Six Sigma: critique
Supposedly Six Sigma projects have created billions and billions of dollars in savings. Is everything as rosy as consultants claim?
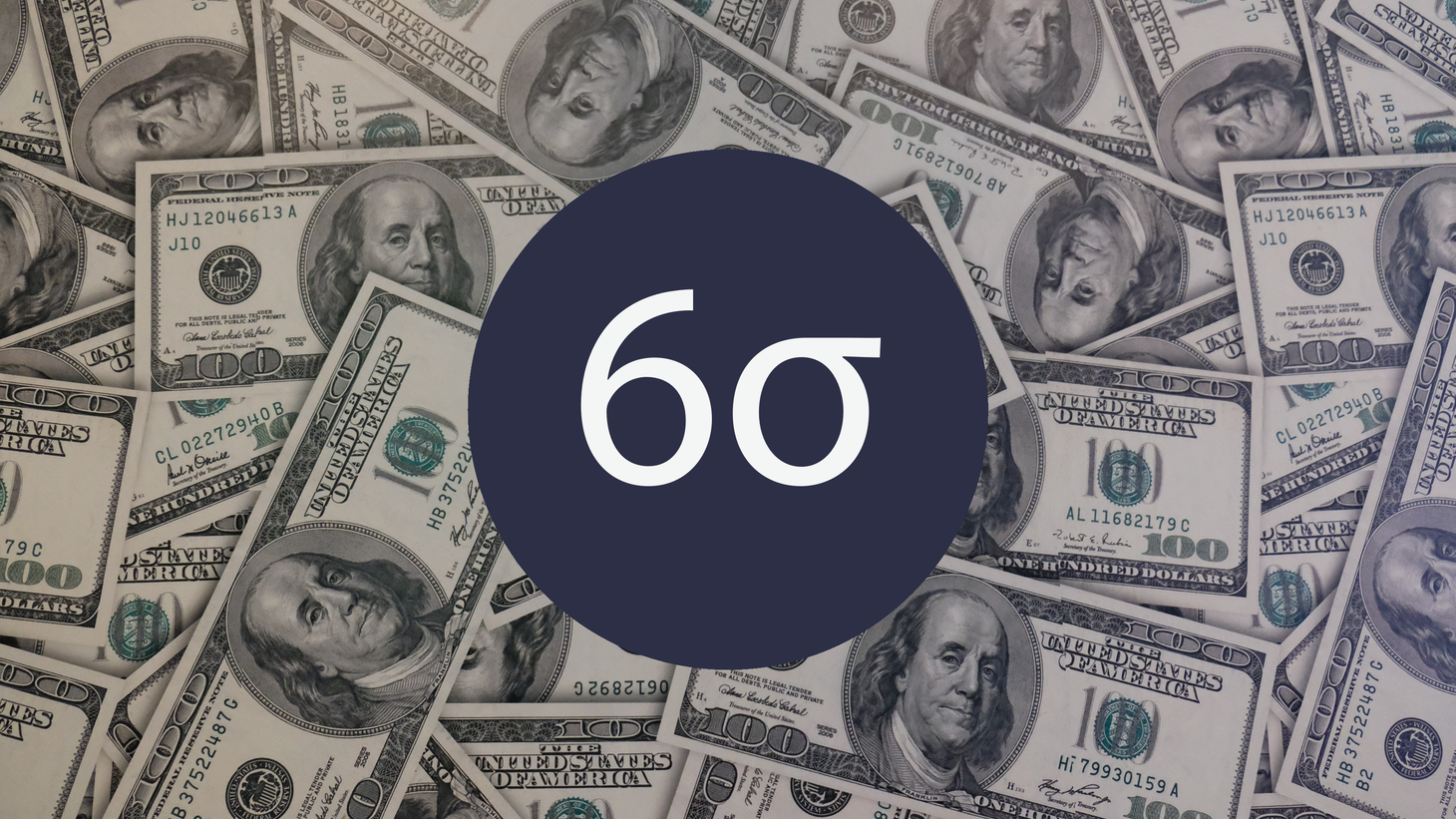
Customer satisfaction (Behara et al., 1995; Douglas & Erwin, 2000; Kuei & Madu, 2003; Ganesh, 2004; Das et al., 2006; Desai, 2006; Rylander & Provost, 2006; Kumar et al., 2007) and financial performance (Kwak & Anbari, 2006; Antony et al., 2005; Freiesleben, 2006) are the most cited benefits of Six Sigma.
Opponents often refer to Six Sigma as another fad (Dalgleish, 2003; Senapati, 2004; Usher, 2008), the fact that it is only appropriate for manufacturing companies (Kumar et al., 2008), that it works only in large organisations (Kumar et al., 2008), that it is same as TQM (Reed, 2000; Seddon, 2003), that it requires massive training (Smith, 2004) and that it is not cost-effective (Senapati, 2004).
Kwak & Anbari (2006) report following benefits and savings from Six Sigma in the manufacturing sector:
Company / project | Metric / measures | Benefit / savings |
---|---|---|
Motorola (1992) | In-process defect levels | 150 times reduction |
Raytheon / aircraft integration systems | Depot maintenance inspection time | Reduced 88% as measured in days |
GE / Railcar leasing business | Turnaround time at repair shops | 62% reduction |
Allied signal / laminates plant | Capacity, cycle time, inventory, on-time delivery | Up 50%, down 50%, down 50%, increased to near 100% |
Allied signal / bendix IQ brake pads | Concept-to-shipment cycle time | Reduced from 18 months to 8 months |
Hughes aircraft's missiles systems group / wave soldering operations | Quality / productivity | Improved 1000% / improved 500% |
General Electric | Financial | 2 billion USD in 1999 |
Motorola (1999) | Financial | 15 billion USD over 11 years |
Dow chemical / rail delivery project | Financial | 2,45 million USD in capital expenditures |
DuPont / Yerkes plant (2000) | Financial | More than 25 million USD |
Telefonica de Espana (2001) | Financial | 30 million EUR in the first 10 months |
Texas Instruments | Financial | 600 million USD |
Johnson and Johnson | Financial | 500 million USD |
Honeywell | Financial | 1,2 billion USD |
SWOT analysis of Six Sigma
Although benefits and savings achieved by implementing Six Sigma in manufacturing sector seem rather motivating, they should not be used as sole factor for obtaining top management buy-in, since that might lead to unrealistic expectations.
Certain care should be taken in choice of definition presented to top management. Although academic definition encompasses all elements of Six Sigma, it might be better to use simpler, business oriented definitions when securing buy-in from top management.
More realistic and critical approach should be used in order to convey the reasons for Six Sigma implementation, using the managerial language and tools. Therefore, a presentation in the form of concise SWOT analysis is proposed:
SWOT analysis is a strategic analysis tool that considers strengths, weaknesses, opportunities, and threats. Strengths and weaknesses are internal factors, whereas opportunities and threats are external factors. Strengths and opportunities are positives, whereas weaknesses and threats are negatives. – Hill (2012)
You can use SWOT analysis of Six Sigma by Tang et al. (2006) as a starting point, and then adapt you to your own organisational context:
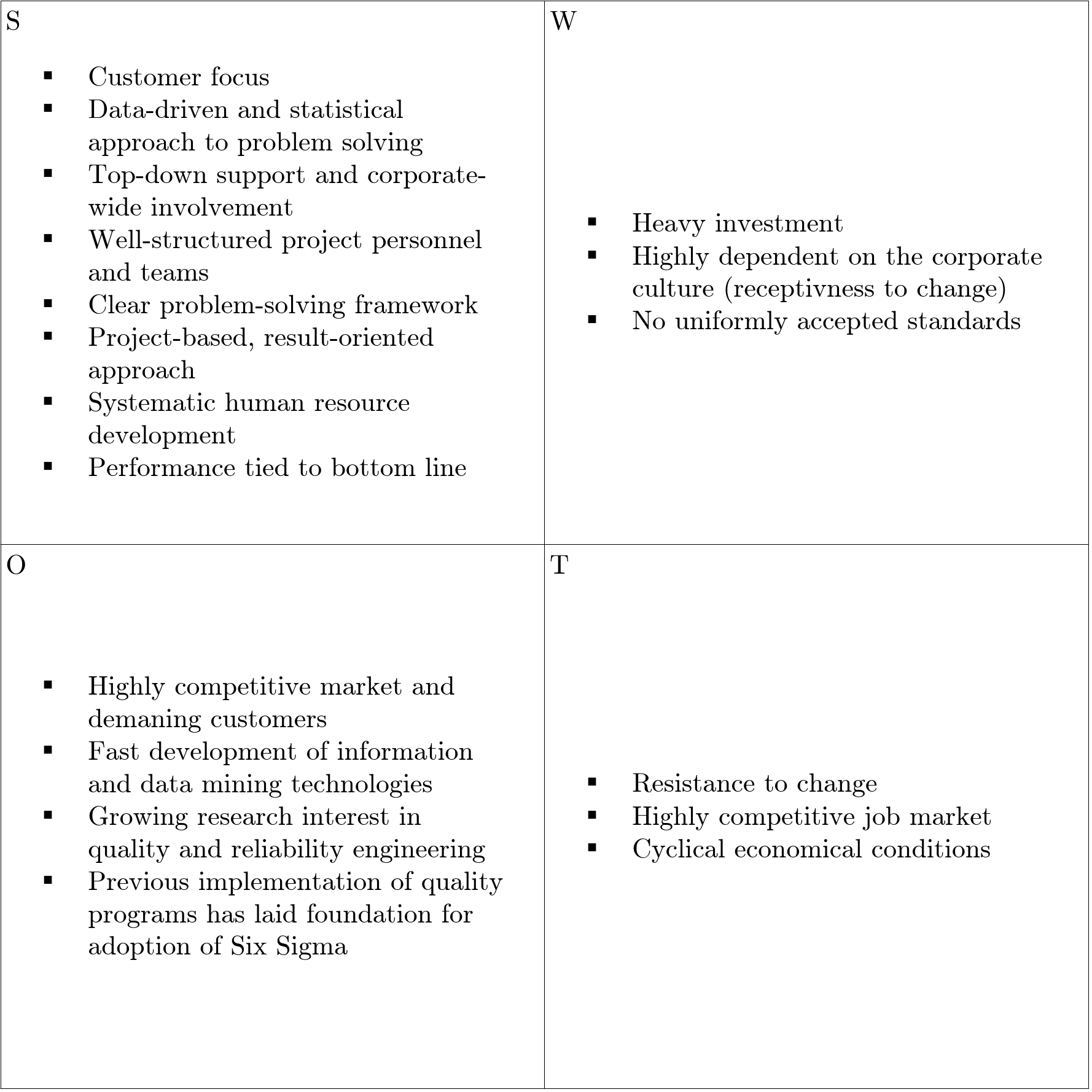
Critical barriers for successful Six Sigma implementation
It is reasonable to assume that organisation should identify potential barriers that could hinder its Six Sigma implementation efforts. Once the barriers have been identified, organisation can plan its future actions and maximise implementation success chances.
Extensive case study by Mohamed (2011) identified 47 barriers, and divided critical barriers into seven categories: knowledge, resources, support complexity, customer focus, sustainability and alignment:
Barrier factor | Variables |
---|---|
Knowledge barrier | Unclear prioritisation of Six Sigma projects |
Lack of knowledge about Six Sigma | |
Satisfaction with other quality programmes | |
Inadequate measurement skills | |
Narrow view of Six Sigma | |
Resource barrier | Large investment in Six Sigma training |
Insufficient time to work on Six Sigma | |
Insufficient financial resources | |
Expensive application of Six Sigma results | |
Lack of dedicated Six Sigma professionals | |
Support barrier | Lack of top management support |
Inadequate specialised Six Sigma training | |
Resistance to change | |
Poor communication of quality data | |
Complexity barrier | Difficulty in identifying process parameters |
Unclear aspects of CTQ | |
Complexity of data analysis | |
Complex Six Sigma tools and techniques | |
Weak presentation of Six Sigma findings | |
Customer focus barrier | Poor measurement of customer satisfaction |
Weak understanding of customer wants | |
Less emphasis on the VOC | |
Unclear COPQ | |
Sustainability barrier | Difficulty to sustain Six Sigma improvements |
Intangibility of Six Sigma results | |
Uncertainty of Six Sigma results | |
Alignment barrier | Unleashed Six Sigma business strategy |
Poor Six Sigma planning and alignment |
Among these barriers, knowledge, support, resources and complexity were identified to have significantly greater inhibiting effect among SMEs than larger organisations. Organisations should prioritise the most obstructing barriers in relation to organisational factors.
Concluding remarks
In previous articles I covered Six Sigma definition, deployment and methods, and organisation and roles. This article presented and overview of benefits and challenges with Six Sigma.
As with any methodology, consultants will be aggressively selling it, so due care should be exhibited. There are still no silver bullets. It's best to be pragmatic and keep whatever works, while discarding all the waste and glut.
Continuous improvement principles are timeless and do not require complex methodologies, dogmatic implementations, or massive investments.
They do require humans that can think, a skill that must be honed all life.
References
Antony, J., Kumar, M., & Madu, C. N. (2005). Six Sigma in small-and medium-sized UK manufacturing enterprises: Some empirical observations. International Journal of Quality & Reliability Management, 22(8), 860–874.
Behara, R. S., Fontenot, G. F., & Gresham, A. (1995). Customer satisfaction measurement and analysis using Six Sigma. International Journal of Quality & Reliability Management, 12(3), 9–18.
Dalgleish, S. (2003). Six Sigma? No thanks. Quality, 42(4), 22.
Das, N., Gauri, S. K., & Das, P. (2006). Six Sigma principles in marketing: An application. International Journal of Six Sigma and Competitive Advantage, 2(3), 243–262.
Desai, D. A. (2006). Improving customer delivery commitments the Six Sigma way: Case study of an Indian small scale industry. International Journal of Six Sigma and Competitive Advantage, 2(1), 23–47.
Douglas, P., & Erwin, J. (2000). Six Sigma’s focus on total customer satisfaction. Journal for Quality and Participation, 45–53.
Freiesleben, J. (2006). Communicating Six Sigma’s benefits to top management. Measuring Business Excellence, 10(2), 19–27.
Ganesh, M. (2004). Six Sigma-time for a reality check. Customer Management, 12(2), 38–39.
Hill, A. (2012). The encyclopedia of operations management: A field manual and glossary of operations management terms and concepts. FT Press.
Kuei, C. H., & Madu, C. N. (2003). Customer-centric Six Sigma quality and reliability management. International Journal of Quality & Reliability Management, 20(8), 954–964.
Kumar, M., Antony, J., Antony, F. J., & Madu, C. N. (2007). Winning customer loyalty in an automotive company through Six Sigma: A case study. Quality and Reliability Engineering International, 23(7), 849–866.
Kumar, M., Antony, J., Madu, C. N., Montgomery, D. C., & Park, S. H. (2008). Common myths of Six Sigma demystified. International Journal of Quality & Reliability Management, 25(8), 878–895.
Kwak, Y. H., & Anbari, F. T. (2006). Benefits, obstacles, and future of Six Sigma approach. Technovation, 26(5–6), 708–715.
Mohamed, G. A. (2011). Reconstructing Six Sigma barriers in manufacturing and service organizations. The International Journal of Quality & Reliability Management, 28(5), 519–541.
Reed, M. (2000). Six Sigma eavesdropping on the Net! Quality Australia, 15(1), 10.
Rylander, D. H., & Provost, T. (2006). Improving the odds: Combining Six Sigma and online market research for better customer service. SAM Advanced Management Journal, 71(1), 13.
Seddon, J. (2003). Freedom from command & control: A better way to make the work work. Vanguard Education Ltd.
Senapati, N. R. (2004). Six Sigma: Myths and realities. International Journal of Quality & Reliability Management, 21(6), 683–690.
Smith, L. (2004). Six Sigma goes to Washington. Quality Digest.
Tang, L. C., Go, T. N., Yam, H. S., & Yoap, T. (2006). Six Sigma: Advanced tools for black belts and master black belts. Wiley.
Usher, J. (2008). Sick of sigmas. Modern Materials Handling, 63(5), 19–19.
This article is a part of Six Sigma series:
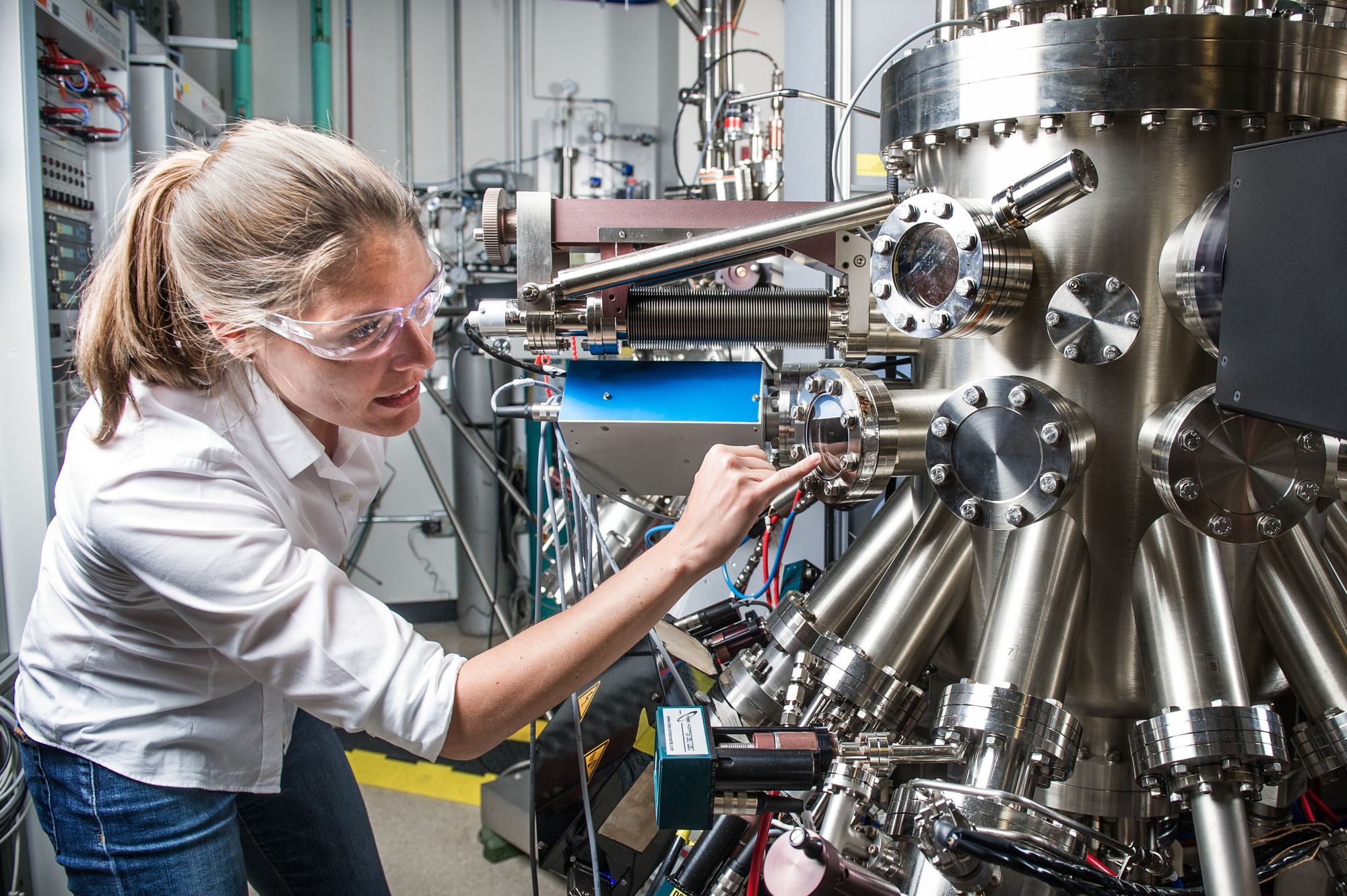
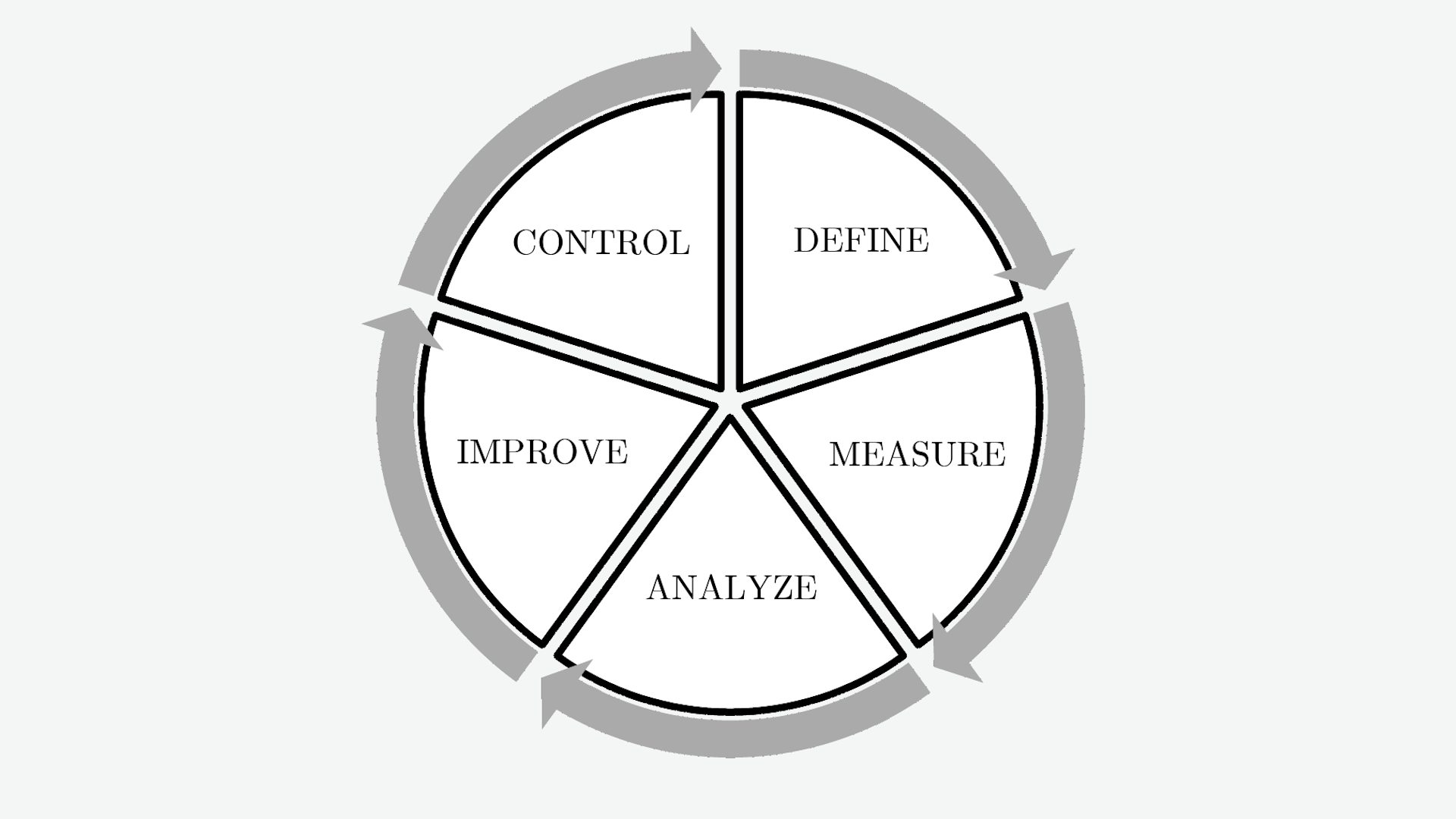
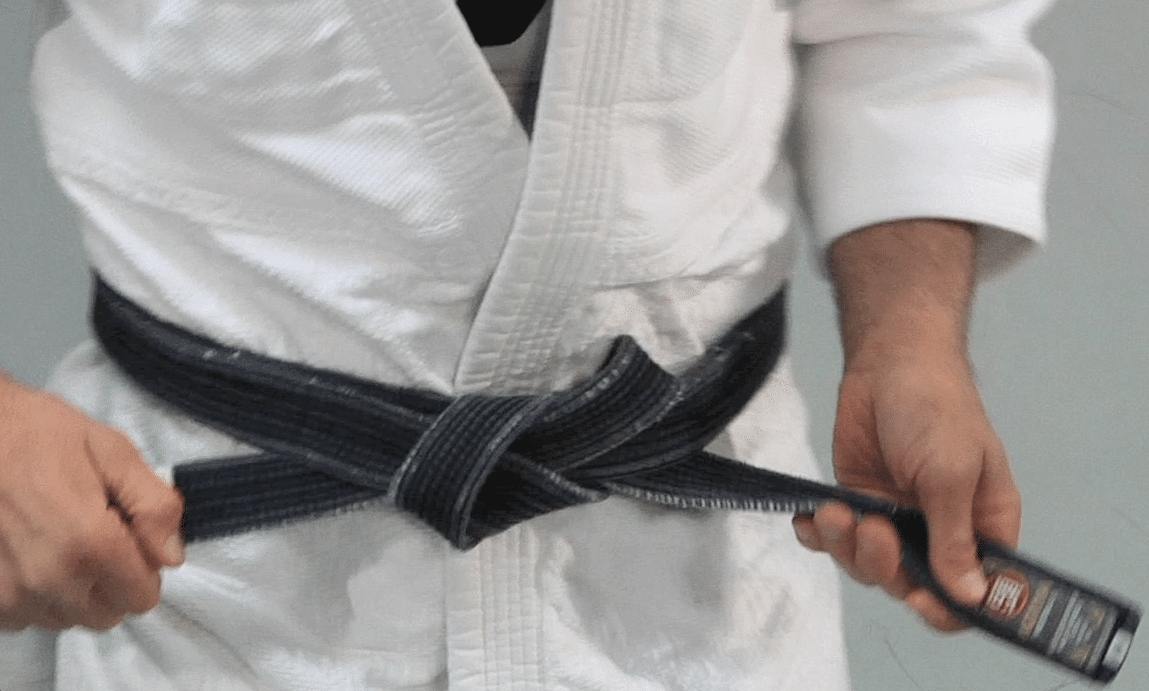
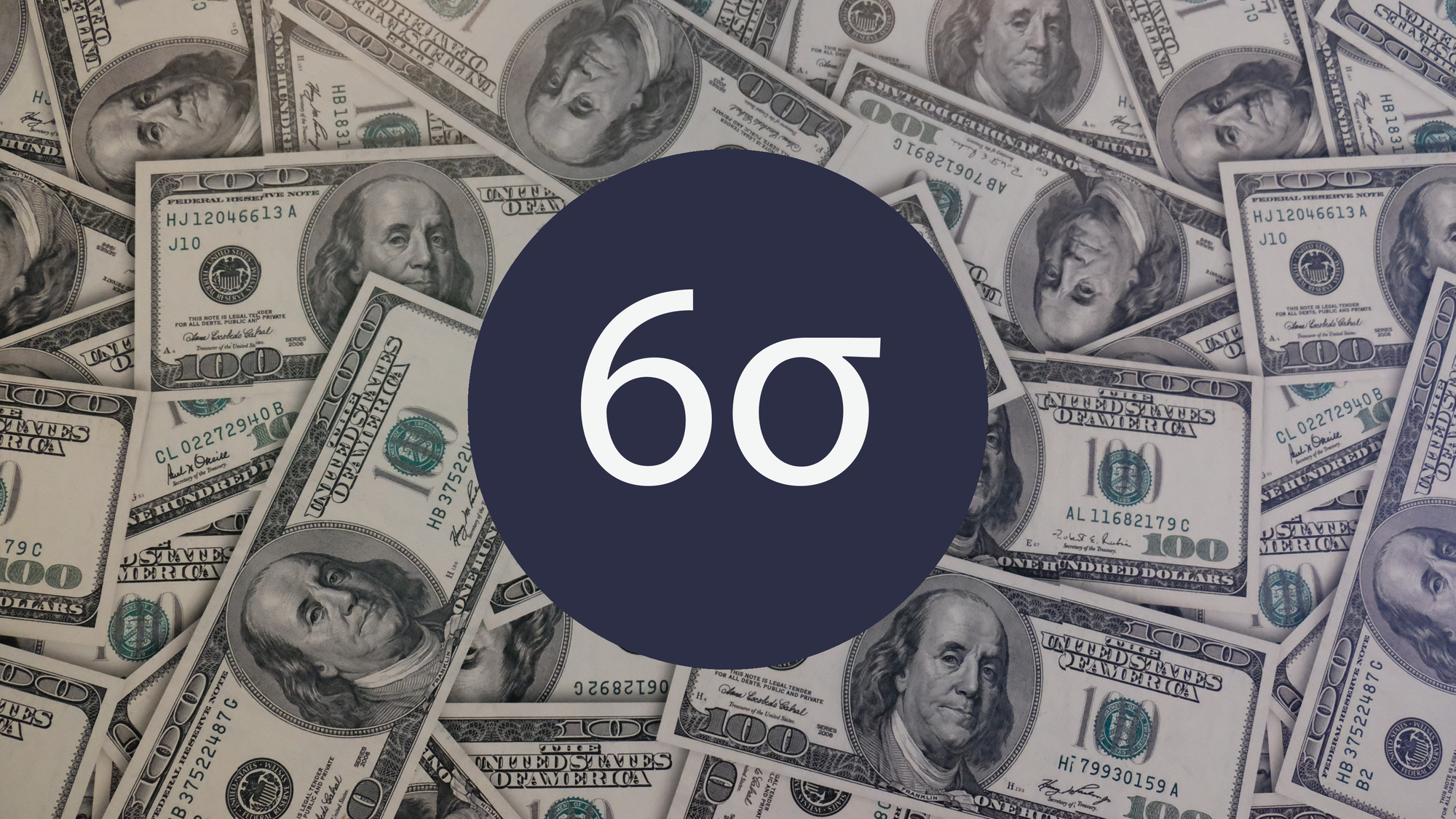
Bruno Unfiltered
Subscribe to get the latest posts delivered right to your inbox. No spam. Only Bruno.