Lean Thinking: critique
Is lean thinking a copy of the Toyota Way or a standalone philosophy built upon two powerful paradigms of the past?
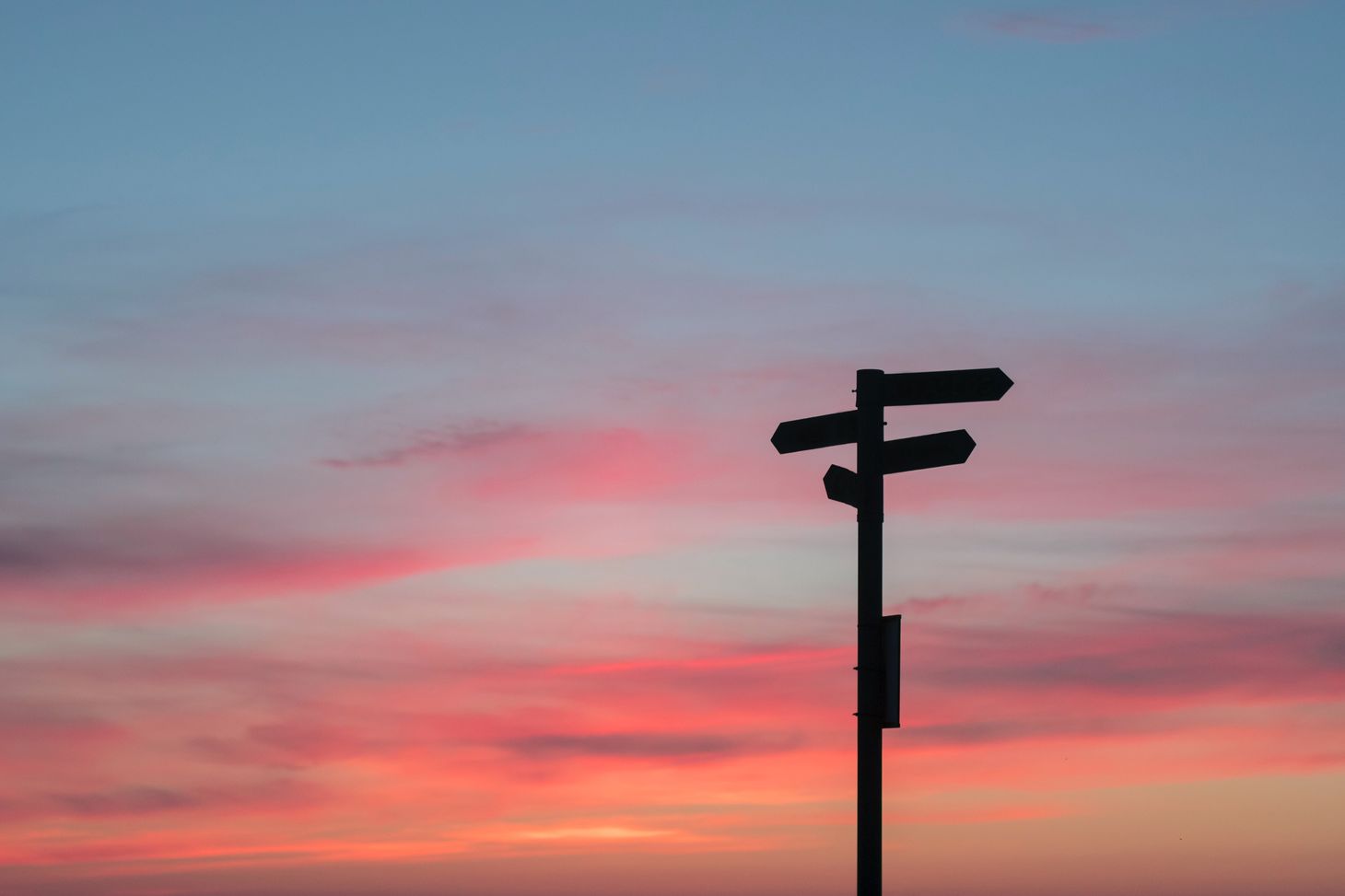
Womack and Jones (Womack et al., 1990; Womack & Jones, 2003) listed a number of benefits achieved by initial implementation of lean thinking:
- double labour productivity through the system,
- production throughput times reduced by 90%,
- inventories in system reduced by 90%,
- defects reaching the customer are cut by half,
- job-related injuries are cut by half, and
- halved time-to-market for new products.
After initial benefits, further benefits are usually achieved within two to three years, resulting in growth as long term benefit.
Numerous publications since the inception of lean assessed various aspects, from benefits, implementation, enablers, sustainability, evolution from lean manufacturing to lean thinking, etc (Stone, 2012). Aforementioned evolution should not be overlooked, as it represent new challenge for lean practitioners.
Ohno on tools
Lean thinking is firmly rooted in manufacturing sector, and while its principles are universal the same does not apply to its tools.
Taichi Ohno was strongly against codifying tools used within Toyota Production System (Ohno 1988; Shimokawa & Fujimoto, 2009). The fact that Toyota Production System was created from need, and not vice versa, should never be overlooked.
Following aforementioned line of thought, such approach should be taken when facing novel problem. Instead of forcing the application of inadequate tool or technique, new tool or technique should be devised. Such approach results in tool that is aligned to the need.
Varying levels of leanness
In Lean Thinking: origin, we defined lean thinking as the operational philosophy of the organisation.
Key term is philosophy.
The principles of lean thinking can be applied at process, shop-floor, department, factory, organisation and supply chain level. For such limited applications term implementation should be used.
Consequently, limited applications yield limited benefits. Applying lean thinking as organisational philosophy is an organisational effort which requires complete dedication of top management (Womack et al., 1990).
Instituting lean thinking solely as a Quality Management System or Continuous Improvement methodology means that it will be limited by certain organisational boundaries, and as discussed earlier, will yield limited benefits.
Technical solution for technical problem
Although certain benefits should be expected from limited implementation of lean, organisations should restrain from merely adopting technical solution for technical problems.
Banality of evil by Arendt (1963) presents an extreme example of technical solution for technical problem. Internal change became impossible since actors justified their actions and had no urge to change.
Extending that concept to the manufacturing, it can be reasoned that applying lean thinking purely as technical solution for technical problem, without supporting philosophy and principles, there is high risk that banalisation of tools will occur.
That could lead to diminished results, or in worst-case scenario, to failed implementation. Such reasoning could be detrimental in the long term, as internal change could became severely inhibited.
Lean transformation has the highest chance of success if it is strategically aligned throughout the organisation.
Identity crisis
The Lean Enterprise Institute could be considered as formal body which defines lean thinking. Its founders defined lean in the 1990s, and continued to work on further promotion.
Based on the information presented in Lean Thinking: origin, Lean Thinking: principles and tools, and Lean Thinking: assessing leanness, it can be said that lean thinking is a generalisation of the Toyota Production System.
Also, it can be noted that Toyota Motor Corporation continues to strongly influence lean thinking (for example the Toyota Way publications).
While that might not be necessarily bad, the question is what lean thinking ultimately aims to be: a copy of the Toyota Way or a standalone philosophy built upon two powerful paradigms of the past?
References
Arendt, H. (1963). Eichmann in Jerusalem: A report on the banality of evil. Penguin.
Ohno, T. (1988). Toyota production system: Beyond large-scale production. Productivity Press.
Shimokawa, K., & Fujimoto, T. (Eds.). (2009). The birth of lean: Conversations with Taiichi Ohno, Eiji Toyoda, and other figures who shaped Toyota management. Lean Enterprise Institute.
Stone, K. B. (2012). Four decades of lean: A systematic literature review. International Journal of Lean Six Sigma, 3(2), 112–132.
Womack, J. P., & Jones, D. T. (2003). Lean thinking: Banish waste and create wealth in your corporation (2nd ed.). Free Press.
Womack, J. P., Jones, D. T., & Roos, D. (1990). The machine that changed the world: Based on the Massachusetts Institute of Technology 5-million dollar 5-year study on the future of the automobile. Rawson Associates.
This article is a part of Lean Thinking series:
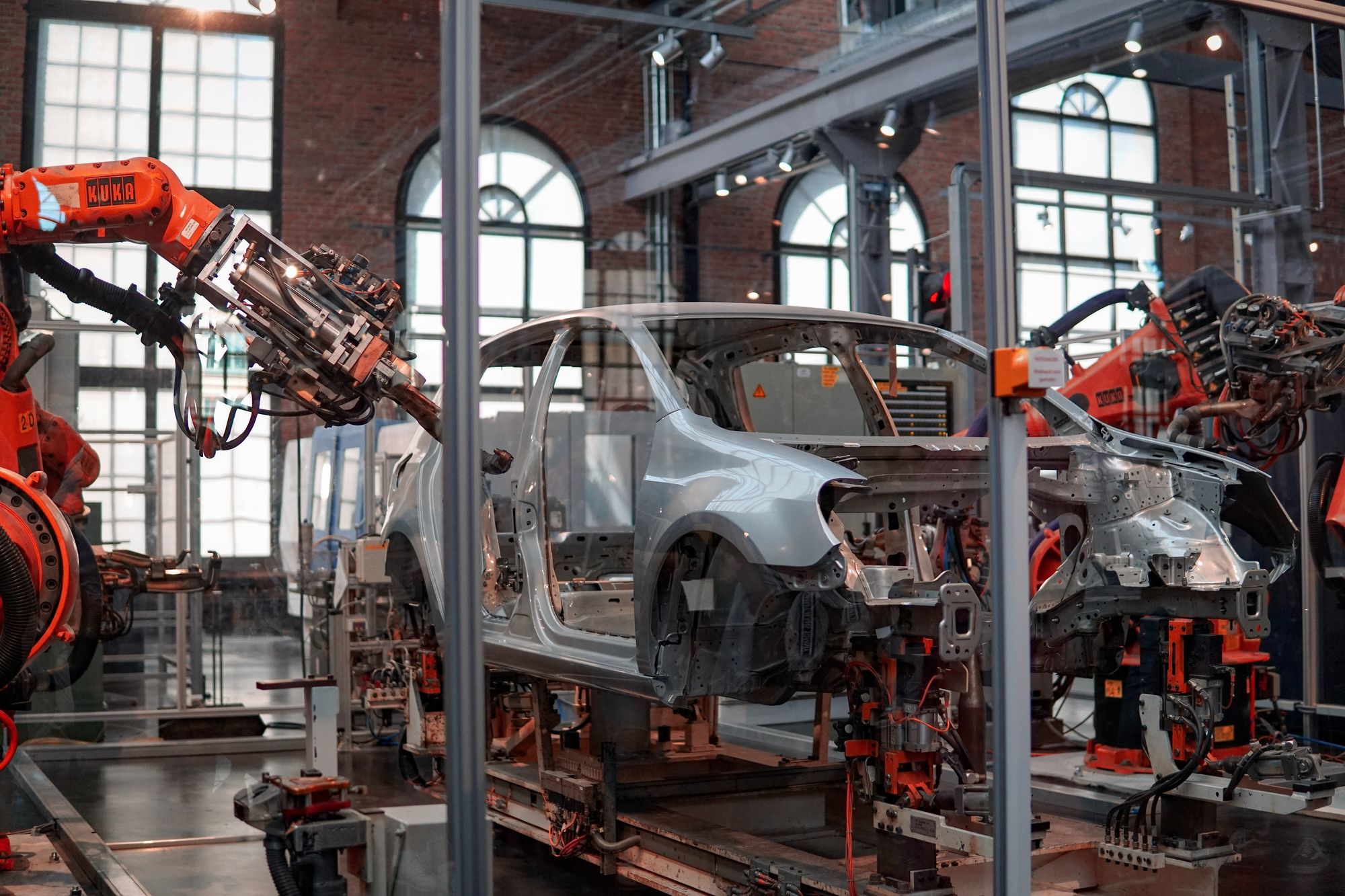
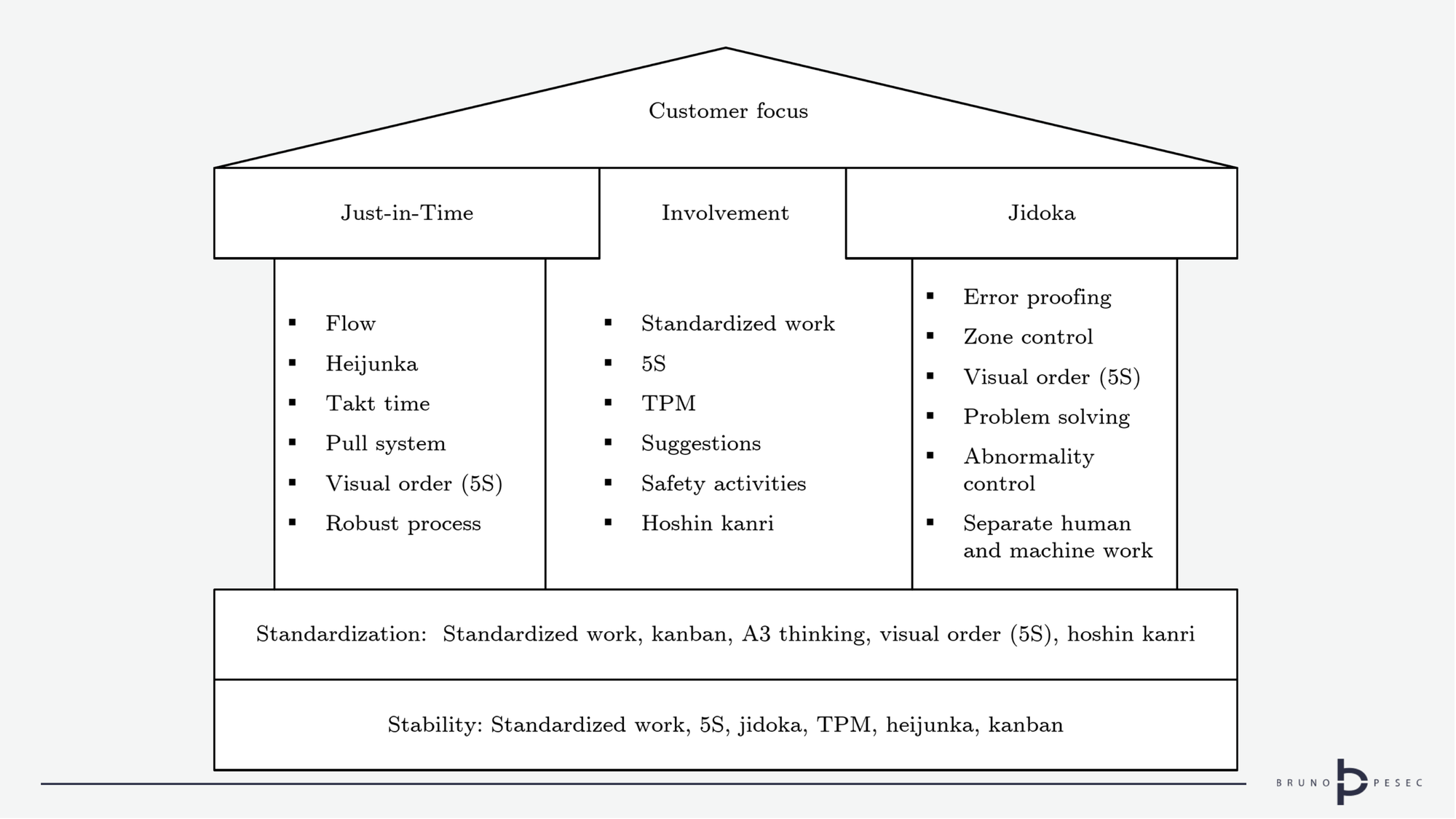
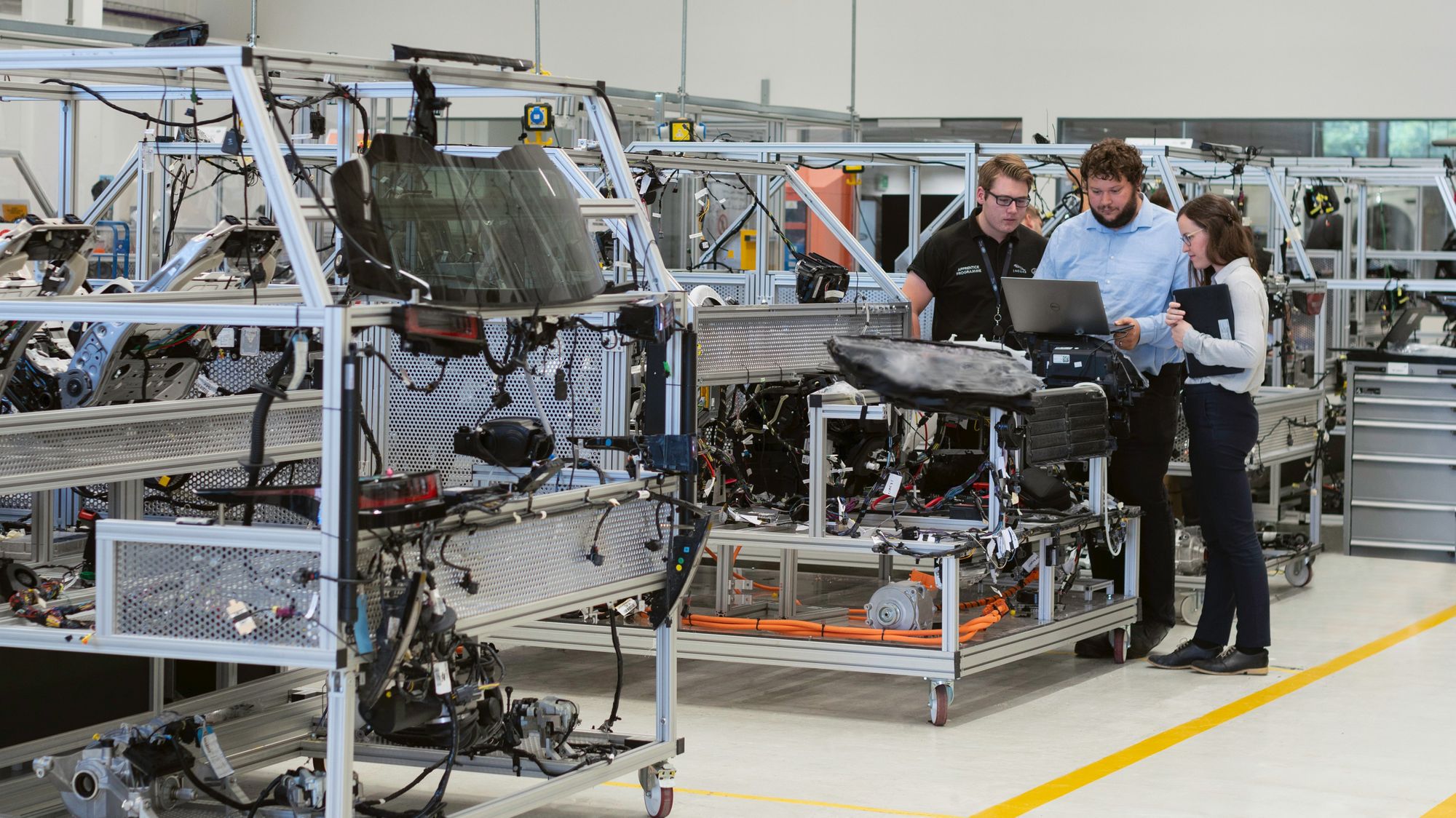
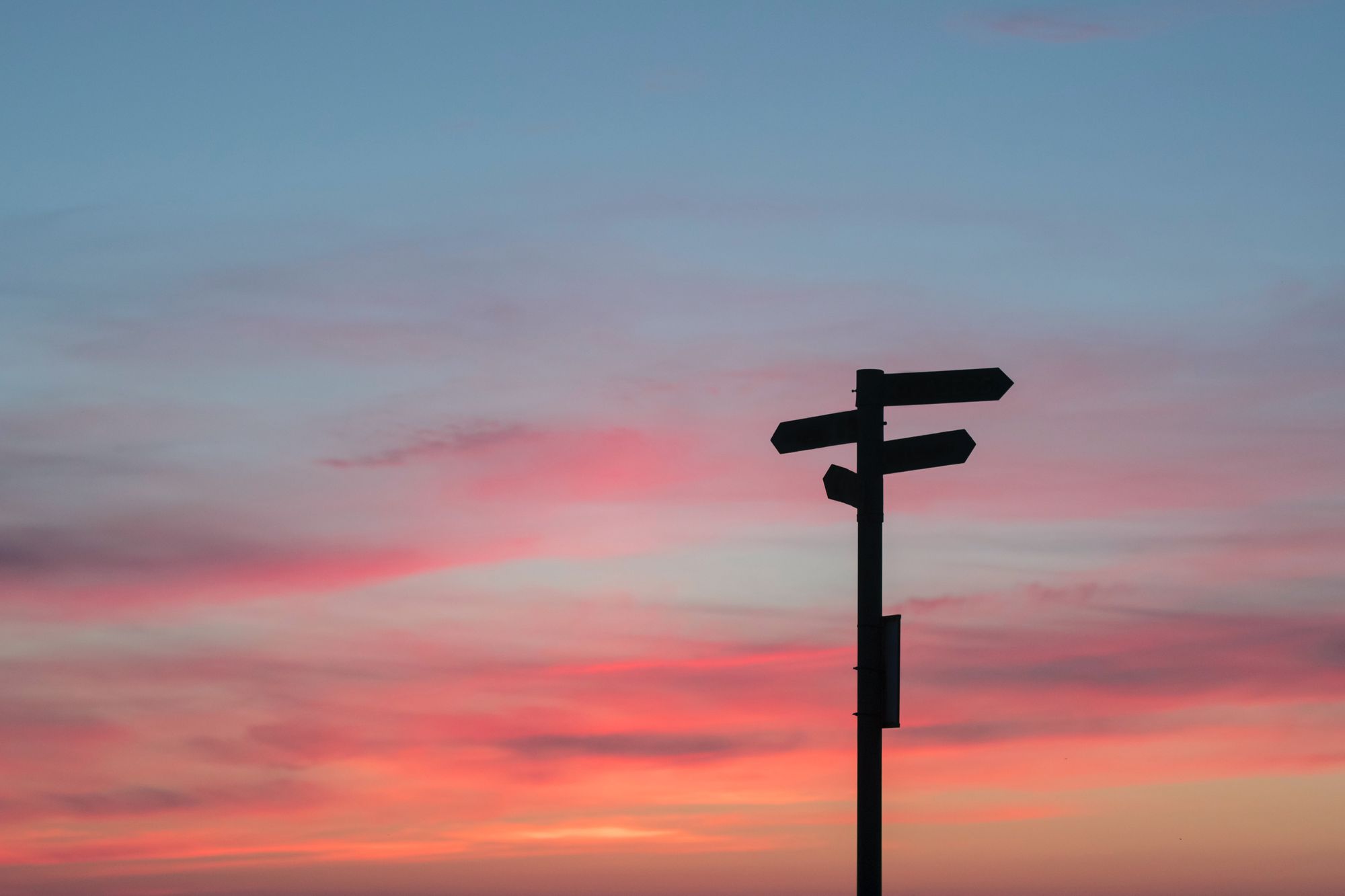
Bruno Unfiltered
Subscribe to get the latest posts delivered right to your inbox. No spam. Only Bruno.