Lean Thinking: origin
A journey from mass manufacturing to Toyota Production System to Lean Thinking.
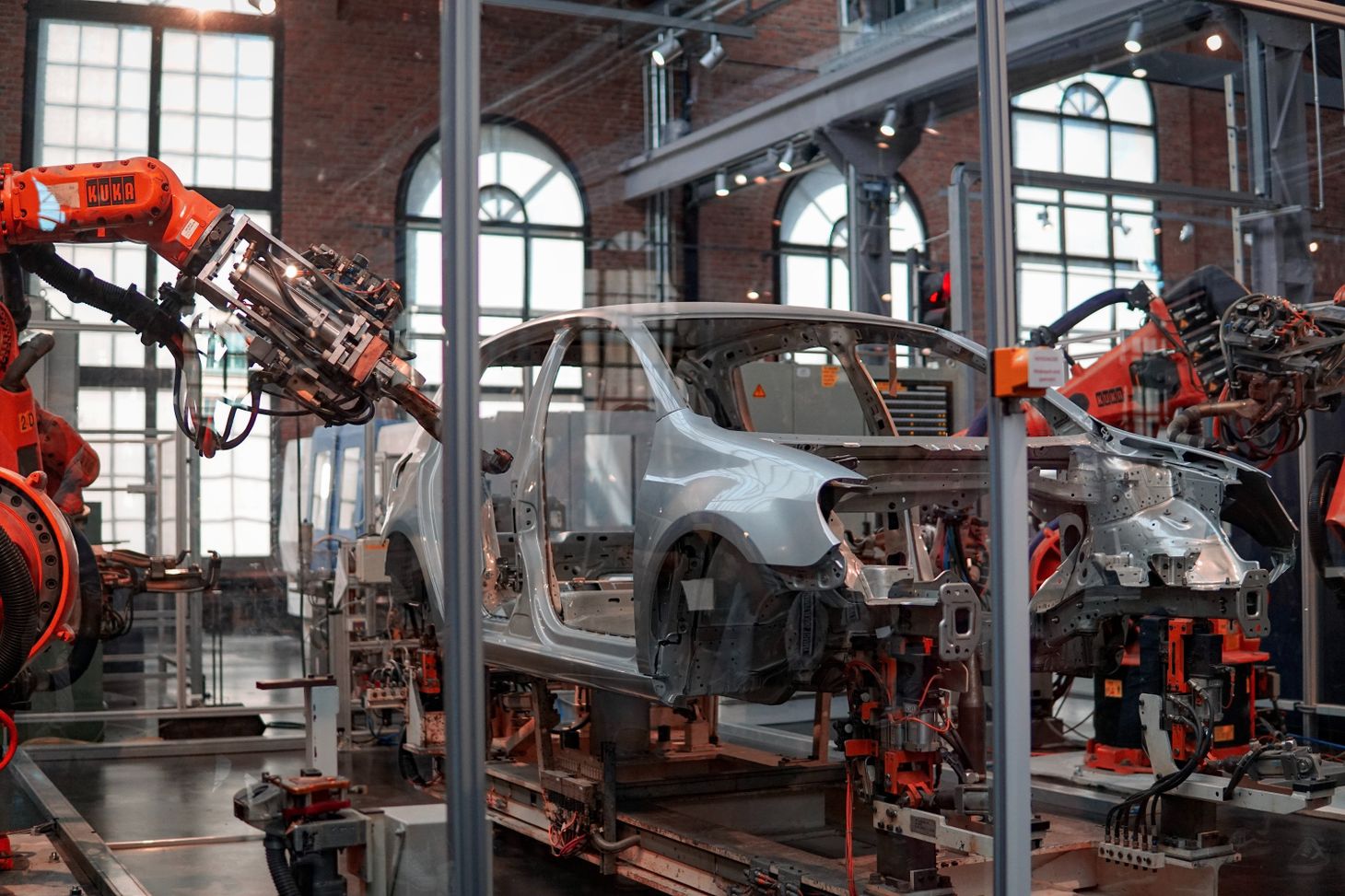
Womack and Jones (2003) defined lean thinking as s an antidote for waste.
Definition I use is slightly modified version of Stone's* (2012):
- lean thinking refers to the operational philosophy of the organisation,
- lean principles refer to underlying theories of lean thinking strategies,
- lean tools refer to tools used to execute lean thinking strategies, and,
- leanness describes the state of the organisation's transformation to lean thinking.
In the Lean Thinking article series I will cover four topics listed above.
Let's go on an amazing journey into the past.
* Stone (2012) defines lean principles as tools used to execute lean thinking strategies. Since the word principles is synonym for rules, the author's definition remains unclear. Although it could be argued that rules could be used as tools, it has been decided to break down the definition to lean principles and lean tools. The aim of such disambiguation is to separate the theory (principles) upon which tools are built and used.
From mass manufacturing to Toyota Production System to Lean Thinking
Lean thinking has its roots in both mass production and Toyota Production System.
Henry Ford pioneered the mass production (Davies & Hounshell, 1985) by achieving high rate of part interchangeability and implementing moving assembly line. In the same period Frederick Winslow Taylor established scientific management (Taylor, 1911).
Ford adopted and applied scientific management, resulting in layered organisational structure where it was expected that workers will obediently work while management would do the thinking. Such approach to workforce led to change in labour relations and worker unions (Katz, 1985). Later Alfred Pritchard Sloan of General Motors added the business elements to the mass production (Womack et al., 1990; Sloan, 1964), like marketing and management techniques.
While mass production was strong in the Unites States, it faced resistance in European countries which were still predominately oriented towards craft production. Ford achieved what he referred to as the true mass production in 1927 at the Rogue complex (Womack et al., 1990).
A number of people visited the complex and discussed the principles of mass production with Ford. Some of these people were from Europe and planned to implement mass principles in their home countries, but their efforts were abruptly stopped when Second World War broke out. After the war ended, knowledge transfer was resumed and mass production started to spread in Europe.
After almost five decades of evolution, in 1955 mass production was a mature system dominating the manufacturing sector. Companies which adopted mass production early, like Ford and General Motors, were producing high volume of products and kept pushing it into the market.
Worker dissatisfaction became focus of numerous research papers, unions were fighting with higher management (Katz, 1985), companies were competing solely on the basis of product or service cost (Womack et al., 1990), quality was considered as additional cost and product customisation was low.
Still, without the critical mass or agent of change there was no incentive for further development of the system.
In 1920s Sakicihi Toyoda laid foundations for the Toyota way by devising two problem-solving approaches, namely jidoka and five-whys (Ohno, 1988; Mass & Robertson, 1996). Later Kiichiro Toyoda, inspired by the Rogue complex, came to the idea of just-in-time (Ohno, 1988).
After Second World War Japan was economically devastated, and United States instituted new labour laws (Nishiguchi, 1989). Toyota Motor Corporations wished to implement mass production, but soon realised that they lack resources required to do so.
Taichi Ohno and Shigeo Shingo started to devise new approach to production, adequate to conditions of post-war Japan (Shimokawa & Fujimoto, 2009). That approach was later named Toyota Production System (TPS) (Ohno, 1978; Ohno, 1988), and eventually evolved into the Toyota Way (Toyota motor corporation, 2012).
Toyota educated its first tier suppliers in TPS, while they would then proceed to educate their first tier suppliers (second tier suppliers of Toyota). Such knowledge transfer cascaded downstream, and was additionally supported (or enforced) by keiretsu, a type of informal business group.
Hill, (2012) defines keirtesu as a set of companies with interlocking business relationships and shareholdings. In The machine that changed the world (Womack et al., 1990) keiretsu groups are briefly described, mostly in positive tone.
Keiretsu groups might have had significant impact on the success of the Toyota Production System (Lincoln et al., 1996; Dyer, 1996). There are a number of papers assessing keiretsu system (Gilson & Roe, 1993; Ahmadjian & Lincoln, 2001; McGuire & Dow, 2003), yet there are virtually no papers assessing the relation between keiretsu system and lean. This interesting knowledge gap is unlikely to be filled due to closed nature of Japanese businesses.
Successful implementation of the new manufacturing paradigm imposed by TPS allowed Japanese businesses, specifically Toyota, to penetrate the world market.
In 1984 International Motor Vehicle Program (IMVP), founded at the Massachusetts Institute of Technology, launched an extensive benchmarking study of automotive industry. The result was a book The Machine that Changed the World, which marked the beginning of lean paradigm.
During the study Taichi Ohno's and Masaaki Imai's books were translated into English (Ohno, 1988; Imai, 1986) providing valuable insight into the elements of TPS.
The study has stated that lean is the paradigm of the future and that mass production should be abandoned as soon as possible. Still, without adequate theoretical models and frameworks, companies could not undertake lean transformation process.
Those companies which did start to implement lean principles usually had some link to Japanese businesses (Womack et al., 1990). In order to provide underlying theory for lean implementation and transformation Womack founded The Lean Enterprise Institute, followed by two publications explaining lean fundamentals (Womack, 1996; Rother, 1999).
In 2000s publications from Jeffrey Liker (Liker, 2004; , Liker, 2006; Liker, 2008;, Liker, 2011) provided even more insight in the Toyota way, enriching the lean thinking in the fields of management, leadership and culture. It can be concluded that publications of The Lean Enterprise Institute and Jeffrey Liker are the most representative of the lean body of knowledge.
Table below presents historical overview of mass production, the Toyota way and lean thinking. It should be noted that the emphasis was on presenting the publications and achievements which were enablers for each of aforementioned paradigms.
Mass production is covered from 1900s to 1960s, emphasizing the work of Henry Ford. After 1960s two new major paradigm shifts are mentioned, namely flexible production (Tolio, 2008) and mass customization (Blecker & Friedrich, 2006).
The Toyota Way is covered from 1920s to 2000s, emphasizing the creation of the TPS and later evolution to the Toyota Way. 5R programme is mentioned since it represent Toyota's efforts to implement environmental aspects into the TPS (Toyota Motor Corporation, 1999). Five R's are refine, reduce, recycle and retrieve energy.
Lean thinking is covered from 1990s to 2010s, from inception of the term lean to latest publications. Emphasis was put on the publications of The Lean Enterprise Institute and Jeffrey Liker.
Historical overview of mass production, the Toyota way and lean thinking:
Period | Mass production | The Toyota Way | Lean Thinking |
---|---|---|---|
1798 | Eli Whiteney - Interchangeable parts | ||
1900s | 1908 Henry Ford achieves perfect part interchangeability | ||
1910s | 1911 Frederick W. Taylor - Principles of Scientific Management | ||
1913 Henry Ford implements moving assembly line | |||
1913 Henry Gantt - Gantt charts | |||
1915 Transition to mass production | |||
1920s | Sakichi Toyoda - Jidoka and Five whys | ||
1925 Alfred Sloan adds business elements to mass production, professional management | |||
1926 Henry Ford proposes term mass production | |||
1927 Henry Ford achieves "true mass production" at the Rogue complex | |||
1930s | Kiichiro Toyoda - Just-in-time principle | ||
1940s | 1948 Pull principle | ||
1949 Henri Fayol - General and Industrial Management | |||
1950s | Mass production starts to spread in Europe | Quality improvement programme inspired by the teachings of Deming and Juran | |
1953 Taichi Ohno - Kanban, production levelling | |||
1955 | Final form of mass production | ||
1960s | 1960 Alfred Sloan - My years with General Motors | 1960 Preventive maintenance | |
1962 Kaoru Ishikawa - Quality circles | |||
1962 Shigeo Shingo - Poka-yoke | |||
1970s | 1971 Total productive maintenance | ||
1978 Taichi Ohno - Toyota Production System | |||
1980s | Development of flexible production | ||
1983 Monden Yasuhiro - Toyota Production System an integrated approach to JIT | |||
1984 Beginning of the IMVP reserach | |||
1986 Masaaki Imai - Kaizen (in English) | |||
1988 Taichi Ohno - Toyota Production System (in English) | |||
1990s | 1990 5R programme | 1990 Womack and Jones - The Machine That Changed the World | |
1996 Womack and Jones - Lean thinking | |||
1999 Rother and Shook - Learning to see | |||
2000s | Development of mass customization | ||
2001 The Toyota Way | |||
2002 Increased interest in lean due to economical crisis | |||
2003 Womack and Jones - Lean thinking (Second Edition) | |||
2004 Jeffrey Liker - The Toyota Way | |||
2005 Womack - Lean Solutions | |||
2008 Jeffrey Liker - Toyota culture | |||
2010s | 2010 Mike Rother - Toyota kata | ||
2012 Jeffrey Liker - The Toyota Way to lean leadership |
Four decades of academic interest in the Lean Thinking
Academic interest is important for any paradigm, as it produces objective scientific papers which are rigorously assessed by the scientific community.
Table below presents four decades of academic interest in lean thinking, from 1970s to 2000s, based on the literature review study from Stone (2012). First column represents time frame, second column represents relevant phase and third column shows the number of publications in its respective period. Only peer reviewed publications with more than 3 citations from manufacturing sector longer than four pages were counted.
Period | Phase | Published quantity |
---|---|---|
1970–1990 | Discovery | 11 |
1991–1996 | Dissemination | 31 |
1997–2000 | Implementation | 28 |
2001–2005 | Enterprise | 56 |
2006–2009 | Performance | 67 |
Discovery phase includes Drucker's article (Drucker, 1971) as one of the first to asses the managerial practices of Japanese businesses (New, 2007). Most important publications from that period are those from the MIT's IMVP programme and ultimately The Machine that Changed the World.
After term lean was established and promoted, a phase of dissemination took place from 1991 to 1996, with publications focusing on articulating the principles of lean. Lean thinking from Womack and Jones – first edition published in 1996, second in 2003 – is an important publication from that period, providing lean principles and implementation framework.
Implementation phase followed, with publications focused on analysing the strategic, managerial, human and organisational aspects of lean. Economic crisis and publication (or more precisely, annunciation) of the Toyota Way led to increased interest in the lean paradigm.
Publications from the enterprise period assessed the lean paradigm in various business sectors, mainly white collar jobs (Brandenburg & Ellinger, 2003; Comm & Mathaisel, 2005; Holton III, 2003; Hyer & Wemmerlöv, 2002; Mann, 2002; Scaffede, 2002; Seitz, 2003). In 2006 Toyota Motor Corporation surpassed General Motors as the largest vehicle manufacturer in the world (Holweg, 2007), which led to further increase of interest in the lean paradigm.
During performance phase publications were mainly from Toyota executives and consultants (Shimokawa & Fujimoto, 2009; Liker, 2006; Liker, 2008; Osono et al., 2008), providing inside knowledge of the Toyota Way, while journal publications focused on measuring leanness and replication of successful lean transformation.
Concluding remarks
In this article we went on a journey into the history of lean thinking.
Now let's look into principles and tools associated with it.
References
Ahmadjian, C. L., & Lincoln, J. R. (2001). Keiretsu, governance, and learning: Case studies in change from the Japanese automotive industry. Organization Science, 12(6), 683–701.
Blecker, T., & Friedrich, G. (Eds.). (2006). Mass customization challenges and solutions. Springer.
Brandenburg, D. C., & Ellinger, A. D. (2003). The future: Just-in-time learning expectations and potential implications for human resource development. Advances in Developing Human Resources, 5(3), 308–320.
Comm, C. L., & Mathaisel, D. F. X. (2005). A case study in applying lean sustainability concepts to universities. International Journal of Sustainability in Higher Education, 6(2), 134–146.
Davies, A. C., & Hounshell, D. A. (1985). From the American system to mass production, 1800-1932: The development of manufacturing technology in the United States. Economic History Review, 38(2).
Drucker, P. F. (1971). What we can learn from Japanese management. Harvard University. Graduate school of business administration.
Dyer, J. H. (1996). Does governance matter? Keiretsu alliances and asset specificity as sources of Japanese competitive advantage. Organization Science, 7(6), 649–666.
Gilson, R. J., & Roe, M. J. (1993). Understanding the Japanese Keiretsu: Overlaps between corporate governance and industrial organization. Yale Law Journal, 102(4), 871–871.
Hill, A. (2012). The encyclopedia of operations management: A field manual and glossary of operations management terms and concepts. FT Press.
Holton III, E. F. (2003). Cycle time: A missing dimension in HRD research and theory. Human Resource Development Review, 2(4), 335–336.
Holweg, M. (2007). The genealogy of lean production. Journal of Operations Management, 25(2), 420–437.
Hyer, N. L., & Wemmerlöv, U. (2002). The office that lean built. IIE Solutions, 34(10), 36–43.
Imai, M. (1986). Kaizen (Ky’zen), the key to Japan’s competitive success. Random House Business Division.
Katz, H. (1985). Shifting gears: Changing labor relations in the U.S. automobile industry. MIT Press.
Liker, J. (2004). The Toyota way: 14 management principles from the world’s greatest manufacturer. McGraw-Hill.
Liker, J. (2006). The Toyota way fieldbook: A practical guide for implementing Toyota’s 4Ps. McGraw-Hill.
Liker, J. (2008). Toyota culture: The heart and soul of the Toyota way. McGraw-Hill.
Liker, J. (2011). The Toyota way to lean leadership: Achieving and sustaining excellence through leadership development. McGraw-Hill.
Lincoln, J. R., Gerlach, M. L., & Ahmadjian, C. L. (1996). Keiretsu networks and corporate performance in Japan. American Sociological Review, 61(1), 67–67.
Mann, D. W. (2002). Steelcase learns how teamwork evolves effectively under lean production. Journal of Organizational Excellence, 21(3), 43–48.
Mass, W., & Robertson, A. (1996). From textiles to automobiles: Mechanical and organizational innovation in the Toyoda enterprises, 1895–1933. Business and Economic History, 25, 1–38.
McGuire, J., & Dow, S. (2003). The persistence and implications of Japanese keiretsu organization. Journal of International Business Studies, 34(4), 374–374.
New, S. J. (2007). Celebrating the enigma: The continuing puzzle of the Toyota Production System. International Journal of Production Research, 45(16), 3545–3554.
Nishiguchi, T. (1989). Strategic dualism: An alternative to industrial societies. University of Oxford.
Ohno, T. (1978). Toyota seisan hōshiki. Diamond, Inc.
Ohno, T. (1988). Toyota production system: Beyond large-scale production. Productivity Press.
Osono, E., Shimizu, N., Takeuchi, H., Dorton, J. K., & Pratt, S. (2008). Extreme Toyota: Radical contradictions that drive success at the world’s best manufacturer. John Wiley & Sons Tokyo.
Rother, M. (2003). Learning to see: Value stream mapping to create value and eliminate muda (2nd ed.). Lean Enterprise Institute.
Scaffede, R. (2002). What it takes to turn manufacturing lean: The experience of Donnelly Corporation. Journal of Organizational Excellence, 21(4), 3–16.
Seitz, T. A. (2003). Lean enterprise integration: A new framework for small businesses. Massachusetts Institute of Technology, System Design & Management Program.
Shimokawa, K., & Fujimoto, T. (Eds.). (2009). The birth of lean: Conversations with Taiichi Ohno, Eiji Toyoda, and other figures who shaped Toyota management. Lean Enterprise Institute.
Sloan, A. P. (1964). My years with general motors. Doubleday.
Stone, K. B. (2012). Four decades of lean: A systematic literature review. International Journal of Lean Six Sigma, 3(2), 112–132.
Taylor, F. W. (1911). The principles of scientific management. Harper & Brothers.
Tolio, T. (Ed.). (2008). Design of flexible production systems—Methodologies and tools. Springer.
Toyota Motor Corporation: Environmental report 1999. (1999).
Toyota motor corporation. (2012). http://www.toyota-global.comAccessed on December 5th, 2012.
Womack, J. (2003). Lean thinking: Banish waste and create wealth in your corporation (2nd ed.). Free Press.
Womack, J. P., Jones, D. T., & Roos, D. (1990). The machine that changed the world: Based on the Massachusetts Institute of Technology 5-million dollar 5-year study on the future of the automobile. Rawson Associates.
This article is a part of Lean Thinking series:
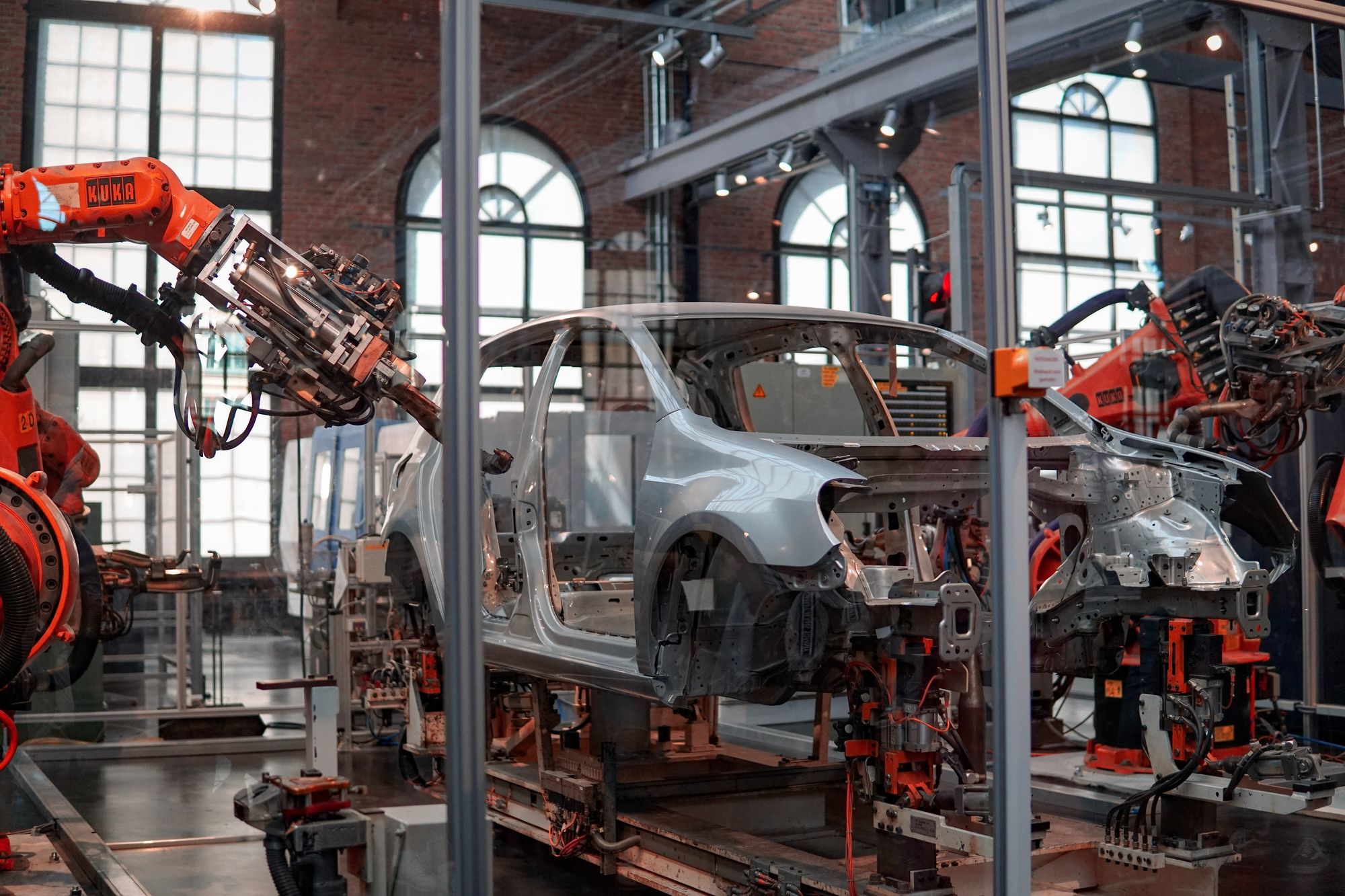
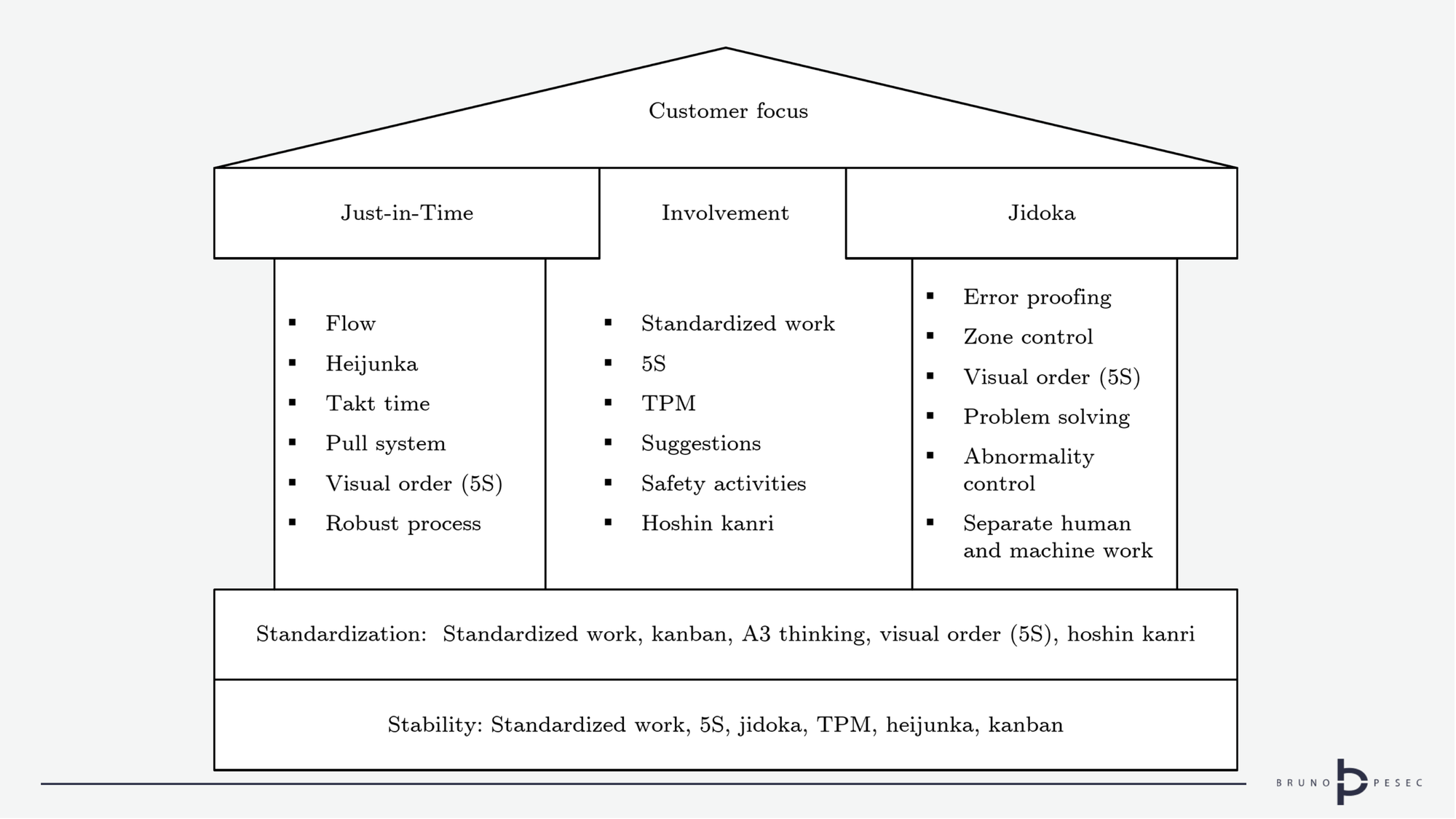
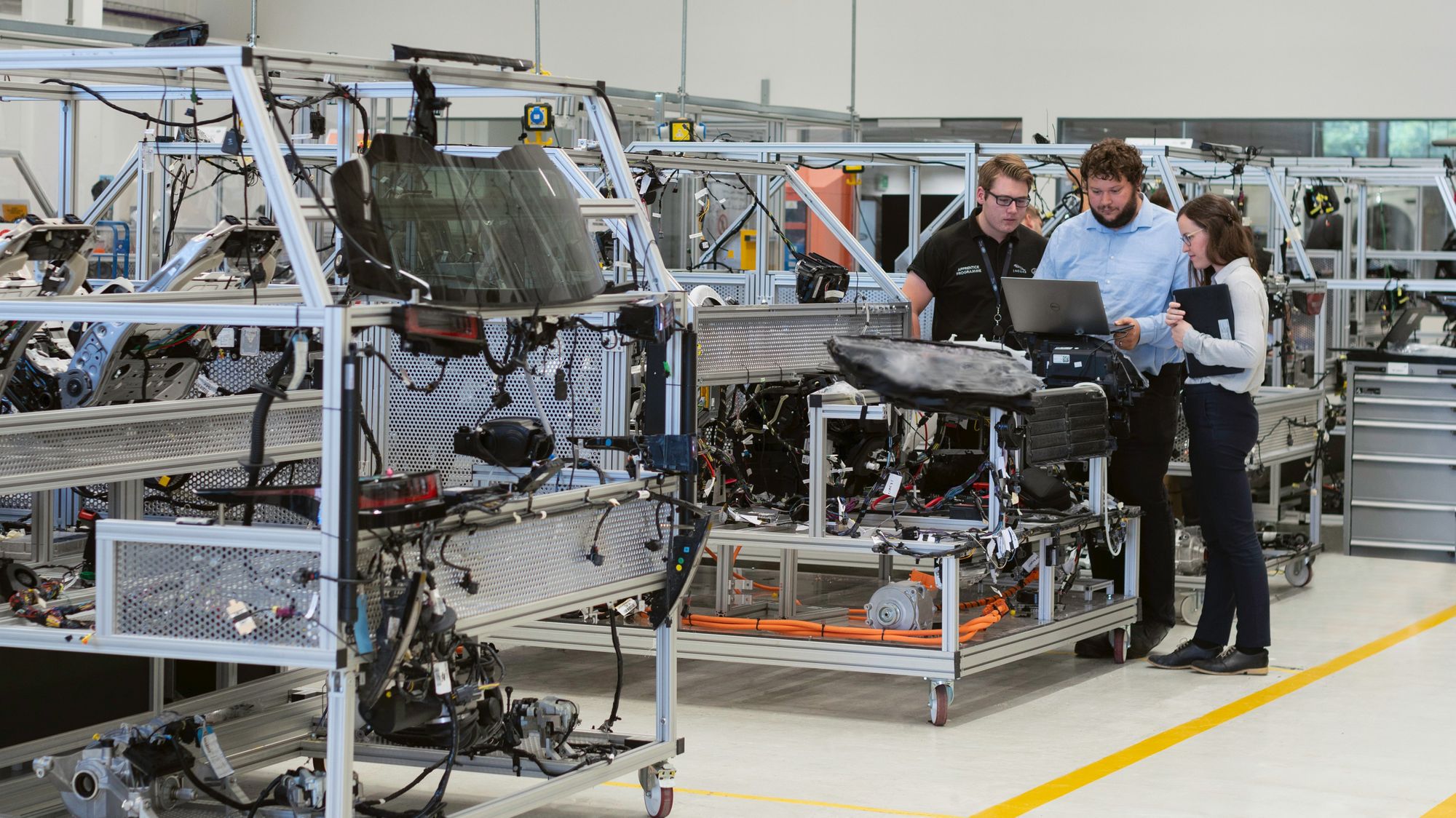
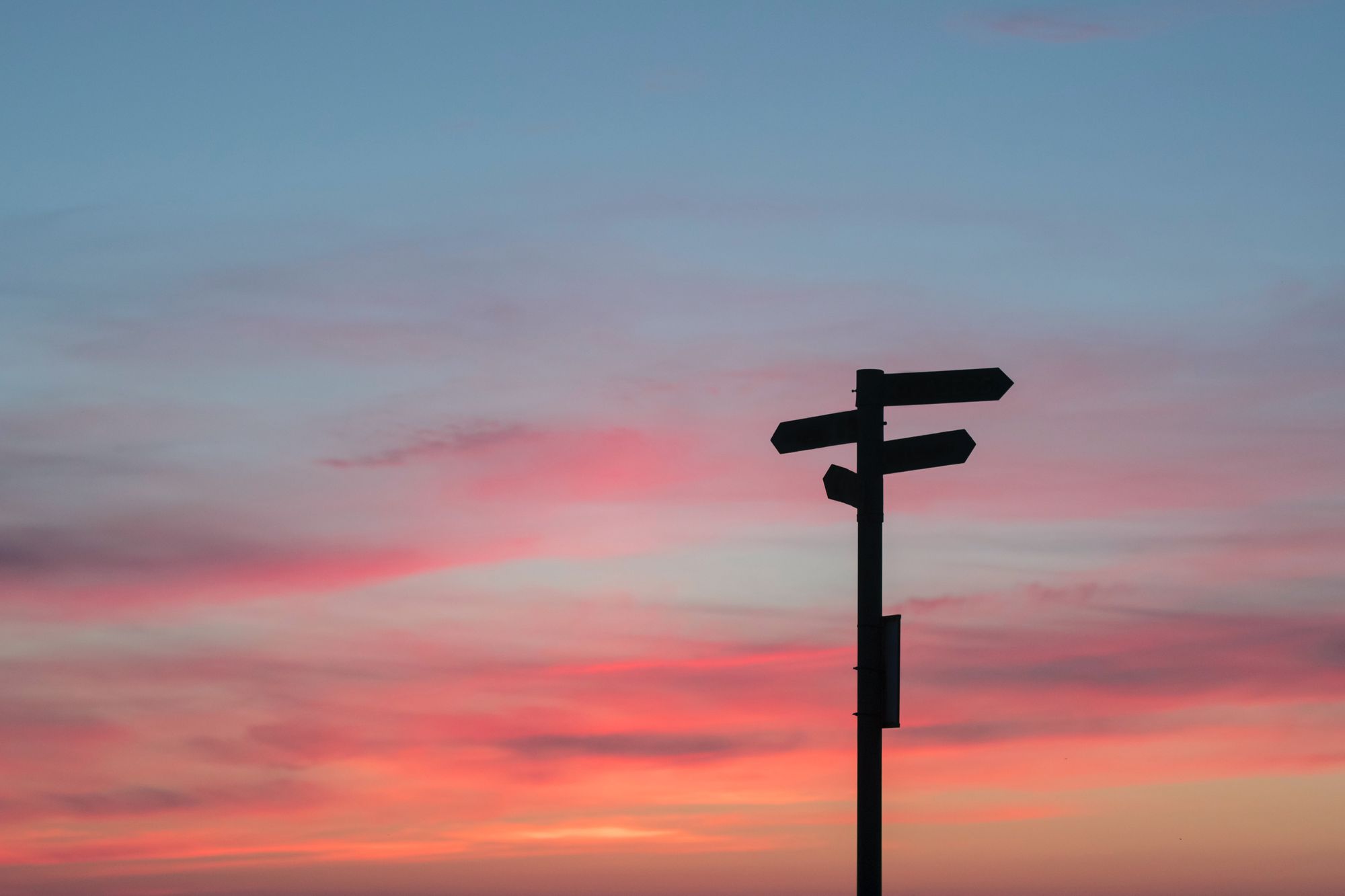
Bruno Unfiltered
Subscribe to get the latest posts delivered right to your inbox. No spam. Only Bruno.