On Managing for Quality
Historical overview of quality movement from inspection to strategic management.
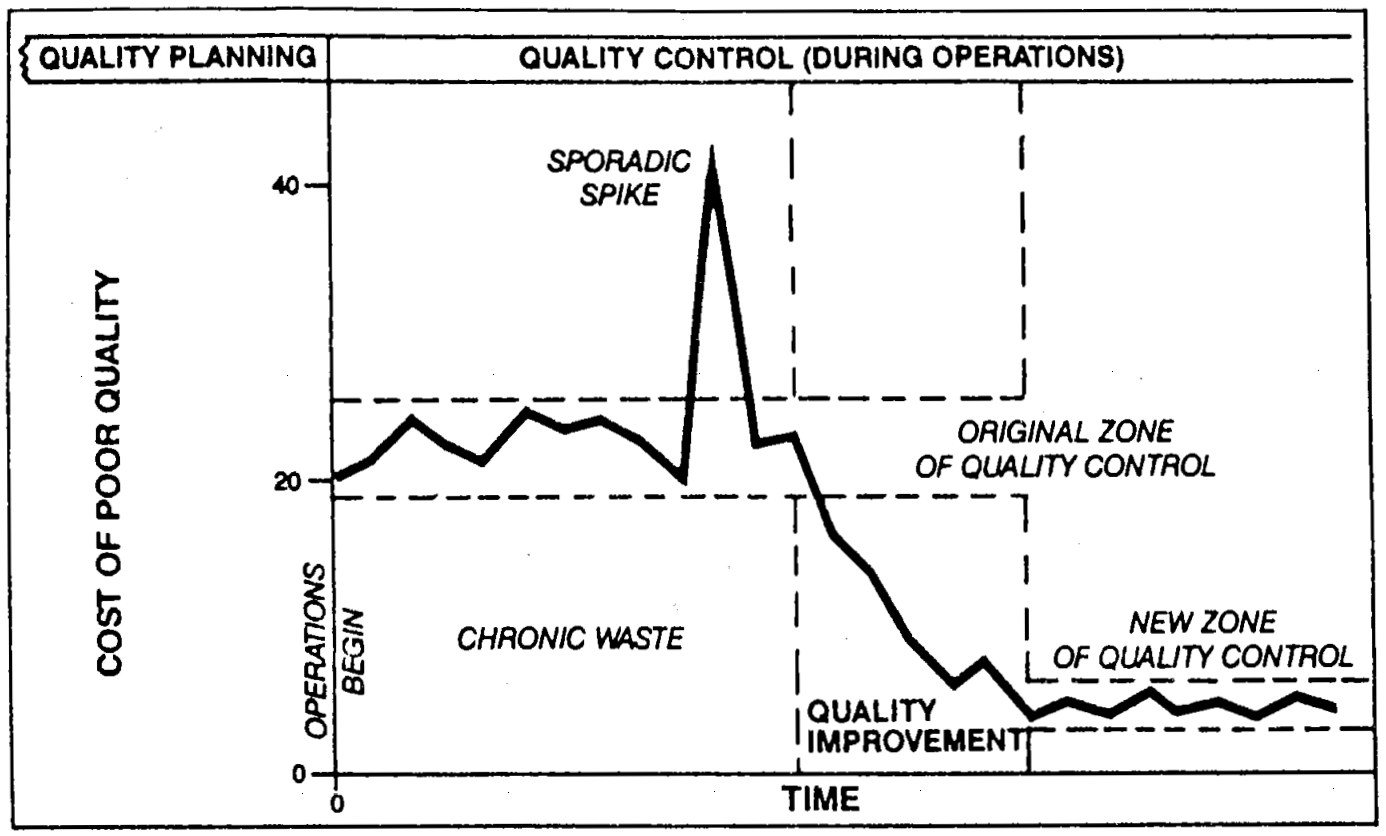
Quality thinking developed with manufacturing systems, and could be considered both order qualifier and order winner. APICS Operations Management Body of Knowledge Framework defines order qualifiers as "screening criteria that must be fulfilled before a firm’s products or services can even be considered as possible candidates for purchase", and order winners as "unique characteristics or combinations of characteristics that result in a competitive advantage and obtaining (winning) an order from the customer." Both terms originated from Oxford professor Terry Hill. Palgrave Macmillan has updated and re-issued his old books on Operations Management.
An abridged history of Quality
Going back to our main topic, quality hasn't always been considered as order qualifier or order winner. During times dominated by philosophy of mass manufacturing, quality was defined from technical aspect, rarely considering the opinion of the end customer and little was done to improve the quality of the system. In such environment quality came at a high price. Works of William Edwards Deming, Philip Bayard Crosby, Joseph Moses Juran and Kaoru Ishikawa shaped modern quality movement.
Table 1 provides a timeline of how quality thinking developed throughout the history as described by Graeme (2011). It should be noted that in this case time period does not represent the first appearance of the theory or approach, instead it represents which theories and approaches were dominant in respective era.
Table 1: Development of quality thinking
Era | Title | Description |
---|---|---|
Pre-1900s | Craftsmanship era | Skilled workers, peer-assessment |
1900s–1950s | Standardisation, Mass Production, Quality Control | Industrialisation, scientific management, unskilled labour, 100% inspection |
1930s–1950s | Quality Assurance era | Statistical Process Control, supplier assessment |
1950s-1970s | Total Quality Management era | Deming, Leadership, Systems Thinking, Customer Focus |
1970s–1990s | Standards and Awards | ISO 9000, Baldrige Award, European Foundation for Quality Management Excellence Award |
1990s–present | Initiative era | Lean, Six Sigma, Business Process Re-Engineering |
Progressive conceptual development is presented in Table 2, based on the phases identified in works by James (1996), Dale et al. (2007), Kaye and Dyason (1995), and Devadasan et al. (2003).
Table 2: From inspection to strategic management
Phase | Title | Abbreviation |
---|---|---|
1. | Quality Inspection | QI |
2. | Quality Control | QC |
3. | Quality Assurance | QA |
4. | Total Quality Management | TQM |
5. | Strategic Quality Management | SQM |
Defining Quality
Before moving to Quality Management, let's consider the following definitions of quality:
The totality of features and characteristics that bear on the ability of a product or service to satisfy a given need. - BS 4778-2:1991
Fitness for purpose. - Juran and Godfrey (1999)
Conformance to requirements. - Crosby (1980)
Satisfaction of the customer. - Ishikawa (1985)
The total composite product and service characteristics of marketing, engineering, manufacture, and maintenance through which the product and service will meet the expectations of the customer. - Feigenbaum (1961)
Quality conformance means consistently delivering services and products in line with their design specifications, which, in turn, need to reflect customer needs. - Hill and Hill (2011)
Quality is a dynamic state associated with products, services, people, processes, and environments that meets or exceeds expectations and helps produce superior value. - Goetsch and Davis (2014)
According to Arnold et al. (2012), the following definition of the quality contains the most commonly accepted ideas in business:
Quality means user satisfaction: that goods or services satisfy the needs and expectations of the user. - Arnold et al. (2012)
From the presented definitions we can delayer quality into several core ideas:
- customers define quality,
- quality should add value to the product or service,
- the product or service should meet or exceed the expectations of customer,
- customer may have unspoken expectations, and
- quality is an organizational effort.
Increased emphasis on quality soon revealed how inadequate traditional systems were for handling quality related issues. Quality Management was devised as an approach to ensure quality of products and services. Differences between the traditional approach to the quality and managing for quality is presented in Table 3.
Table 3: Traditional approach to quality versus managing for quality
Traditional approach to the quality | Quality Management |
---|---|
Emphasis on management | Emphasis on leadership |
Short term focus | Long term focus |
Conformance to internal standards, lack of customer focus | Conformance to customers standards, aims at exceeding the expectations of the customer |
Quality is achieved at high cost | Cost of quality is assessed |
Mechanistic organisation, functional departments, barriers between departments | Focus on system thinking |
Managers think, workers do | Empowering the workers |
Managing for Quality
Since quality is a complex concept, it should be addressed by joint effort of all departments within the company. Dr. Joseph Juran was a big proponent of actively managing for quality, instead of trying to inspect it into the product. One of his notable contributions to Quality Management field was his Quality Trilogy (Figure 1). Inspired by financial processes of (1) budgeting, (2) cost control, expense control, and (3) cost reduction, profit improvement, he created (1) quality planning, (2) quality control, and (3) quality improvement. In other words, modern Quality Management consists of:
- Quality Planning
- Quality Assurance
- Quality Control
- Quality Improvement
Core principles of Quality Management are (Graeme, 2011; Goetsch and Davis, 2014):
- Customer focus
- Strategic focus
- Leadership focus
- Process focus
- People focus
- Scientific focus
- Continuous improvement
- Systems thinking
Some of the tangible and intangible benefits of Quality Management are:
- reduction of costs associated with non-quality (Juran and Godfrey, 1999; Feigenbaum, 1961),
- reduction of waste (Ohno, 1988),
- increased customer satisfaction (Ahire and Dreyfus, 2000; York and Miree, 2004),
- increased workforce satisfaction and motivation (Deming, 1990), and
- improved environmental impact (Tarí and Molina-Azorín, 2010; Pereira-Moliner et al., 2012).
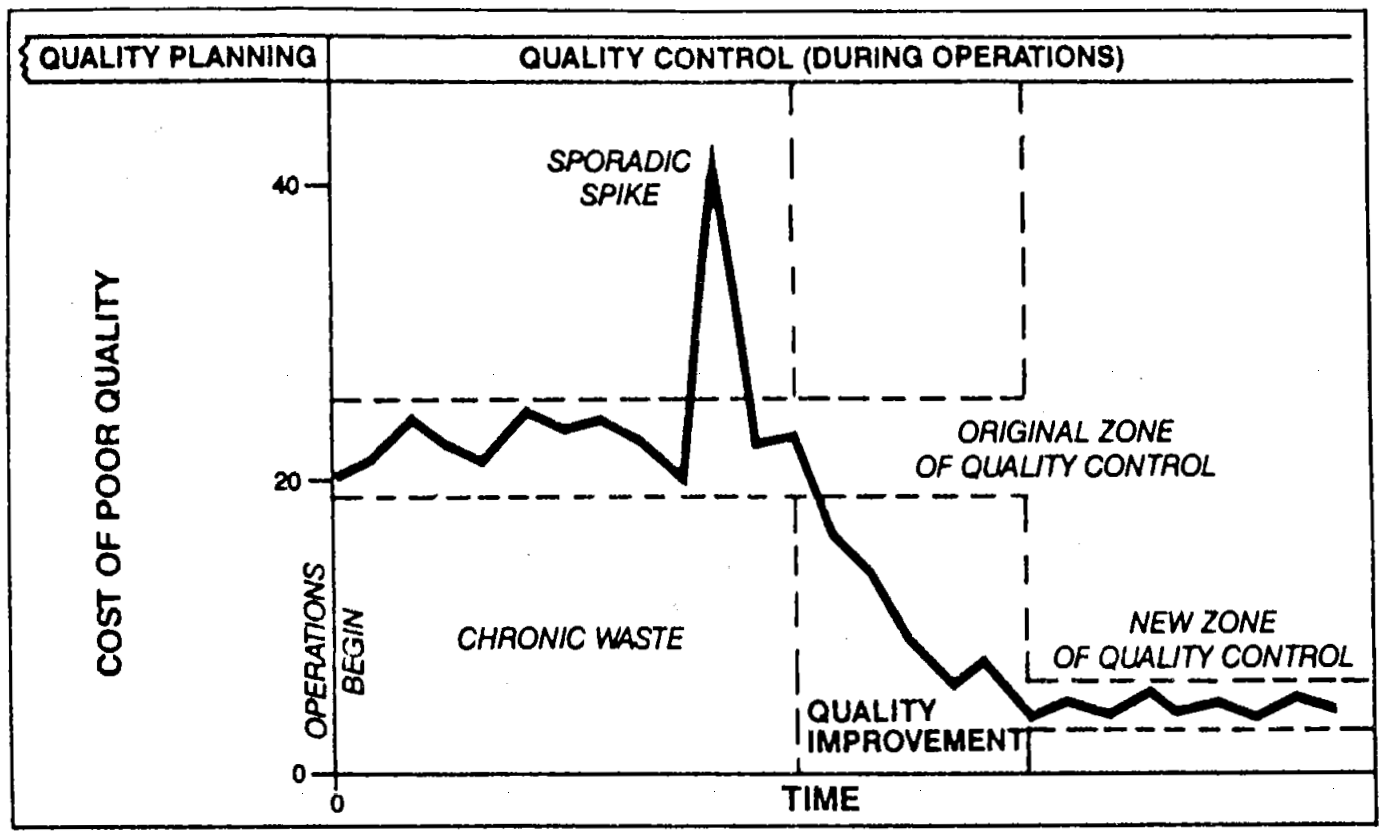
Concluding Remarks
This is the first post in my "Quality Management" series, and as such it was appropriate to start with concise historical overview, from quality inspection to strategic quality management. After that we took a look at various definitions of quality and used them to delayer quality into several core ideas. Finally, I concisely described core elements of Quality Management, as well as its benefits.
In following posts I will write more about William Edwards Deming, Philip Bayard Crosby, Joseph Moses Juran and Kaoru Ishikawa, and their contributions to the Quality Management field. After presenting aforementioned quality philosophers I will write more about various Quality Management Systems and Quality Management Frameworks. I will wrap up my Quality Management series with a post on Continuous Improvement.
References
Ahire, S.L. and Dreyfus, P., 2000. The impact of design management and process management on quality: an empirical investigation. Journal of operations management, 18(5), pp.549-575.
Arnold, J.R.T., Chapman, S.N. and Clive, L.M., 2012. Introduction to Materials Management. Prentice Hall.
Crosby, P.B., 1980. Quality is free: The art of making Quality certain. Signet.
Dale, B.G., Van Der Wiele, T. and Van Iwaarden, J., 2007. Managing Quality. John Wiley & Sons.
Deming, W.E., 1990. The new economics: For industry, government, education. MIT press.
Devadasan, S.R., Muthu, S., Samson, R.N. and Sankaran, R.A., 2003. Design of total Failure Mode and Effects Analysis programme. International Journal of Quality & Reliability Management, 20(5), pp.551-568.
Feigenbaum, A. V., 1961. Total Quality Control. McGraw-Hill.
Goetsch, D.L. and Davis, S.B., 2014. Quality Management for Organizational Excellence. Pearson.
Graeme, K., 2011. Quality Management. Ventus Publishing.
Hill, A. and Hill, T., 2011. Essential Operations Management. Palgrave Macmillan.
Ishikawa, K., 1985. What is Total Quality Control? The Japanese Way. Prentice Hall.
James, P.T., 1996. Total Quality Management: An introductory text. Prentice Hall.
Juran, J.M., 1986. A universal approach to managing for quality. Quality Progress, 19(8), pp.19-24.
Juran, J.M. and Godfrey, A.B., 1999. Juran's Quality Handbook. 5th edition. McGraw-Hill.
Kaye, M.M. and Dyason, M.D., 1995. The fifth era. The TQM Magazine, 7(1), pp.33-37.
Ohno, T., 1988. Toyota Production System: Beyond large-scale production. Productivity Press.
Pereira-Moliner, J., Claver-Cortés, E., Molina-Azorín, J.F. and Tarí, J.J., 2012. Quality Management, Environmental Management and firm performance: Direct and mediating effects in the hotel industry. Journal of Cleaner Production, 37, pp.82-92.
Tarí, J. J. and Molina-Azorín, J.F., 2010. Integration of Quality Management and Environmental Management Systems: Similarities and the role of the EFQM model. The TQM Journal, 22(6), pp.687-701.
York, K.M. and Miree, C.E., 2004. Causation or covariation: An empirical re-examination of the link between TQM and financial performance. Journal of Operations Management, 22(3), pp.291-311.
This article is a part of Quality Management series:
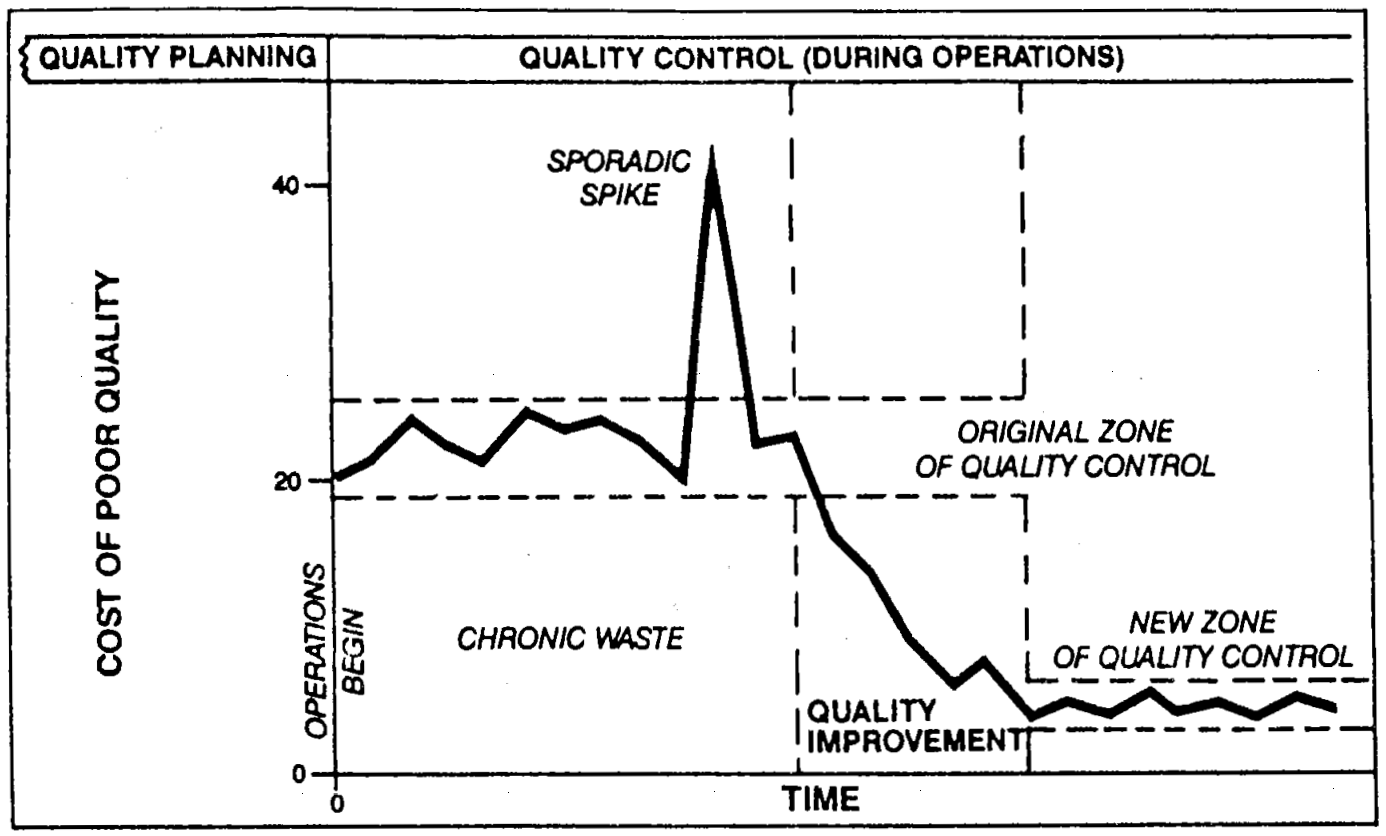
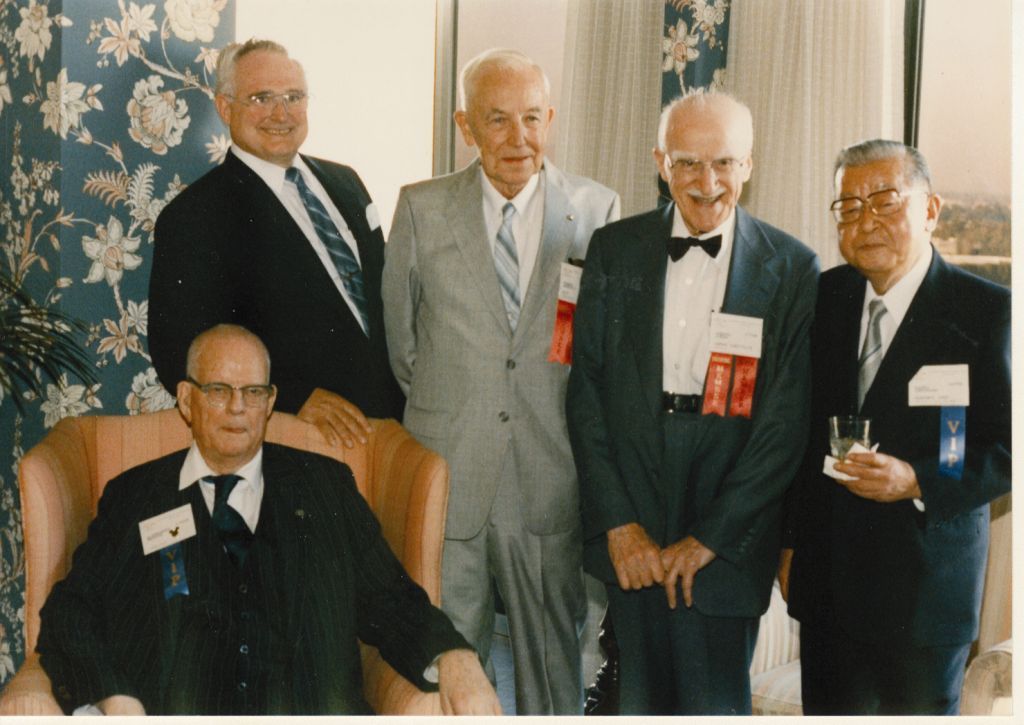
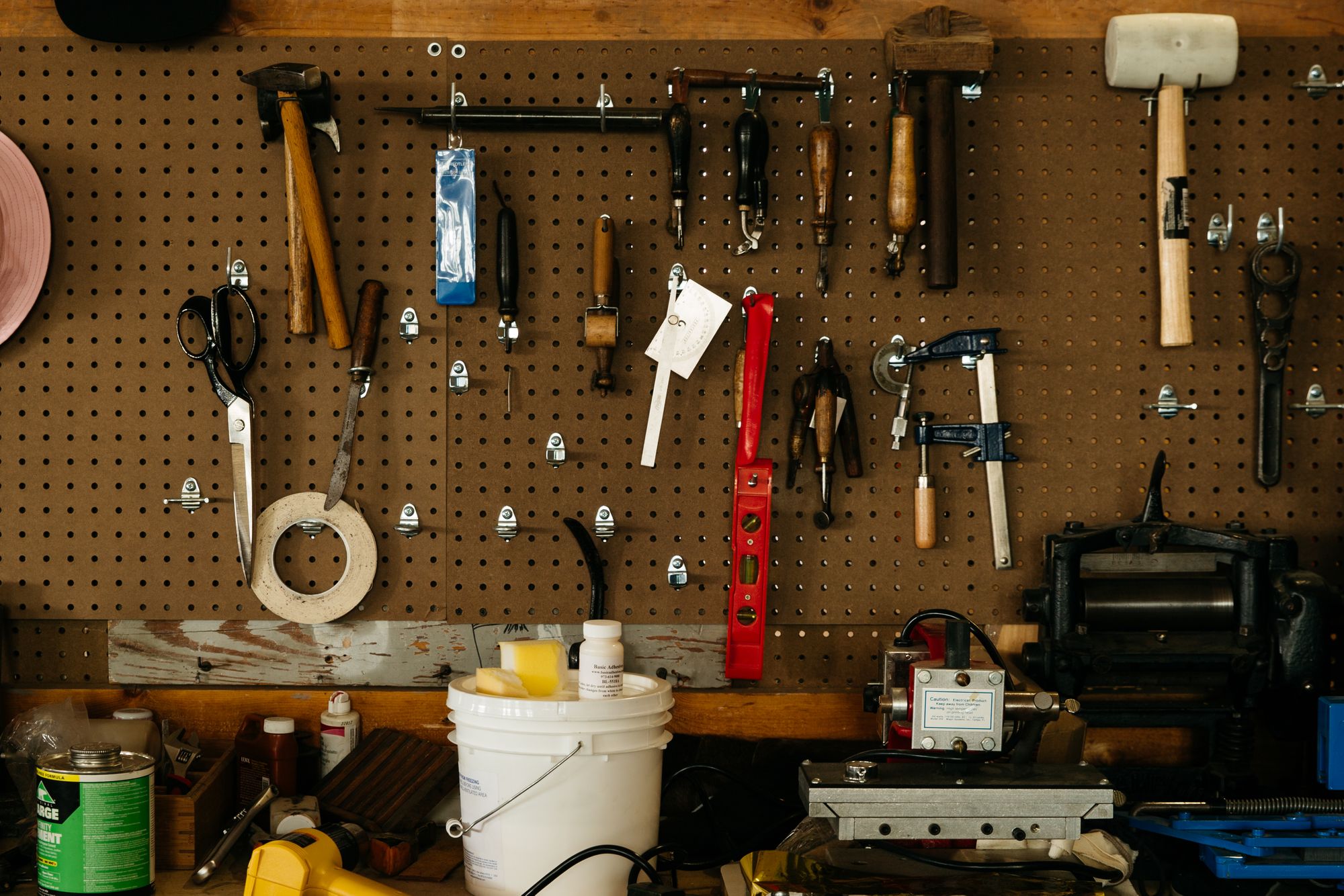
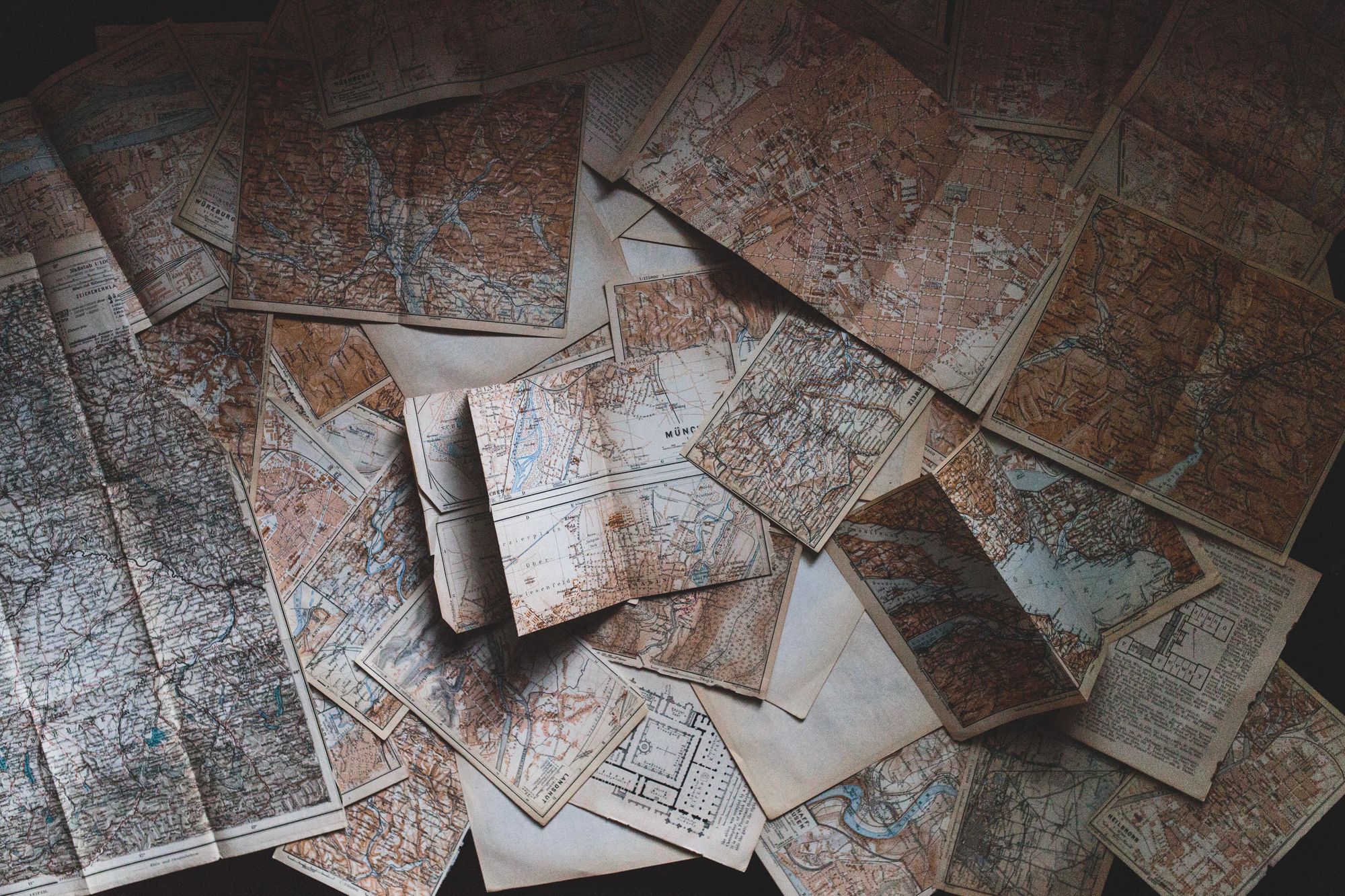
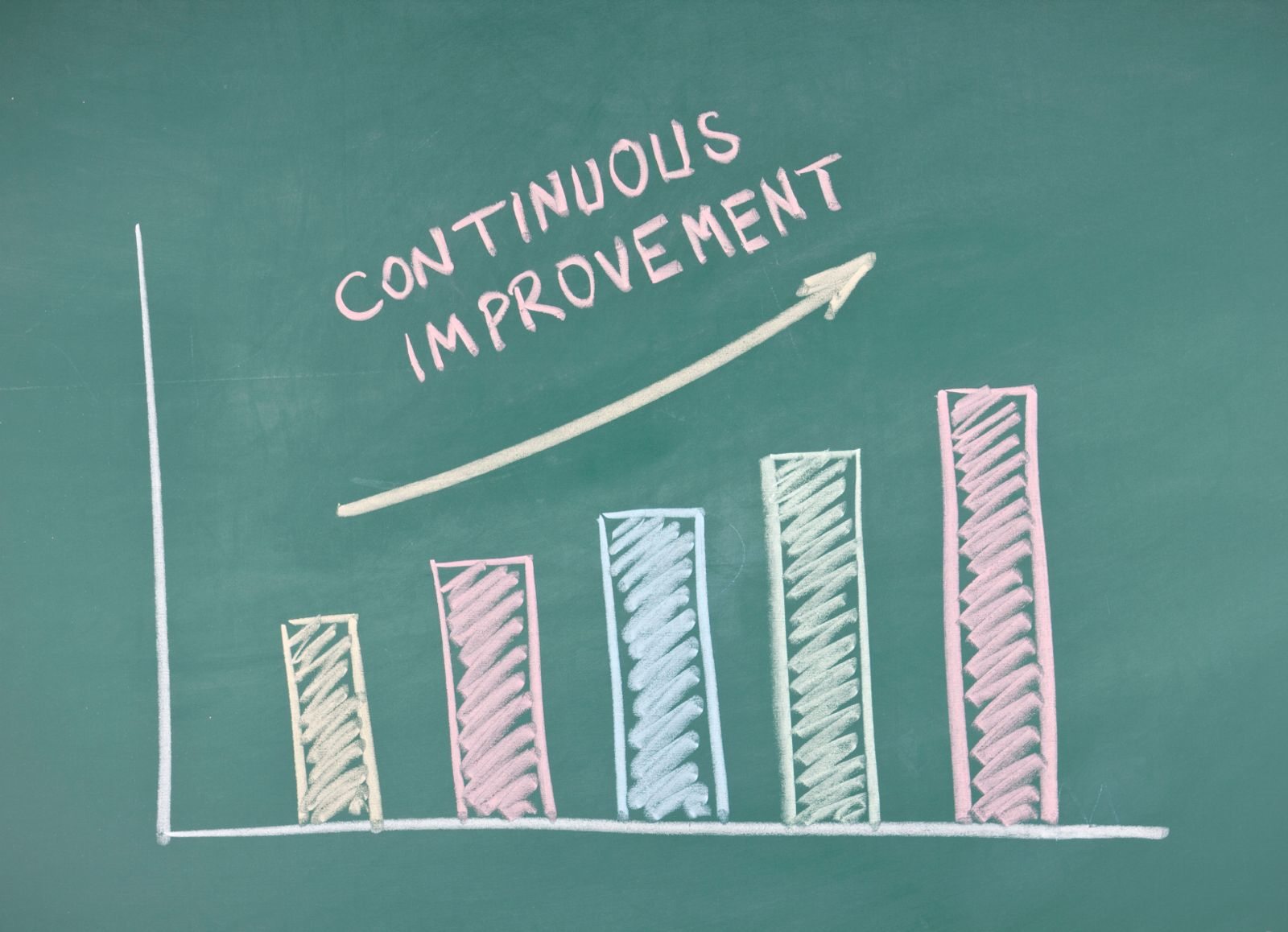
Bruno Unfiltered
Subscribe to get the latest posts delivered right to your inbox. No spam. Only Bruno.