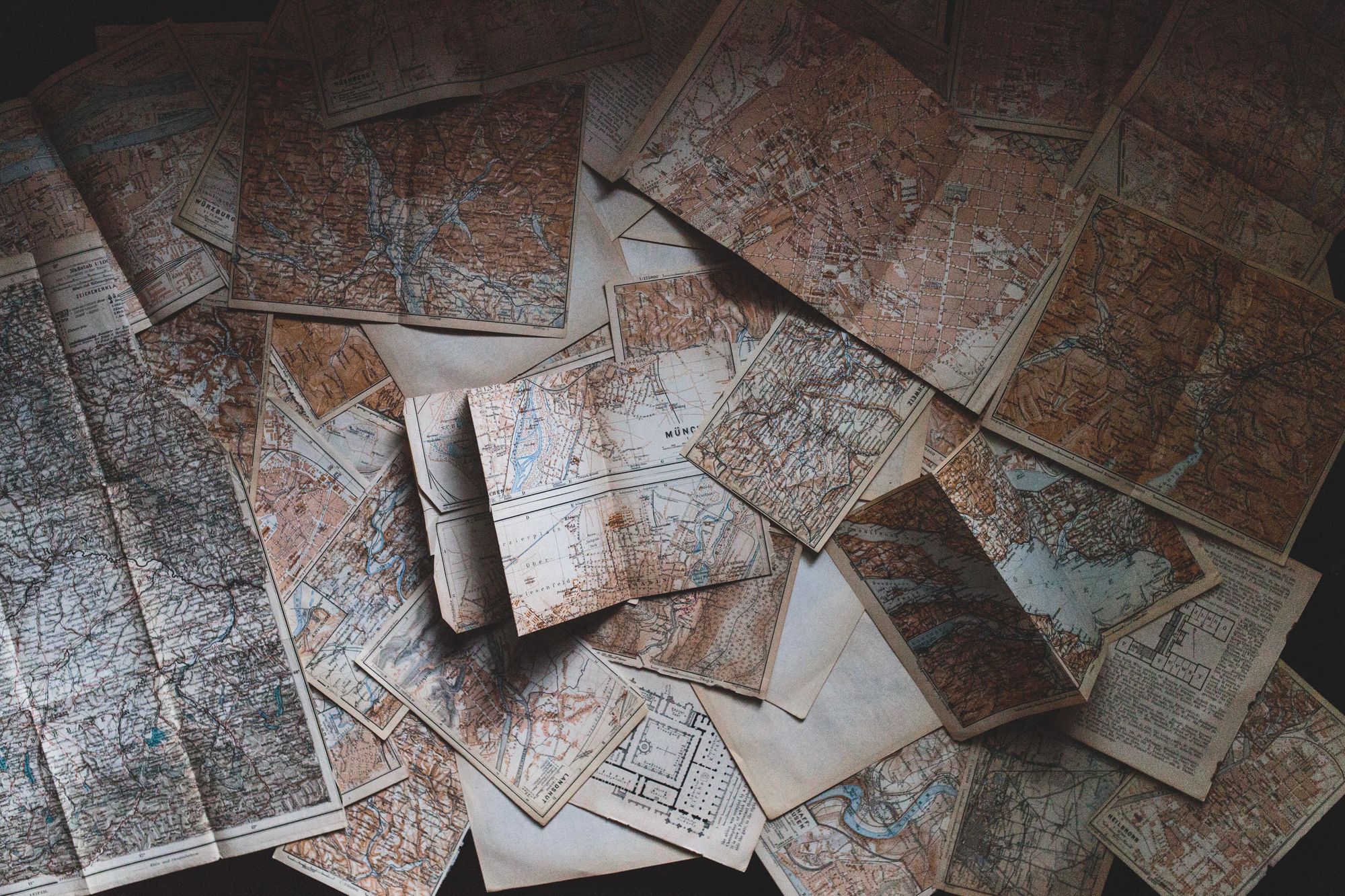
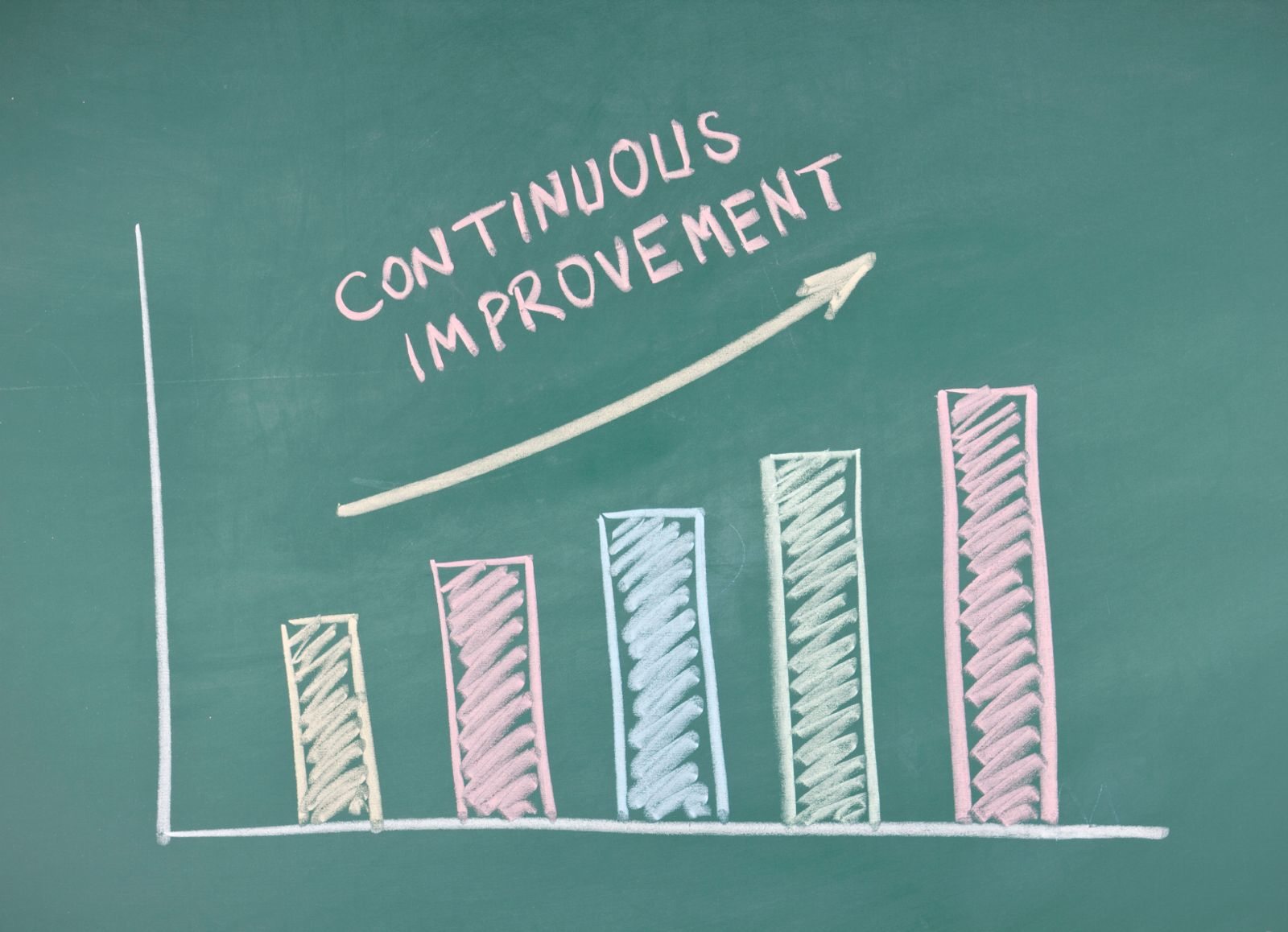
Bruno Unfiltered
Subscribe to get the latest posts delivered right to your inbox. No spam. Only Bruno.