Six Sigma: organisation and roles
How does successful Six Sigma organisation look like? What are key roles and their responsibilities?
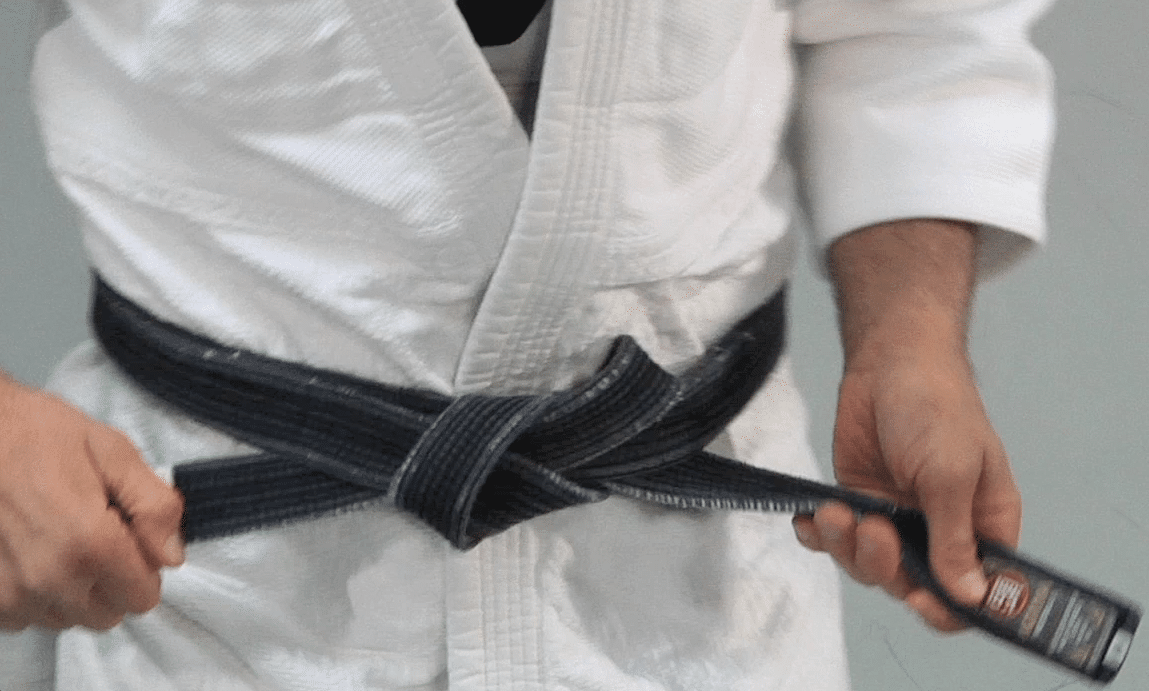
Six Sigma has unique team infrastructure, consisting of green belt, black belt, master black belt, champion and executive sponsor. Reporting hierarchy is presented in the figure below:
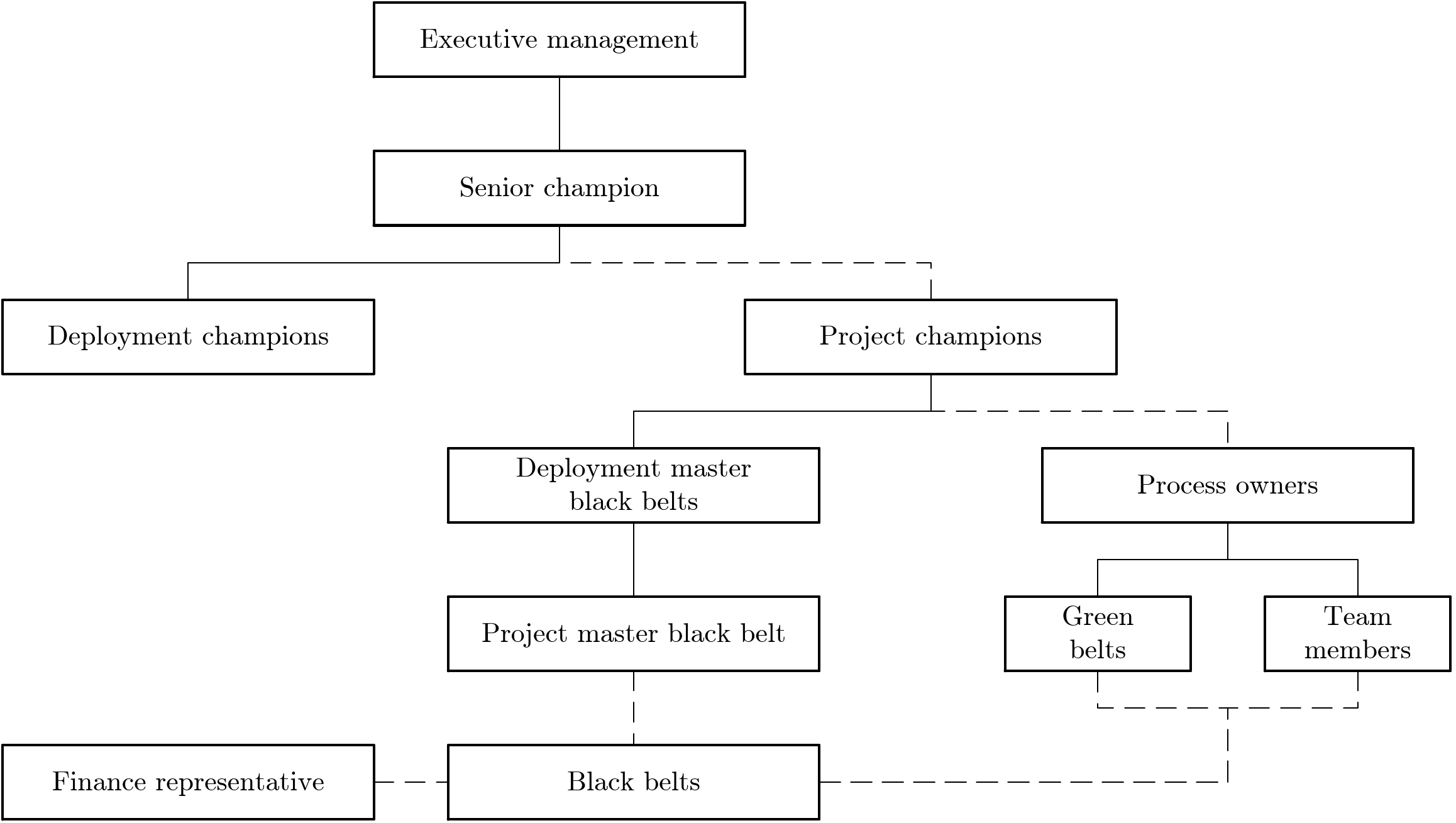
Tang et al. (2006), and Nonthaleerak & Hendry (2008) stress that team and reporting infrastructure are considered to be one of the key elements for the successful Six Sigma implementation.
Let's look at each role.
Executive sponsor
The executive sponsor should communicate, lead, and direct the organisations overall objectives toward successful and profitable Six Sigma implementation. Without direct involvement and complete commitment of executive management implementation will inevitably fail (Taghizadegan, 2006; Arthur, 2011).
Champion
Champion is responsible for selecting employees which shall receive Six Sigma training, for project selection and monitoring, for communication between belts and executive management, and for supporting the Six Sigma philosophy across the organisation.
Senior champion should be chosen from executive management, while project champions should be from either executive or top management. Project champions report to senior champion, who in turn reports to CEO.
Master black belt
Master black belt (MBB) is responsible for guidance and education of black and green belts. MBB should possess deep understanding of all tools used within Six Sigma, leadership skills and preferably high emotional intelligence (Milivojevich, 2006). It should be considered as full-time position. MBB should be chosen from the best black belts.
Black belt
Black belt (BB) is the technical leader of the Six Sigma project. They report to the project MBB and finance representative, while project team (or teams) report to him. It is possible to have BBs as full-time or part-time position. Nonthaleerak & Hendry (2008) discuss advantages and disadvantages of these two position patterns:
Pattern | Advantages | Disadvantages |
---|---|---|
Full time | Highly motivated, dedicated to the project, can handle cross-functional large-scale complicated projects. | No authority in the improved area, less cooperation if the BB status is mismanaged, higher cost. |
Part time | Project is integrated into day-today work, belt have authority as project are undertaken in their are of responsibility, gain co-operation as working in the area, lower cost. | High workload, belts have less motivation and less satisfaction doing projects, project can be delay, limited scope of project due to time constraints. |
Arthur (2011) emphasises that black belts should have improvement, process-oriented, problem-solver mindset. Gupta (2005) defines black belt body of knowledge as follows:
Elements | Knowledge required |
---|---|
Enterprise-wide deployment | Value, systems and processes, leadership roles and responsibilities, organizational goals and objectives, key metrics and scorecards, project selection process. |
Business process management | Process versus functional view, project measures, VOC, customer requirements, PPM, DPMO, DPU, rolled throughput yield, COPQ, benchmarking. |
Project management | Project charter, planning tools, team leadership, team tools, managing change, organizational roadblocks, communication. |
Define | Project scope, top-level process maps, metrics, problem statement, baseline and improvement goals. |
Measure | Process analysis and documentation, descriptive and inferential statistics, MSA, $C_p$, $C_{pk}$, $P_p$, $P_{pk}$, $C_{pm}$, Sigma levels. |
Analyze | Multivariable studies, regression analysis hypothesis testing, ANOVA, test for means, variances and proportions, nonparametric test. |
Improve | DOE (full-factorial and Taguchi), significance of results, response surface methodology, evolutionary operations. |
Control | Statistical process control, rational subgrouping, control charts, precontrol, short-run SPC, EWMA, MSA. |
DFSS | QFD, robust design, FMEA, DFM, TRIZ. |
He also defines following as key black belt tools and techniques:
Elements | Tools and techniques |
---|---|
Define | Survey, storyboarding, focus groups, affinity diagram, QFD, pareto chart, SIPOC, CTQ, force field analysis, project charter. |
Measure | Terminology, COPQ, normal distribution, MSA, $C_p$, $C_{pk}$, $P_p$, $P_{pk}$, $C_{pm}$, DPU, DPMO, rolled throughput yields, probability distributions, sampling. |
Analyze | PDCA cycle, scatter diagram, stem and leaf plot, box plot, cause and effect analysis, fault tree analysis, mutivariabe analysis, FMEA, tree diagram, regression analysis, hypothesis testing, ANOVA. |
Improve | TRIZ, comparative experiments, components search, DOE, response surface methodology for optimization, nonparametrc test, advanced statistics, team-building skills. |
Control | Leadership and facilitation skills, process thinking, precontrol charts, control charts, internal audits, corrective action and management review process, Six Sigma Business Scorecard. |
Green belt
Green belt (GB) is considered to be a team participant. They work with black belts in projects, and should have knowledge of the process being optimised. They report to both process owners and BB. According to Gupta (2005), key green belt tools and techniques are:
Elements | Tools and techniques |
---|---|
Define | Pareto chart, process mapping, SIPOC. |
Measure | Terminology, COPQ, normal distribution, MSA, $C_p$, $C_{pk}$, DPU, DPMO. |
Analyze | Cause and effect analysis, mutivariabe analysis, FMEA, regression analysis, hypothesis testing, ANOVA. |
Improve | TRIZ, comparative experiments, components search, full factorial experiments, response surface methodology for optimization. |
Control | Process thinking, precontrol charts, control charts, internal audits, corrective action and management review process, Six Sigma Business Scorecard, TOC. |
Abbreviations explained
Since there are a lot of abbreviations in the tables above, here is another table:
Term | Meaning |
---|---|
ANOVA | Analysis of variance |
COPQ | Cost of poor quality |
Cp | Process capability index |
Cpk | Process capability index (equivalent) |
Cpm | Process capability index (Taguchi) |
CTQ | Critical to quality |
DFM | Design for manufacturing |
DFSS | Design for Six Sigma |
DOE | Design of experiments |
DPMO | Defects per million opportunities |
DPU | Defects per unit |
EWMA | Exponentially weighted moving average |
FMEA | Failure mode and effects analysis |
MSA | Measurement System Analysis |
Pp | Process performance index |
Ppk | Long-term capability of the process |
PPM | Parts per million |
QFD | Quality Function Deployment |
SIPOC | Suppliers, inputs, process, outputs, and customers |
SPC | Statistical process control |
TOC | Theory of Constraints |
TRIZ | Theory of inventive problem solving |
VOC | Voice of customer |
Concluding remarks
This article dealt with two questions – How does successful Six Sigma organisation look like? and What are key roles and their responsibilities?
Improvement specialists are crucial in deployment and execution of successful Six Sigma programmes – but they need to be coupled with an appropriate executive sponsor and politically savvy champions. In their work they rely on a wide range of engineering, statistical, and managerial tools and techniques.
References
Arthur, J. (2011). Lean Six Sigma demystified (2nd ed.). McGraw-Hill.
Gupta, P. (2005). The Six Sigma performance handbook: A statistical guide to optimizing results. McGraw-Hill.
Milivojevich, A. (2006). Emotional intelligence and Six Sigma. Quality Progress, 39(8), 45–49.
Nonthaleerak, P., & Hendry, L. (2008). Exploring the Six Sigma phenomenon using multiple case study evidence. International Journal of Operations & Production Management, 28(3), 279–303.
Taghizadegan, S. (2006). Essentials of Lean Six Sigma. Elsevier.
Tang, L. C., Go, T. N., Yam, H. S., & Yoap, T. (2006). Six Sigma: Advanced tools for black belts and master black belts. Wiley.
This article is a part of Six Sigma series:
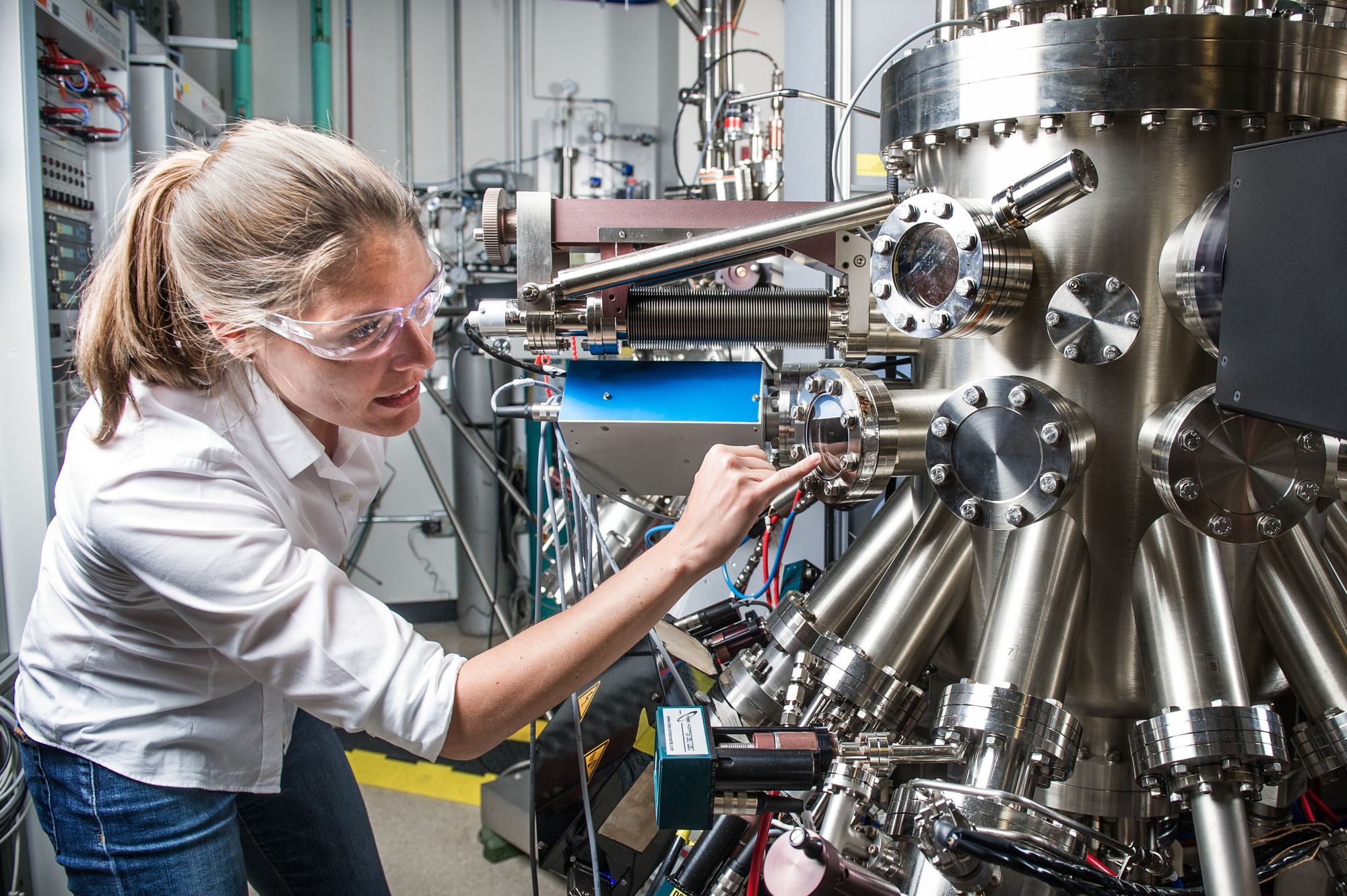
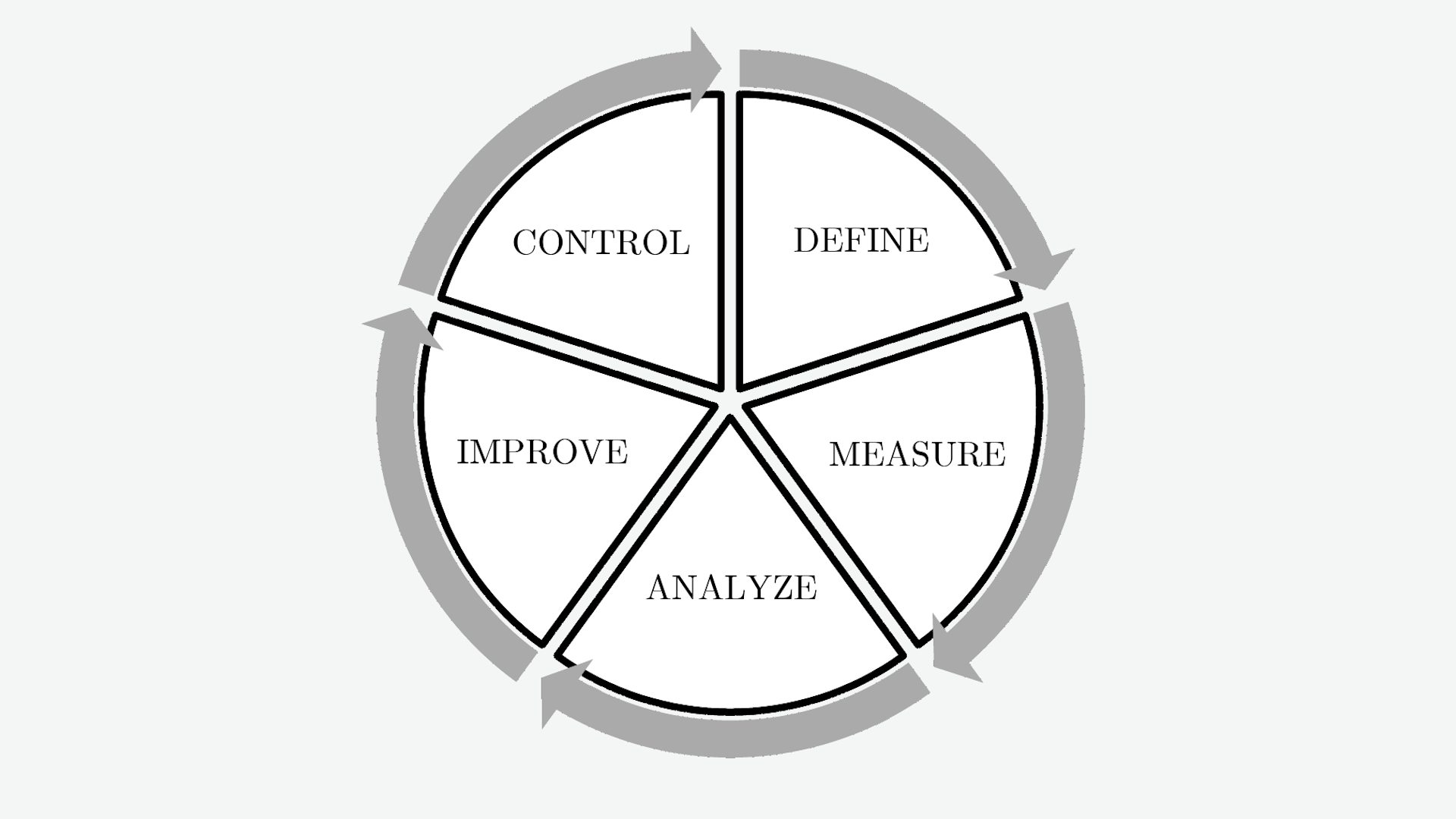
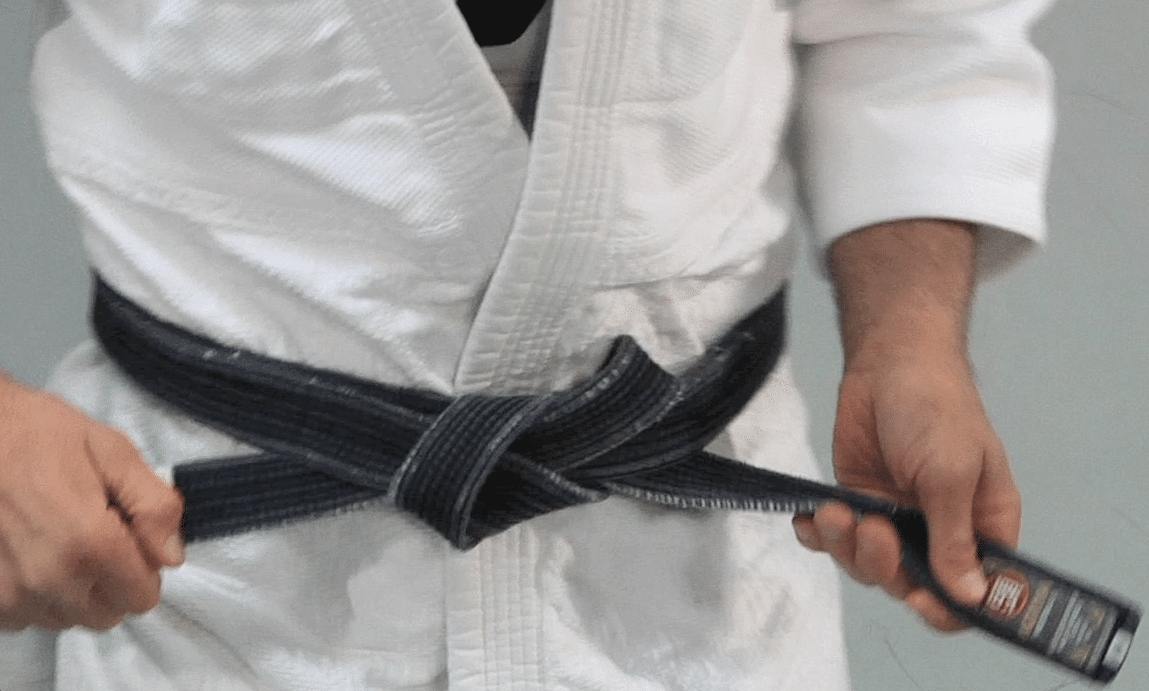
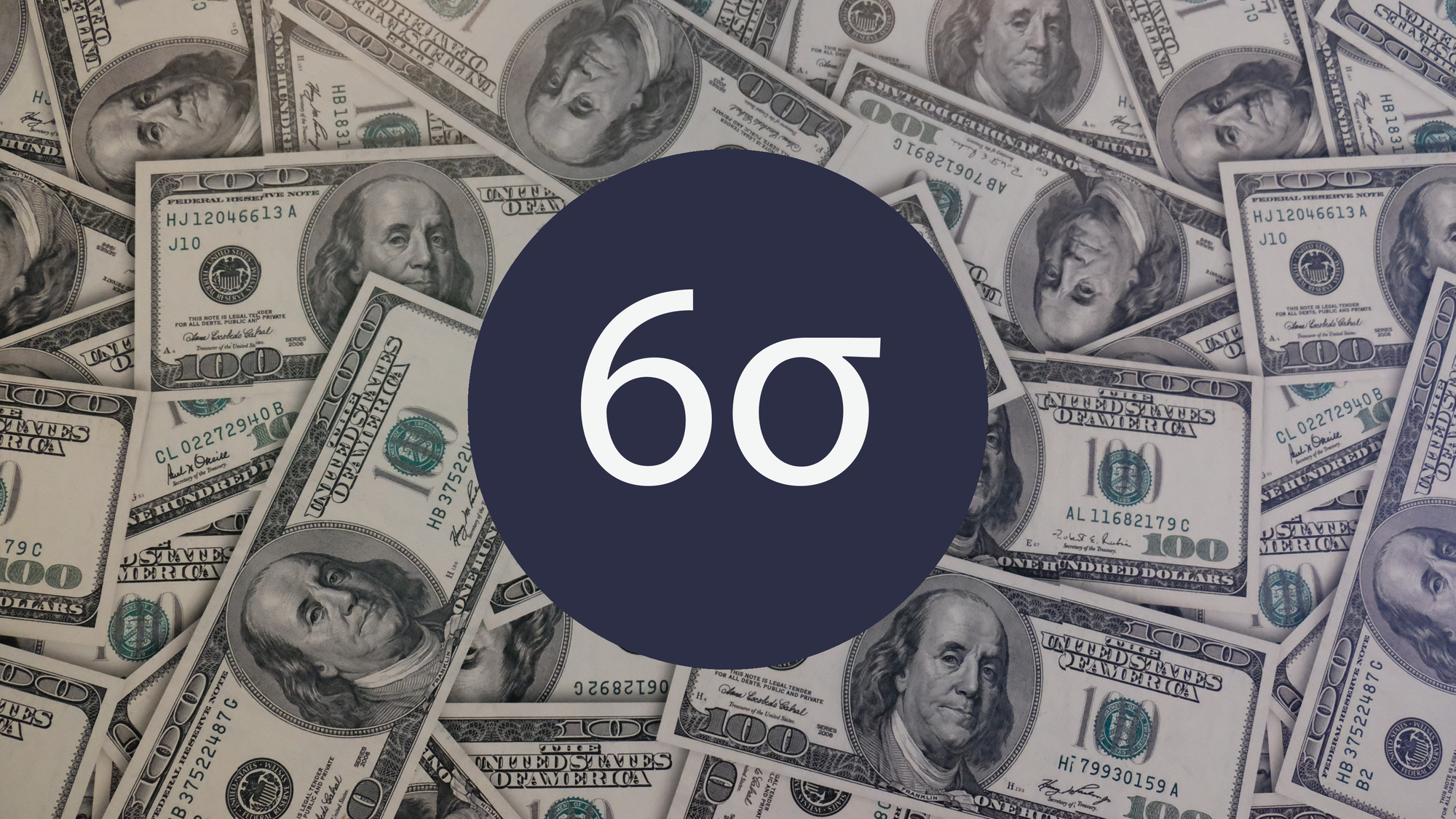
Bruno Unfiltered
Subscribe to get the latest posts delivered right to your inbox. No spam. Only Bruno.