Quality Management Frameworks
Organisations can use quality management frameworks to benchmark the quality performance on their journey to excellence.
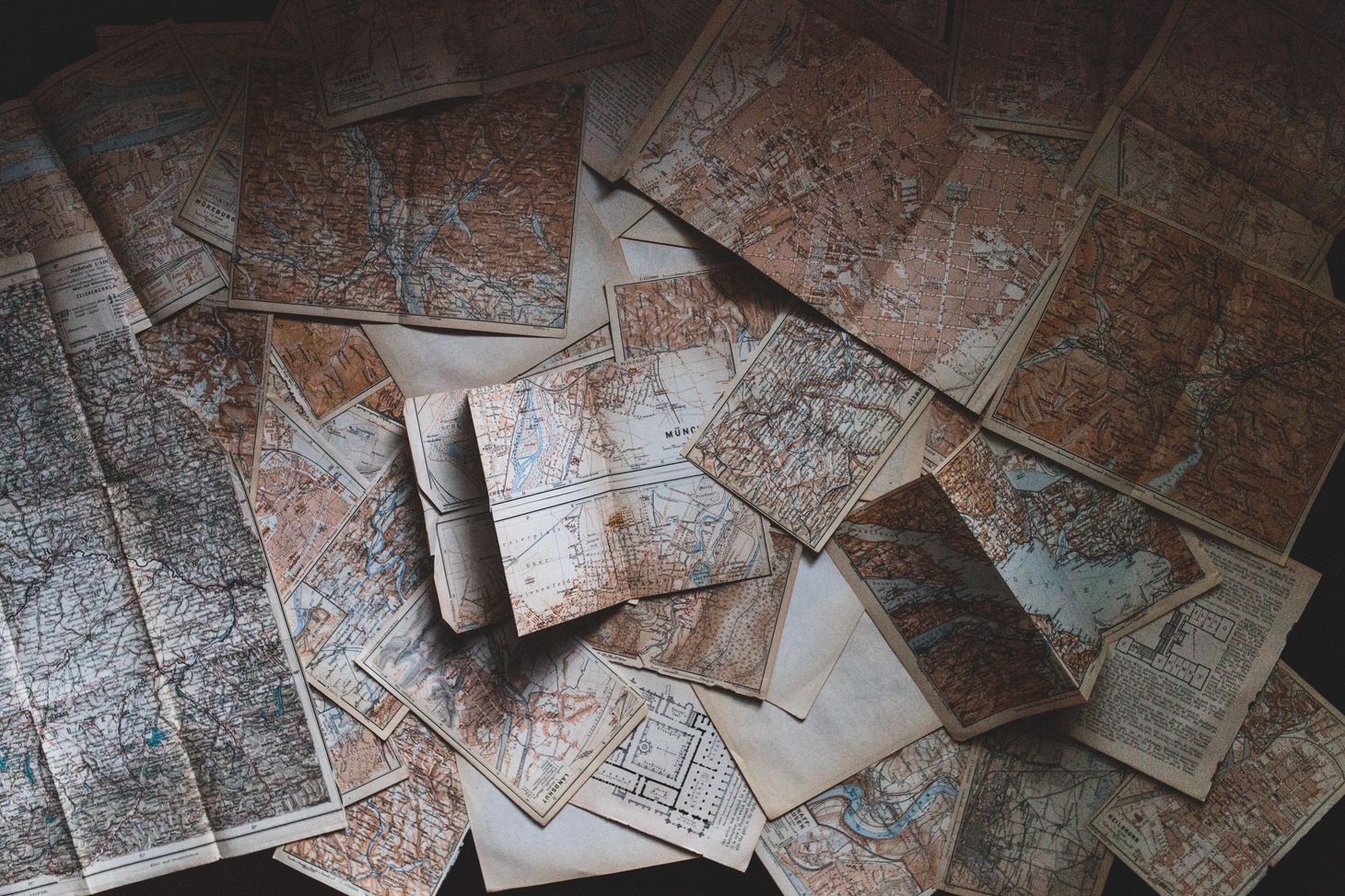
Besides previously discussed Quality Management Systems (QMS), there are also Quality Management Frameworks (QMF) which aim to provide guidance. Companies can use these frameworks to benchmark the performance of their QMS, and can use the guidance of QMF to strive for excellence. In this section I present four most recognized QMFs according to Hill and Hill (2011), and Graeme (2011): ISO 9000 family of standards, The Deming Prize, The Malcolm Baldrige National Quality Award and The European Foundation for Quality Management Excellence Award. Table 1 below provides overview of the aims of aforementioned QMFs.
Table 1: Overview of aims of Quality Management Frameworks
QMF | Aim |
---|---|
ISO 9000 family of standards | Provide international QM standards |
The Deming Prize | Improve the performance of Japanese businesses |
Baldridge Award | Improve the performance of US businesses |
EFQM Excellence Award | Improve the performance of European businesses |
ISO 9000 family of standards
ISO stands for International Organization for Standardization. ISO 9000 “Quality Management” family of standards is developed and maintained by ISO technical committee ISO/TC 176 “Quality management and quality assurance”, and aims to provide standardized guidelines for design and deployment of QMS. Historical development of the standard is given in Table 2. Table 3 lists standards from ISO/TC 176 and its subcommittees.
Table 2: Historical development of ISO 9000 family of standards
Year | Standard |
---|---|
Post 1945 | NATO AQAP |
1960s | Defence Standards 05-21 et seq |
1972 | BS 4891 Guide to Quality Assurance |
1973 | 73/851 DC |
1975 | BS 5179 pt 1-3 |
1979-1981 | BS 5750 pt 1-6 |
1987 | ISO 9000:1987 family |
1994 | ISO 9000:1994 family |
2000 | ISO 9000:2000 family |
2008 | ISO 9000:2008 family |
2015 | ISO 9000:2015 family |
Table 3: Current standards from ISO/TC 176 and its subcommittees
Standard | Title |
---|---|
ISO 9000:2015 | Quality management systems – Fundamentals and vocabulary |
ISO 9001:2015 | Quality management systems – Requirements |
ISO/TS 9002:2016 | Quality management systems – Guidelines for the application of ISO 9001:2015 |
ISO 9004:2009 | Managing for the sustained success of an organization – A quality management approach |
ISO 10001:2007 | Quality management – Customer satisfaction – Guidelines for codes of conduct for organizations |
ISO 10002:2014 | Quality management – Customer satisfaction – Guidelines for complaints handling in organizations |
ISO 10003:2007 | Quality management – Customer satisfaction – Guidelines for dispute resolution external to organizations |
ISO 10004:2012 | Quality management – Customer satisfaction – Guidelines for monitoring and measuring |
ISO 10005:2005 | Quality management systems – Guidelines for quality plans |
ISO 10006:2003 | Quality management systems – Guidelines for quality management in projects |
ISO 10007:2003 | Quality management systems – Guidelines for configuration management |
ISO 10008:2013 | Quality management – Customer satisfaction – Guidelines for business-to-consumer electronic commerce transactions |
ISO 10012:2003 | Measurement management systems – Requirements for measurement processes and measuring equipment |
ISO/TR 10013:2001 | Guidelines for quality management system documentation |
ISO 10014:2006 | Quality management – Guidelines for realizing financial and economic benefits |
ISO 10015:1999 | Quality management – Guidelines for training |
ISO/TR 10017:2003 | Guidance on statistical techniques for ISO 9001:2000 |
ISO 10018:2012 | Quality management – Guidelines on people involvement and competence |
ISO 10019:2005 | Guidelines for the selection of quality management system consultants and use of their services |
ISO/TS 16949:2009 | Quality management systems – Particular requirements for the application of ISO 9001:2008 for automotive production and relevant service part organizations |
ISO/TS 17582:2014 | Quality management systems – Particular requirements for the application of ISO 9001:2008 for electoral organizations at all levels of government |
ISO 18091:2014 | Quality management systems – Guidelines for the application of ISO 9001:2008 in local government |
ISO 19011:2011 | Guidelines for auditing management systems |
ISO 9000 proposes the use of process approach to achieve continual improvement (Figures 1 and 2) as well as seven Quality Management Principles (ISO, 2015):
- Customer focus
- Leadership
- Engagement of people
- Process approach
- Improvement
- Evidence-based decision making
- Relationship management
In addition, ISO/TC 176 (2009) proposes seven steps for successful implementation of QMS:
- Engagement of top management
- Identify key processes and the interactions needed to meet quality objectives
- Implement and manage the QMS and its processes (using process management techniques)
- Build your ISO 9001-based QMS
- Implement the system, train company staff and verify effective operation of your processes
- Manage your QMS
- If necessary, seek third party certification/registration of the QMS or alternatively, issue a self-declaration of conformity
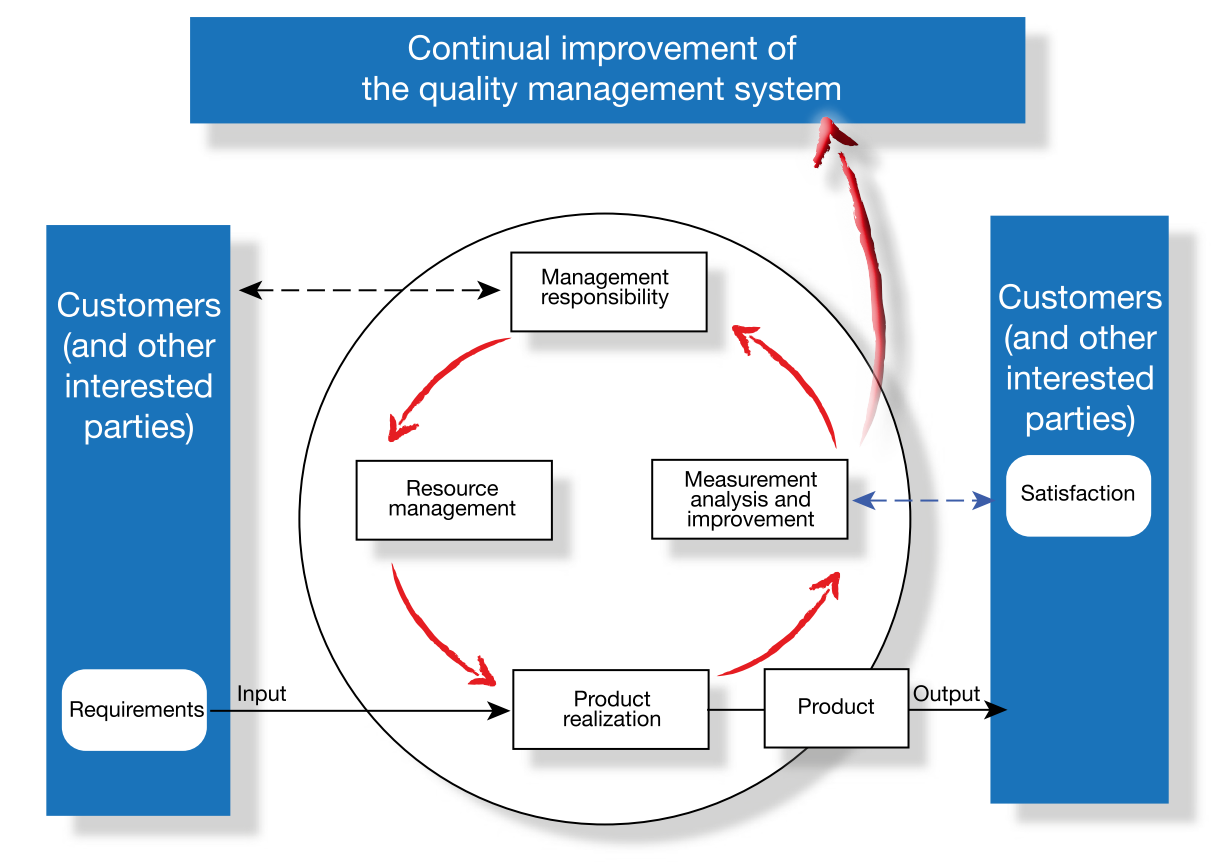
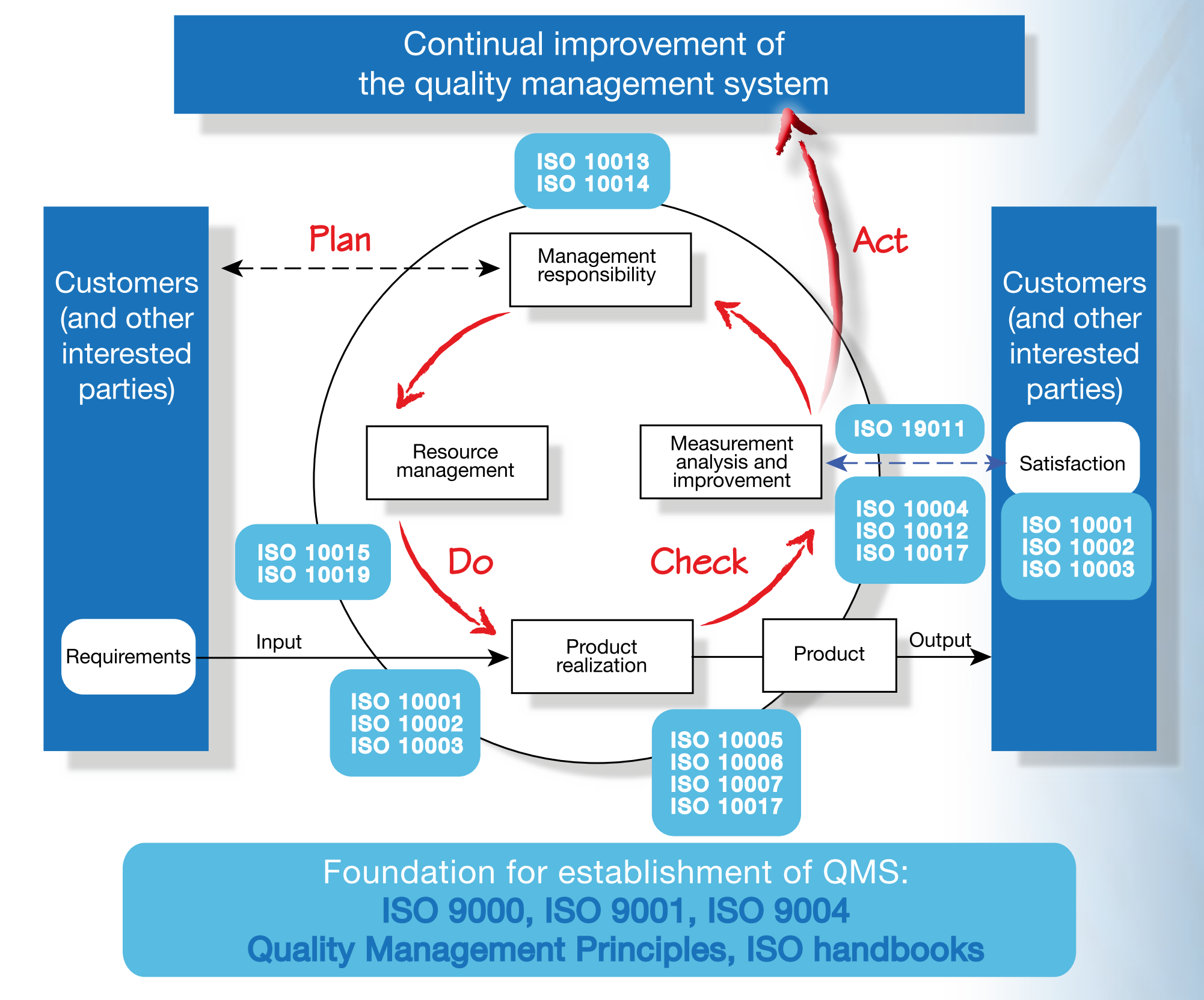
According to ISO (2010) and ISO (2015), 1109905 certificates for ISO 9001 had been issued in 2010, and 1033936 in 2015. Certification is not performed by ISO. Yet, the usefulness of ISO 9000 family of standards is often questioned and criticised. Proponents argue that organizations with ISO 9000 certificate achieve better financial results (Heras et al., 2002; Corbett et al., 2005; Sharma, 2005), operational performance (Naveh and Marcus, 2007; Lo et al., 2009), stock market performance (Rajan and Tamimi, 2003), market performance (Buttle, 1997) and a number of internal benefits (Alcorn, 1995). Based on the aforementioned works, benefits of implementing ISO 9000 could be summed to the following:
- standards as a communication tool, both internal and external,
- increased profit margins,
- optimisation of operations and processes,
- enhanced image and marketing,
- empowered and motivated workforce, and
- better customer satisfaction.
It should be noted that direct causation between listed benefits and ISO 9001:2008 certification hasn’t been proven (Corbett et al., 2005). Opponents argue that ISO 9000 family focuses on procedures and control instead of improvement and understanding (Seddon, 2000), requires large amount of paperwork which results in increased administrative workload (Seddon, 2000), and does not cover the passion required to deliver the excellence (Peters and Waterman, 2006). Further criticism is that ISO 9001:2008 certificate does not guarantee good product or service and that benefits of applying the quality approach are unrelated to the certification (Dalgleish, 2005). Heras et al. (2011) find that “no significant relationship was definitively identified between the use of quality tools and an increase in a company’s performance when it based its quality system on the ISO 9001:2000 standard”. Furthermore, some requirements directly contradict the teachings of quality gurus.
Most recent issue of the standard ISO 9001 (2015) has stirred a lot of controversy and confusion, especially with so-called Risk Based Thinking. Christopher Paris of Oxebridge has written a number of useful articles:
- Exploding the Myths of ISO 9001:2015
- ISO 9001:2015 Won’t Require a Quality Manual — Here’s What to Replace it With
- Practical Implementation of “Risk Based Thinking” – Part 1
- Practical Implementation of “Risk Based Thinking” – Part 2
The Deming Prize
The Deming Prize was created by the Union of Japanese Scientists and Engineers (JUSE) as appreciation to contribution of Edward Deming. Its aim is to promote excellence in Japanese businesses. The categories of the Deming Prize (Table 4) are the Deming Prize for Individuals, the Deming Prize, and the Deming Grand Prize. Applicants are examined on basis of the following viewpoints:
- Reflecting its management principles, type of industry, business scope, and business environment, the applicant has established challenging and customer-oriented business objectives and strategies under its clear management leadership.
- TQM has been implemented properly to achieve business objectives and strategies as mentioned Item 1 above.
- As an outcome of Item 2, the outstanding results have been obtained for business objectives and strategies as stated in Item 1.
Table 4: Categories of the Deming Prize
Category | Description |
---|---|
The Deming Prize for Individuals | Given to those who have made outstanding contributions to the study of TQM or those who have made outstanding contributions in the dissemination of TQM. |
The Deming Prize | Given to organizations that have implemented TQM suitable for their management philosophy, scope/type/scale of business, and management environment (Annual award). |
The Deming Grand Prize | Given to organizations that had maintained and further enhanced the level of TQM for more than three years after the winning of the Deming Prize or the Deming Prize (Annual award). |
JUSE lists the following five effects of the Deming Prize:
- New product development and launch will be promoted
- New technology can be obtained
- Sales target will be achieved continuously
- Become capable of following a policy and fulfilling an objective
- Organization’s functionality will be enhanced
Deming Prize is an efficient way of benchmarking and steering your TQM system. JUSE publishes summaries of prize winners, allowing you to benchmark yourself against the pioneers of quality:
- 2013 Deming Grand Prize and Deming Prize Winners Presentation Summary
- 2014 Deming Prize Winners Presentation Summary
- 2015 Deming Prize Winners Presentation Summary
- 2016 Deming Prize Winners Presentation Summary
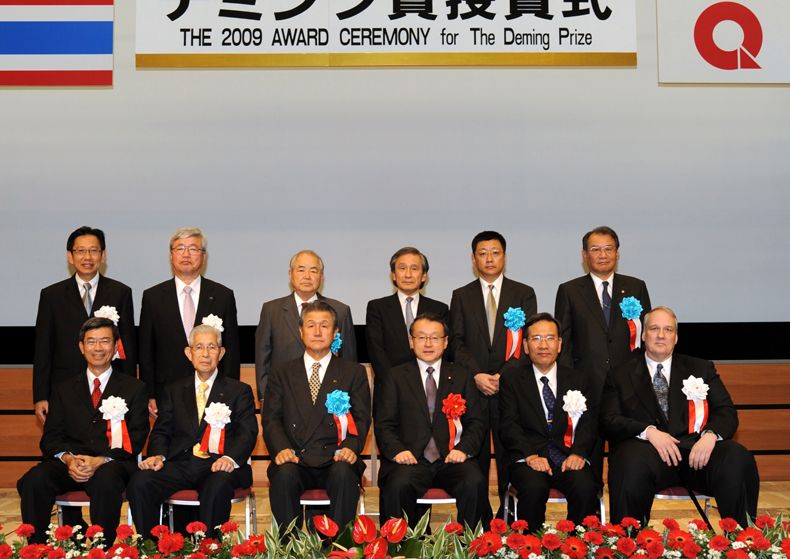
The Malcolm Baldrige National Quality Award
The Malcolm Baldrige National Quality Award (MBNQA) was created by the United States congress and was named after Malcolm Baldrige. It is administered by the National Institute of Standards and Technology (NIST), and aims to improve the performance of U.S. businesses by identifying and recognizing role-model businesses, establishing criteria for evaluating improvement efforts and disseminating and sharing best practices. The award focuses on performance in five key areas: product and process outcomes, customer outcomes, workforce outcomes, leadership and governance outcomes, and financial and market outcomes.
In addition to the MBNQA, NIST also promotes Baldrige Excellence Framework, a “systems approach to improving your organization’s approach” for Business / Nonprofit, Education, and Health Care sectors. Baldrige Criteria for Performance Excellence are depicted in Figure 4, while the role of core value and concepts is depicted in Figure 5. You can read more about aforementioned criteria in available commentary.
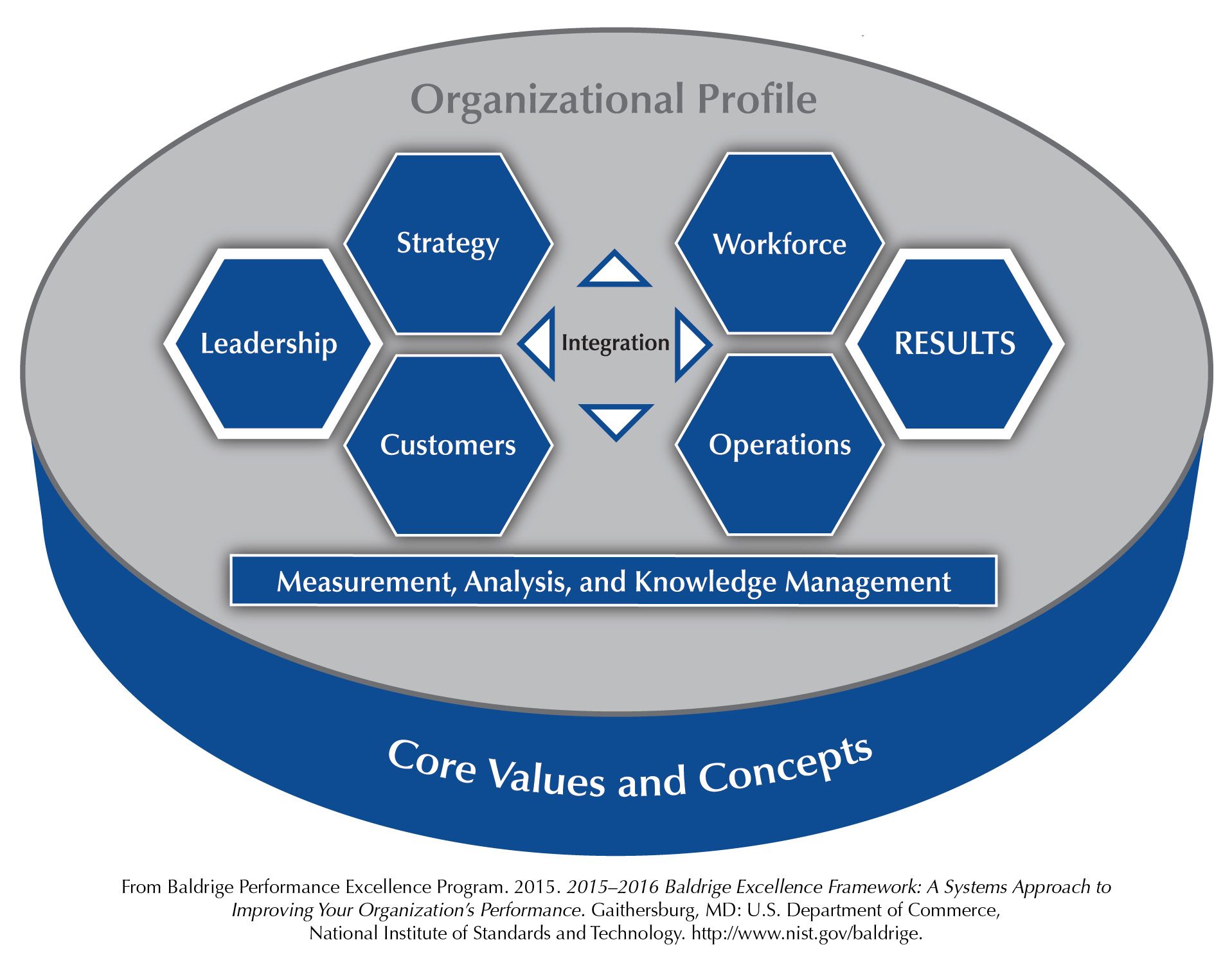
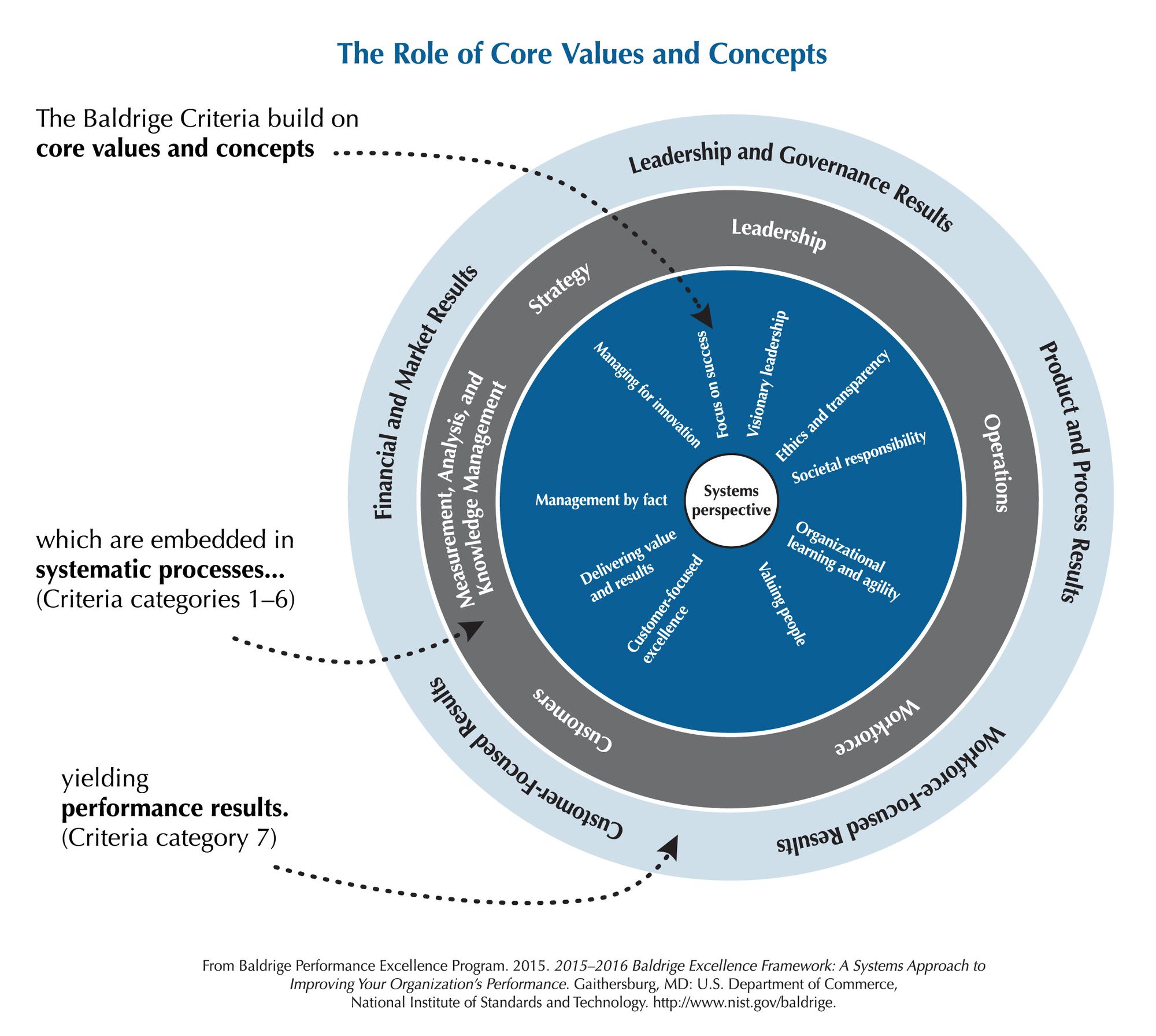
The European Foundation for Quality Management Excellence Award
European Foundation for Quality Management (EFQM) was founded in 1988 with aim to promote TQM approach and improve performance in European businesses. European Quality Award was launched in 1991, and was later renamed to EFQM Excellence Award. Companies are assessed on the basis of nine aspects: leadership; people; strategy; partnership and resources; processes, products and services; people results; customer results; society results; business results.
The EFQM Excellence Model is proposed as framework for achieving excellence. It is envisioned as non-prescriptive holistic framework and is comprised of three integrated components: The Fundamental Concepts of Excellence (Figure 6), The Criteria (Figure 7) and The RADAR (Figure 8). Concise description of aforementioned components is given in Table 5. Model is reviewed and updated in 3 year cycles.
Improvements in the organizational results are expected after successful adoption of holistic model like EFQM model (Hendricks and Singhal, 1996). Recent studies have shown that in companies which use EFQM model, quality-improvement tools have a high effect on performance (Heras et al., 2011), while also contributing to the development of an integrative strategy formation process (Taboada et al., 2011).
Table 5: Elements of the EFQM Excellence Model
Element | Description |
---|---|
The Fundamental Concepts of Excellence | The Fundamental Concepts of Excellence outline the foundation for achieving sustainable excellence in any organisation. They can be used as the basis to describe the attributes of an excellent organisational culture. They also serve as a common language for top management. |
The Criteria | The EFQM Excellence Model allows people to understand the cause and effect relationships between what their organisation does, the Enablers, and the Results it achieves. |
The RADAR | The RADAR logic is a dynamic assessment framework and powerful management tool that provides a structured approach to questioning the performance of an organisation. |
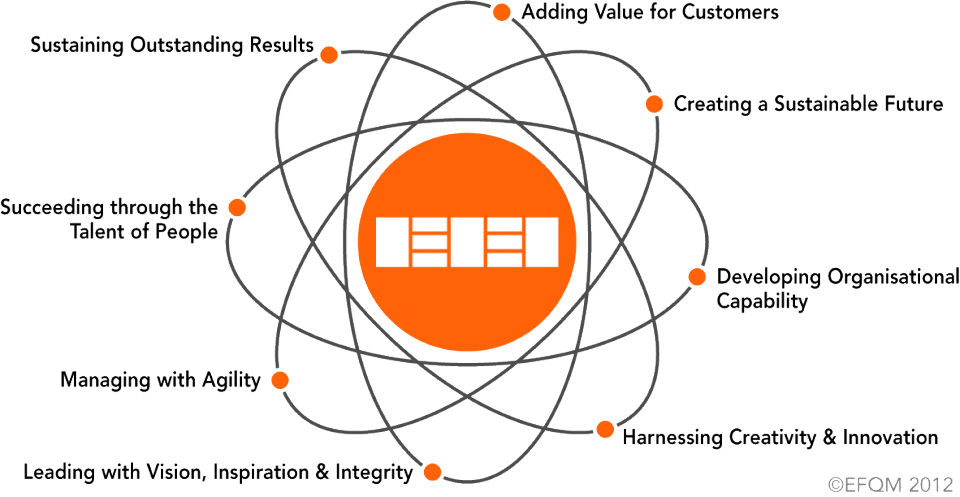
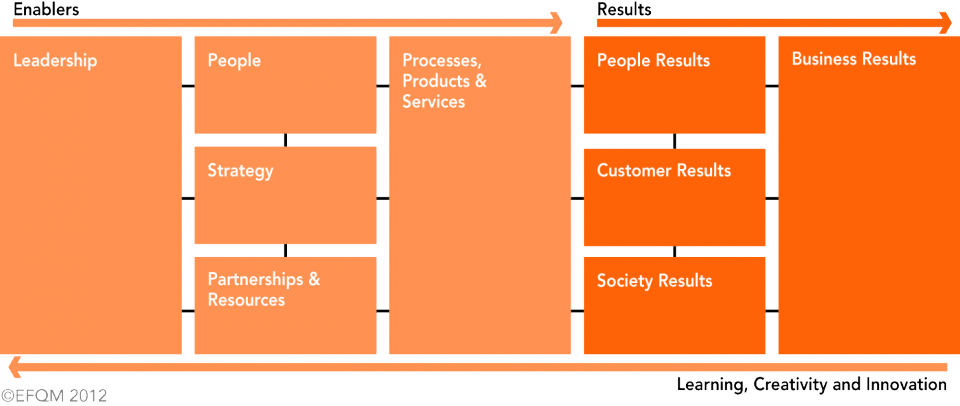
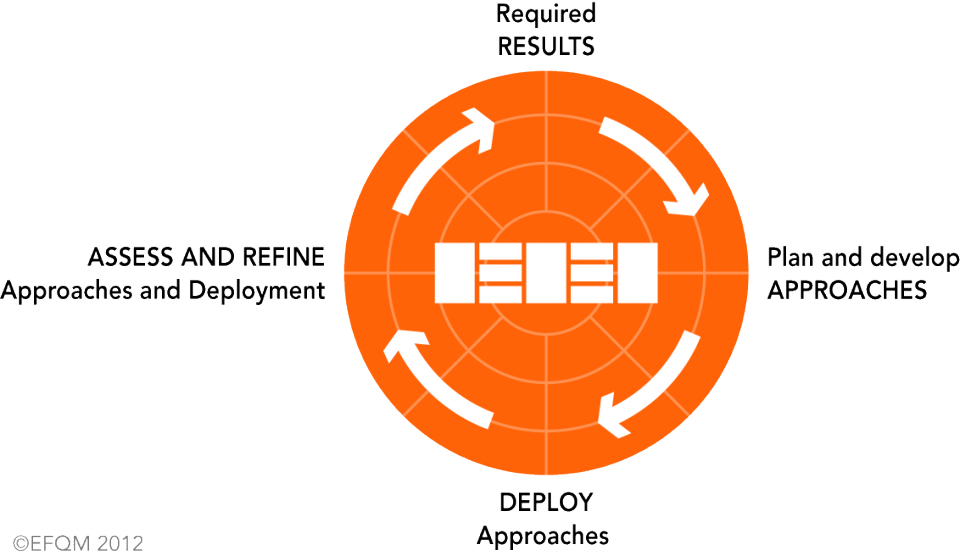
Closing remarks
In previous blog posts I covered what is quality and why is it important to manage it, some of the most important quality philosophers, and presented six different Quality Management Systems. As Aristotle said, excellence is a matter of habit. In this post I presented four well known Quality Management Frameworks. ISO 9001 is the most well known of these four, but has encountered increasing problems in last years, from numerous certificate mills to bad management.
Your QMS should support your efforts to deliver great value to your customers without sacrificing the well-being of your own employees. QMFs, like excellence awards, can be a great way to benchmark yourself against the best in the field. QMSs and QMFs don’t exclude each other, but rather complement each other. In today’s ultra-competitive world it is important to use every advantage you can.
References
Alcorn, J. E. 1995. The Benefits of ISO 9000 Certification, in A Collection of Papers Presented at the 55th Conference on Glass Problems: Ceramic Engineering and Science Proceedings, Volume 16, Issue 2 (ed J. B. Wachtman), John Wiley & Sons, Inc.
Buttle, F., 1997. ISO 9000: marketing motivations and benefits. International journal of quality & reliability management, 14(9), pp.936-947.
Corbett, C.J., Montes-Sancho, M.J. and Kirsch, D.A., 2005. The financial impact of ISO 9000 certification in the United States: An empirical analysis. Management science, 51(7), pp.1046-1059.
Dalgleish, S. 2005. Probing the Limits: ISO 9001 Proves Ineffective. Quality Magazine.
Graeme, K., 2011. Quality Management. Ventus Publishing.
Hendricks, K.B. and Singhal, V.R., 1996. Quality awards and the market value of the firm: An empirical investigation. Management science, 42(3), pp.415-436.
Heras, I., Dick, G.P. and Casadesus, M., 2002. ISO 9000 registration’s impact on sales and profitability: A longitudinal analysis of performance before and after accreditation. International Journal of Quality & Reliability Management, 19(6), pp.774-791.
Heras, I., Marimon, F. and Casadesús, M., 2011. Impact of quality improvement tools on the performance of firms using different quality management systems. Innovar, 21(42), pp.161-174.
Hill, A. and Hill, T., 2011. Essential Operations Management. Palgrave Macmillan.
ISO, 2010. ISO 9001 survey. ISO.
ISO, 2015. Quality Management Principles. ISO.
ISO, 2015. The ISO Survey of Management System Standard Certifications 2015. ISO.
ISO/TC 176, 2009. Selection and use of the ISO 9000 family of standards. ISO.
Lo, C.K., Yeung, A.C. and Cheng, T.E., 2009. Impact of ISO 9000 on time-based performance: an event study. Int J Humanit Soc Sci, 1, pp.35-40.
Naveh, E. and Marcus, A., 2007. Financial performance, ISO 9000 standard and safe driving practices effects on accident rate in the US motor carrier industry. Accident Analysis & Prevention, 39(4), pp.731-742.
Peters, T. and Waterman, R. 2006. In search of excellence : Lessons from America’s best-run companies. HarperBusiness Essentials.
Rajan, M. and Tamimi, N., 2003. Payoff to ISO 9000 registration. The Journal of Investing, 12(1), pp.71-77.
Seddon, J. 2000. The case against ISO 9000. Oak Tree Press.
Sharma, D.S., 2005. The association between ISO 9000 certification and financial performance. The international journal of accounting, 40(2), pp.151-172.
Taboada, L.R., Giner, M.T.C. and Benavent, F.B., 2011. Quality tools and techniques, EFQM experience and strategy formation. Is there any relationship? The particular case of Spanish service firms. Innovar: revista de ciencias administrativas y sociales, 21(42), pp.25-40.
This article is a part of Quality Management series:
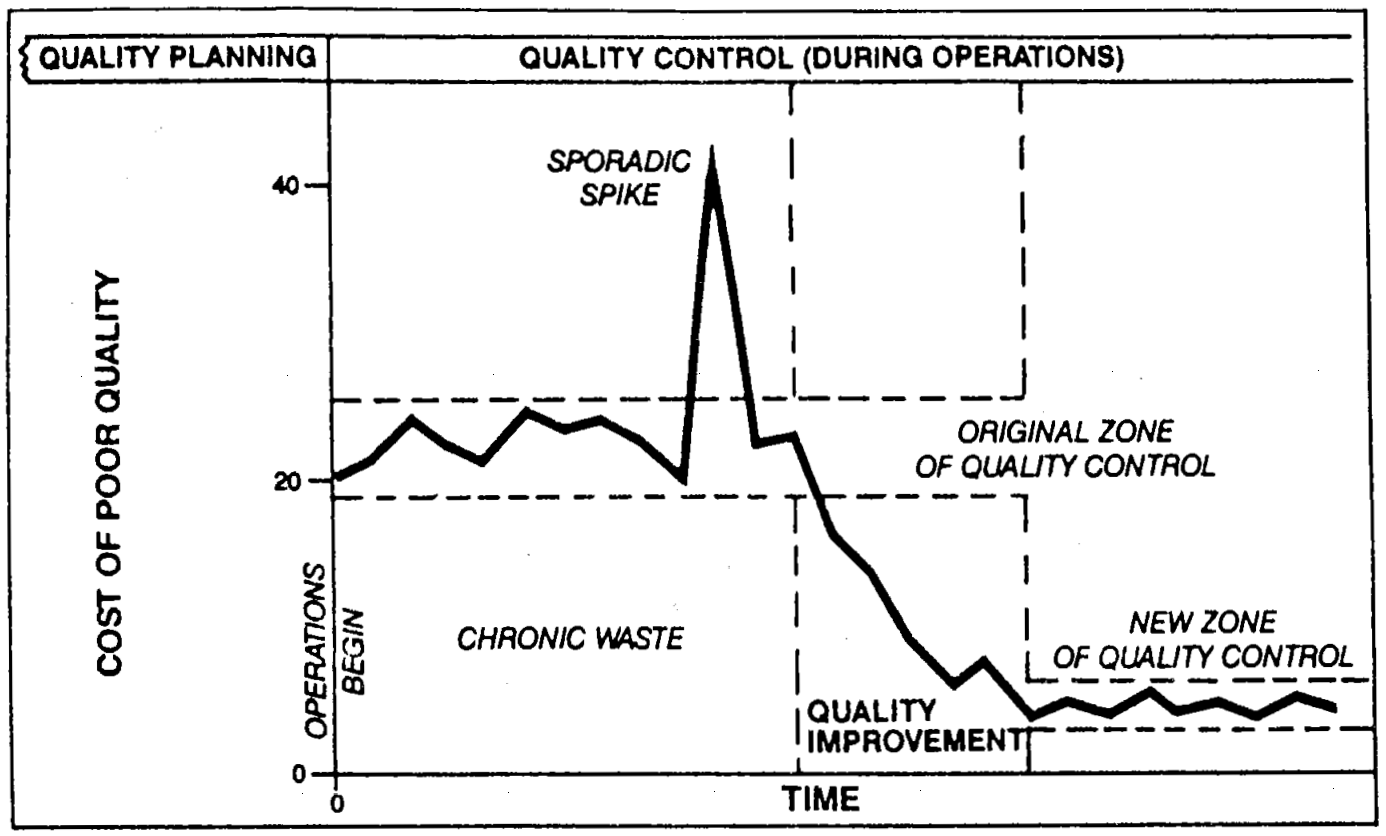
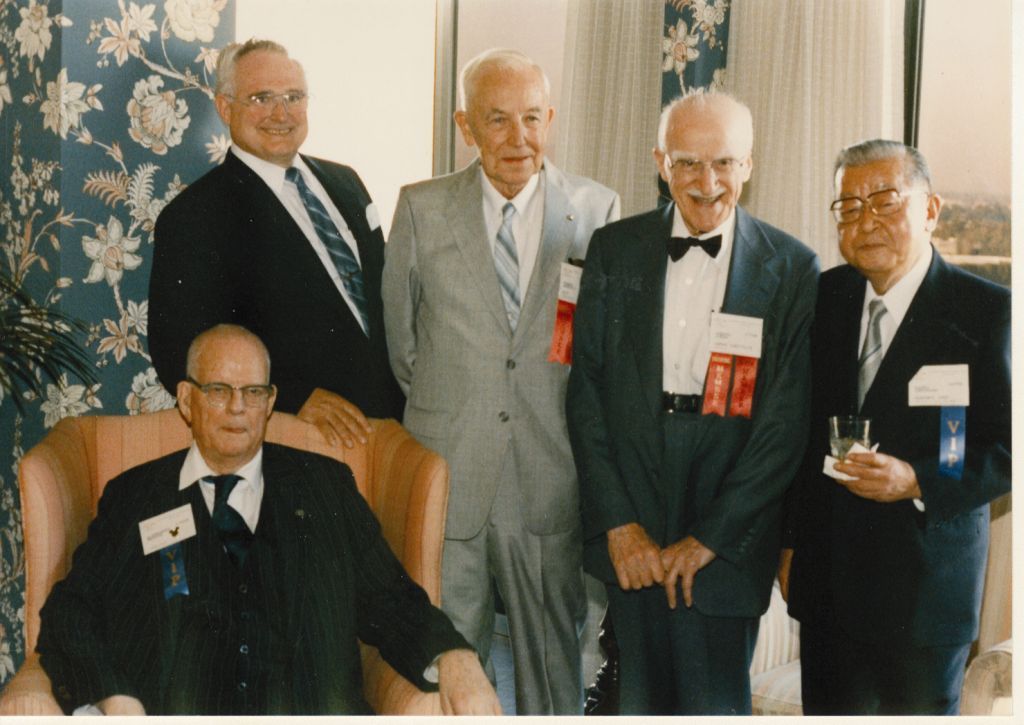
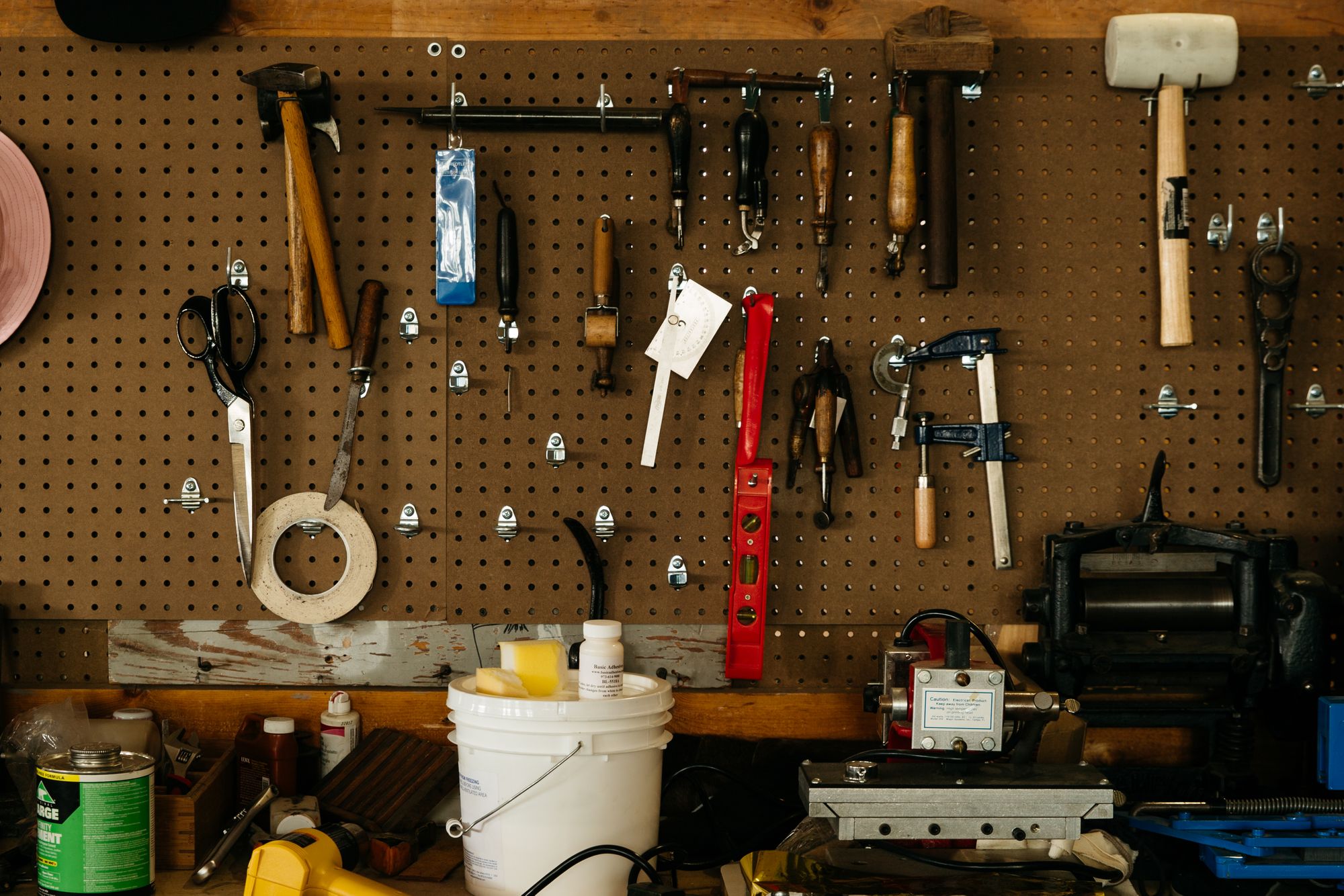
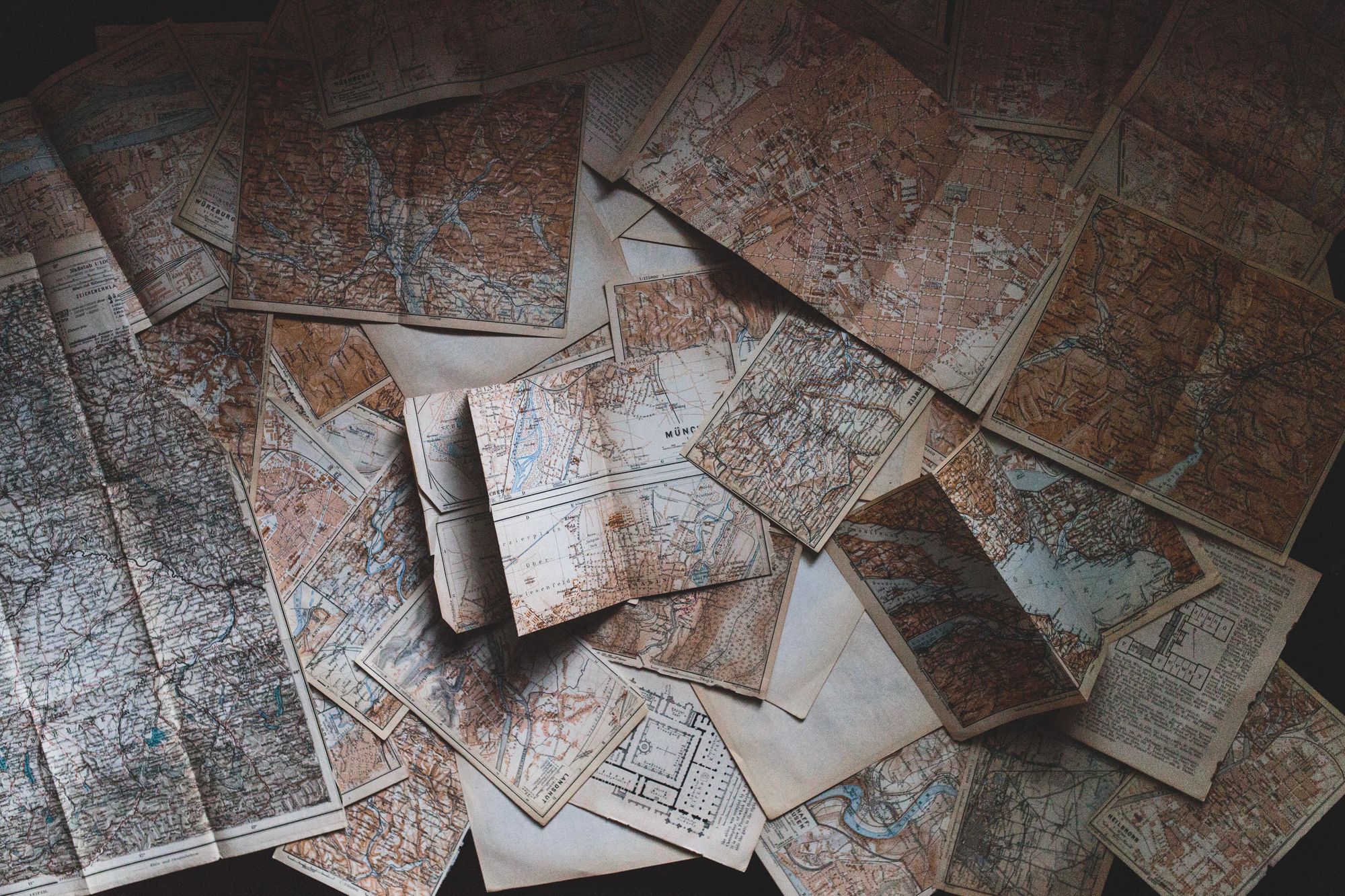
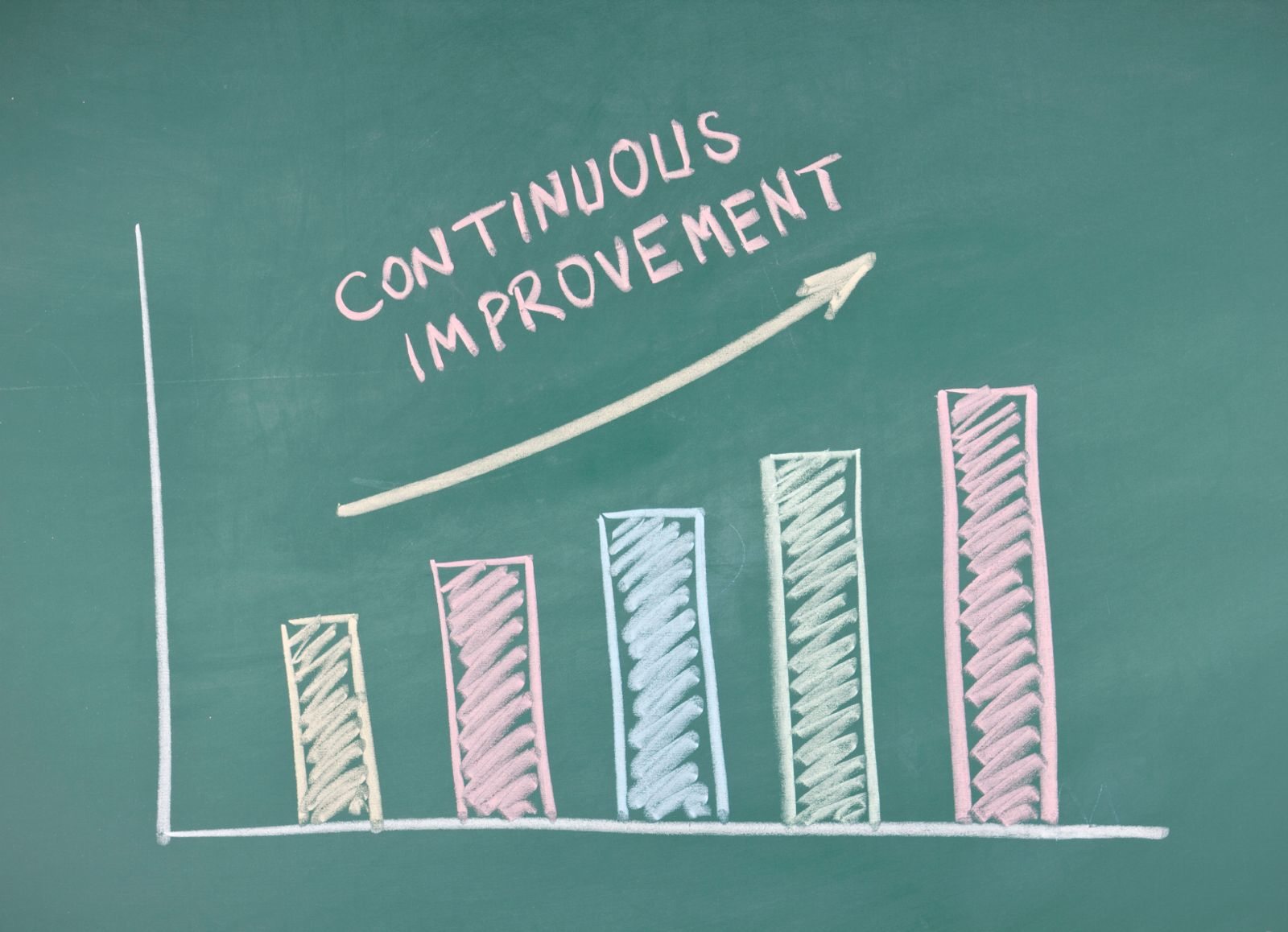
Bruno Unfiltered
Subscribe to get the latest posts delivered right to your inbox. No spam. Only Bruno.