Lean Thinking: principles and tools
Understanding principles behind the lean thinking is critical for our ability to make a change for the better.
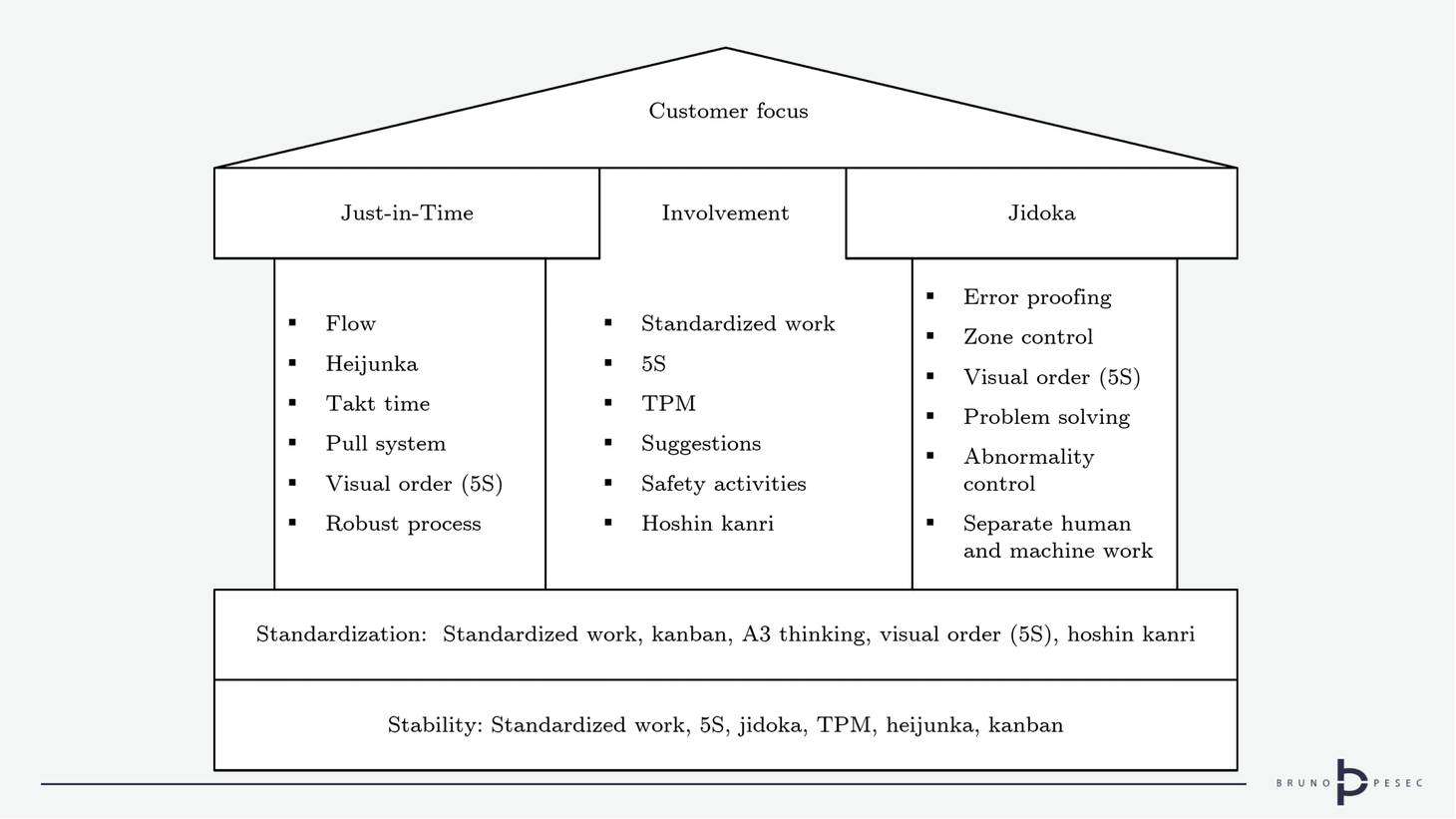
Value, value stream, flow, pull and perfection form a core of lean thinking and provide underlying theory and philosophy (Womack & Jones, 2003).
Lean principles are applied to products or services in following order:
- specify value for the customer,
- identify the value stream,
- establish the flow and establish the pull system.
- Reiterate into infinity, striving for perfection.

Let's look into each principle.
Value
Value must be defined from the perspective of end customer.
It should be assessed in terms of whole product (from idea to end-of-life).
Value stream
After value has been defined value stream should be identified and mapped.
Ohno (1988) and Womack & Jones (2003) identify three type of activities:
- value-added,
- non-value-added (type one muda – Japanese term for waste) and
- waste activities (type two muda).
It should be noted that other authors use slightly different terms which could lead to confusion. Table below compares activities as named by Ohno (1988) to names proposed by George (2002):
Activity | Acronym | Synonym | Acronym |
---|---|---|---|
Value-added | VA | Customer value-added | CVA |
Non-value-added (type one muda) | NVA | Business value-added | BVA |
Waste (type two muda) | WA | Non-value-added | NVA |
Aforementioned activities are defined as follows:
- CVA Activities which add value to the product or service, as defined by the customer.
- BVA Activities which add no value but are required for business to operate efficiently.
- NVA Activities which add no value to neither customer or business.
CVA activities should withstand the 3C litmus test (Hambleton, 2008):
- Change – the activity changes the product or service.
- Customer – the customer is willing to pay for it.
- Correct – the activity is done correctly the first time.
NVA activities, also known as waste activities, should be eliminated first since they add no value to neither the customer or business.
In the Toyota Production System (Ohno,1988) seven wastes were identified: overproduction, waiting, transporting, over-processing, inventories, motion and making defective part and products.
Over time authors of various publications suggested and added new wastes. Hambleton (2008) sums up some of the most common wastes as follows:
Waste | Description |
---|---|
Overproduction | Producing parts ahead of schedule in anticipation of demand, producing wrong parts at the wrong time |
Waiting | People unnecessarily waiting due to either unbalanced operations or waiting for decisions, approvals, or inspection |
Transportation | Moving parts or objects unnecessarily, excess travel distance |
Over-processing | Unnecessary operations, steps and complexity |
Inventories | Excess space consumed by shelving, floor space, excessively wide aisles, bins, filing cabinets, or files that house accumulated in-process or finished goods, including parts waiting fro rework or scrap storage |
Motion | Excess and unnecessary people activities such as searching, walking, sitting, choosing, copying, stapling, sorting, climbing, bending over, and lying down |
Defects | Repairs and reworks needed to get something to function properly |
Materials | Scrap or excess ordering of raw materials |
Idle material | Material that waits or sits in inventory |
Energy | Wasted power or people energy |
Excessive labour | Too many workers in the process causing inefficient operations |
Safety hazards | Unsafe work environments |
Management | Failure to orchestrate and unleash the inherent capabilities of the organization |
Ownership | Lack of accountability, authority or empowerment to perform responsibilities |
Focus | Dispersed energy working on different sets of critical issues due to inconsistent alignment of management and employees |
Structure | Lack of infrastructure support needed to focus on CI or to gain ownership |
Discipline | Failure to maintain the process, performance and behaviours needed to achieve standards |
While it is indisputable that aforementioned activities are true waste, the motive for adding new waste to the core list of wastes should be questioned.
The very same act of adding new wastes could be considered as waste.
Flow
Once value stream has been identified flow should be established.
Flow is the movement of products trough process with minimum time spent on BVA and no time spent on NVA.
Establishing flow increases the velocity of of the supply chain and enables further identification of waste.
Womack & Jones (2003) propose three techniques to achieve flow which should be carried out simultaneously:
- The focus should be on the object of flow from the beginning to the completion.
- Traditional boundaries should be ignored.
- Work practices and tools should be rethought.
Pull
Ohno (1988), inspired by U.S. supermarkets, described pull principle as follows:
The later process goes to the earlier process to acquire the needed parts at the time and in the quantity needed. The earlier process immediately produces the quantity just taken.
Later, Womack & Jones (2003) reformulated Ohno's description as follows:
Pull in simplest terms meant that no one upstream should produce a good or service until the customer downstream asks for it.
Although both formulations appear similar it should be noted that Ohno's description was at the conceptual and strategic level while Womack's and Jones's was at tactical level (Hopp & Spearman, 2004).
Latter description led to confusing push with make-to-stock (MTS) and pull with make-to-order (MTO) strategies. Hopp & Spearman (2004) explain the differences and provide following definition of pull and push:
A pull production system is one that explicitly limits the amount of work in process that can be in the system. By default, this implies that a push production system is one that has no explicit limit on the amount of work in process that can be in the system.
When in doubt go back to the source.
Perfection
An organization should compete against perfection, not against competitors (Womack & Jones, 2003).
A culture of continuous improvement should be instituted, consisting of both incremental (kaizen) and breakthrough (kaikatsu) improvements.
Perfection is unattainable, but should be continuously, relentlessly and vigorously pursued.
Lean tools
Lean house, modelled after the Toyota house (Liker, 2004; Hill, 2012), is often used to depict the core principles and tools of lean thinking:
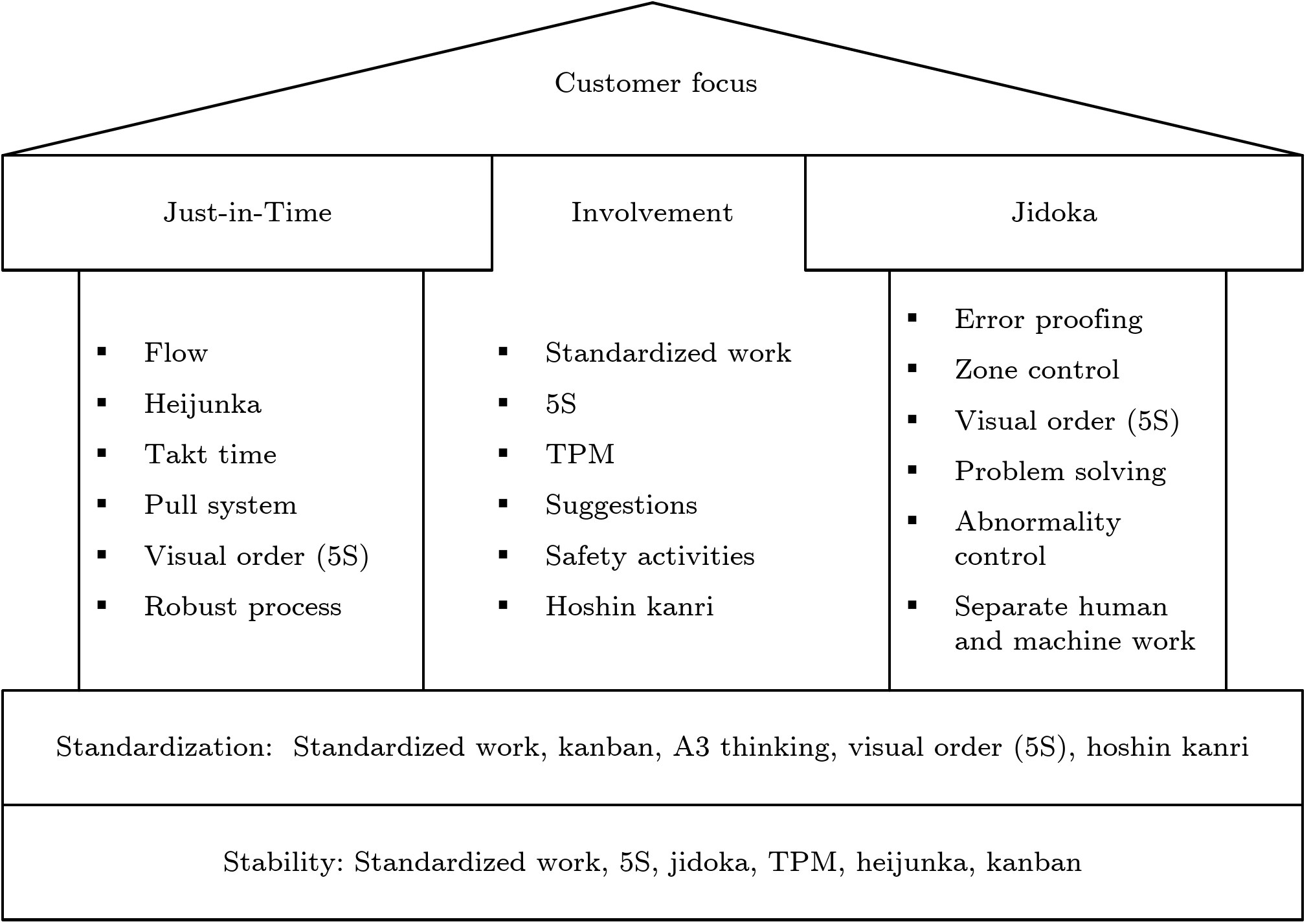
Left pillar emphasises material management, right pillar emphasises the manufacturing processes while foundation emphasises the fundamentals of lean.
Early sketches of it can be found in Toyota seisan hōshiki (Ohno, 1978).
High-level workflow is presented in the figure below, emphasising the project-driven approach to lean implementation and transformation:
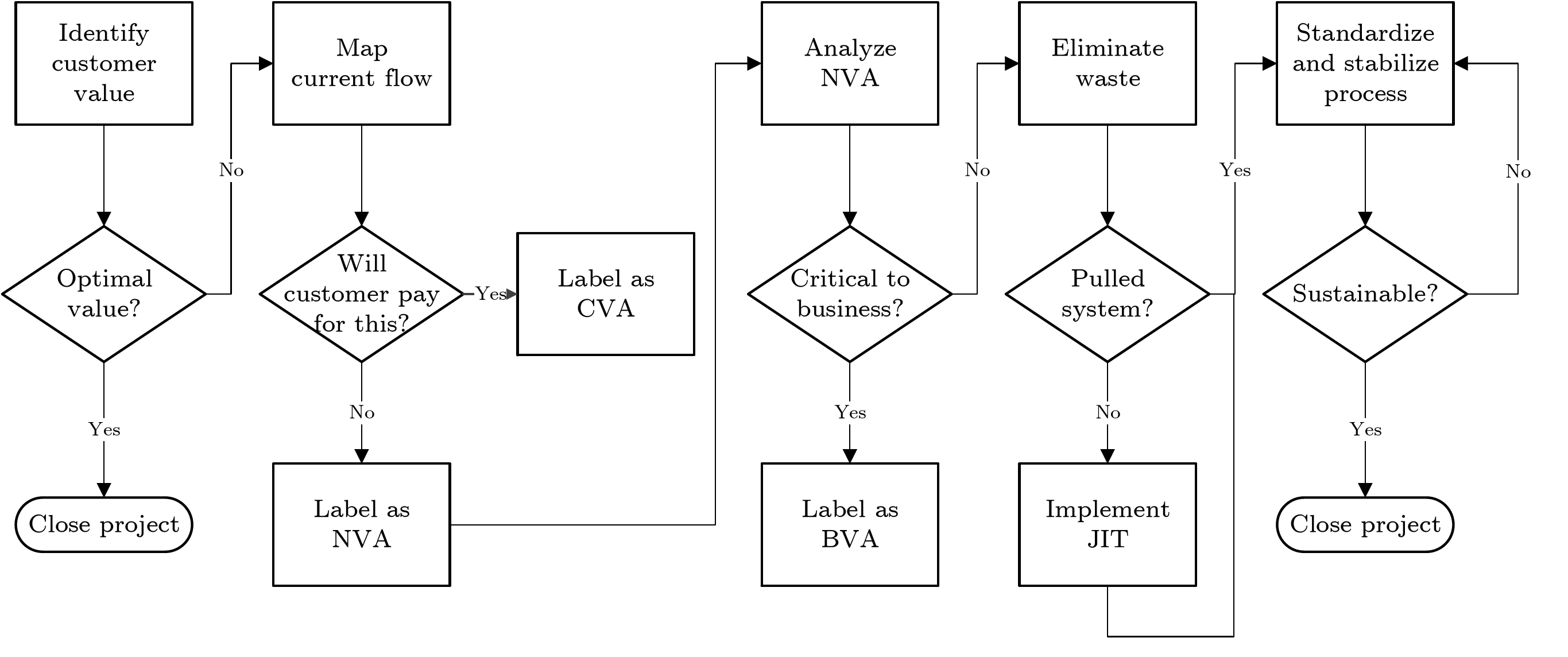
It can be seen that the project starts with identifying the customer value, and ends with project closure instead of backward loop towards the beginning. While it might seem to contradict the flow of principles as laid out by Womack & Jones (2003), it should be noted that automatic adjustment of the system to internal and external changes should be ensured before closing the project.
Another important point is that closure of one project frees resources for following project, hence enabling further improvements. It is of paramount importance to asses the system as a whole before prioritising projects (Womack et al., 1990; Womack & Jones, 2003; Cleland & Gareis, 2006).
Hambleton (2008) lists candidate tools for each activity:
Activity | Candidate tools and techniques |
---|---|
Identify customer value | Voice of customer gathering techniques, takt time |
Map the current process workflow | Detailed process map, swim-lane process map, value stream mapping, value stream matrix, spaghetti map, total lead time, process cycle efficiency, workstation turnover times |
Analyze NVA | Categories of waste, theory of constraints, detailed process map, value stream matrix, spaghetti map, flow manufacturing, multi-process operation, visual control, 5S, constraint management, level loading and levelled production, changeover, manpower reduction, pull systems, kanban, just-in-time, flexible process, lot size reduction, autonomation (Jidoka), standard operation, maintenance and safety, cost benefit analysis |
Eliminate waste | Prioritization matrix, solution select matrix, implementation plan, communication plan, training plan, standard operating procedures (revised), should be value stream matrix, should be process map, should be standard operating procedures, control plan, risk management plan |
Standardize the process | Implementation plan, communication plan, should be value stream matrix, should be process map, should be standard operating procedures, control plan, risk management plan |
Validate the process | Control plan, risk management plan, kaizen |
Closing remarks
I believe that internalising lean principles as underlying theories of lean thinking strategies is critical to developing our capability to deploy and adapt lean thinking within our own context.
Tools are immensely helpful, but each comes with its own history, context, and intention. Being pragmatic pays off – use whatever works, and discard what doesn't. If it is a good tool it'll come back.
References
Cleland, D. I., & Gareis, R. (Eds.). (2006). Global project management handbook: Planning, organizing, and controlling international projects (2nd ed.). McGraw-Hill.
George, M. (2002). Lean Six Sigma: Combining Six Sigma quality with lean speed. McGraw-Hill.
Hambleton, L. (2008). Treasure chest of Six Sigma growth methods, tools, and best practices: A desk reference book for innovation and growth. Prentice Hall.
Hill, A. (2012). The encyclopedia of operations management: A field manual and glossary of operations management terms and concepts. FT Press.
Hopp, W. J., & Spearman, M. L. (2004). To pull or not to pull: What is the question? Manufacturing & Service Operations Management, 6(2), 133–148.
Liker, J. (2004). The Toyota way: 14 management principles from the world’s greatest manufacturer. McGraw-Hill.
Ohno, T. (1978). Toyota seisan hōshiki. Diamond, Inc.
Ohno, T. (1988). Toyota production system: Beyond large-scale production. Productivity Press.
Womack, J. P., & Jones, D. T. (2003). Lean thinking: Banish waste and create wealth in your corporation (2nd ed.). Free Press.
Womack, J. P., Jones, D. T., & Roos, D. (1990). The machine that changed the world: Based on the Massachusetts Institute of Technology 5-million dollar 5-year study on the future of the automobile. Rawson Associates.
This article is a part of Lean Thinking series:
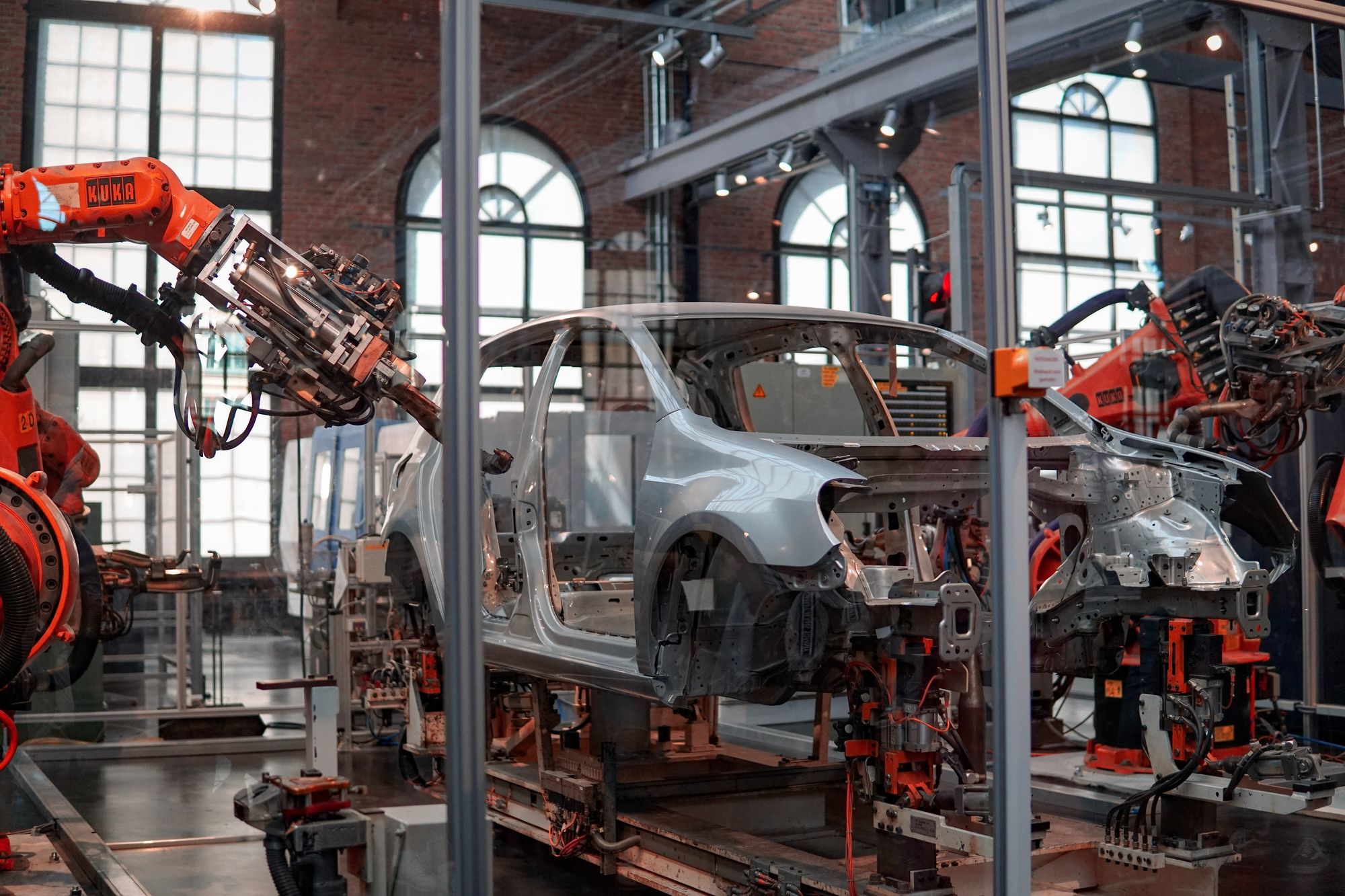
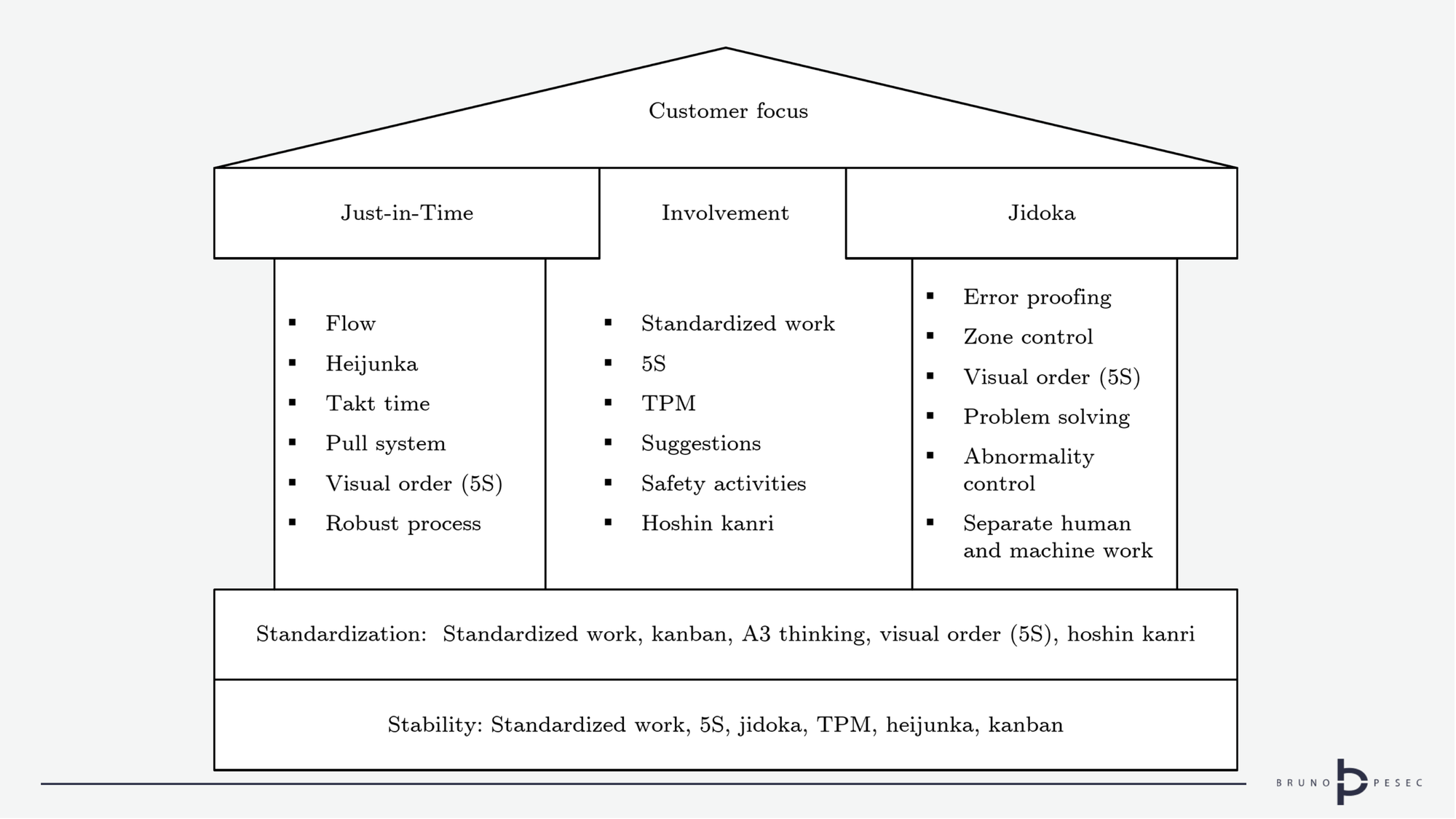
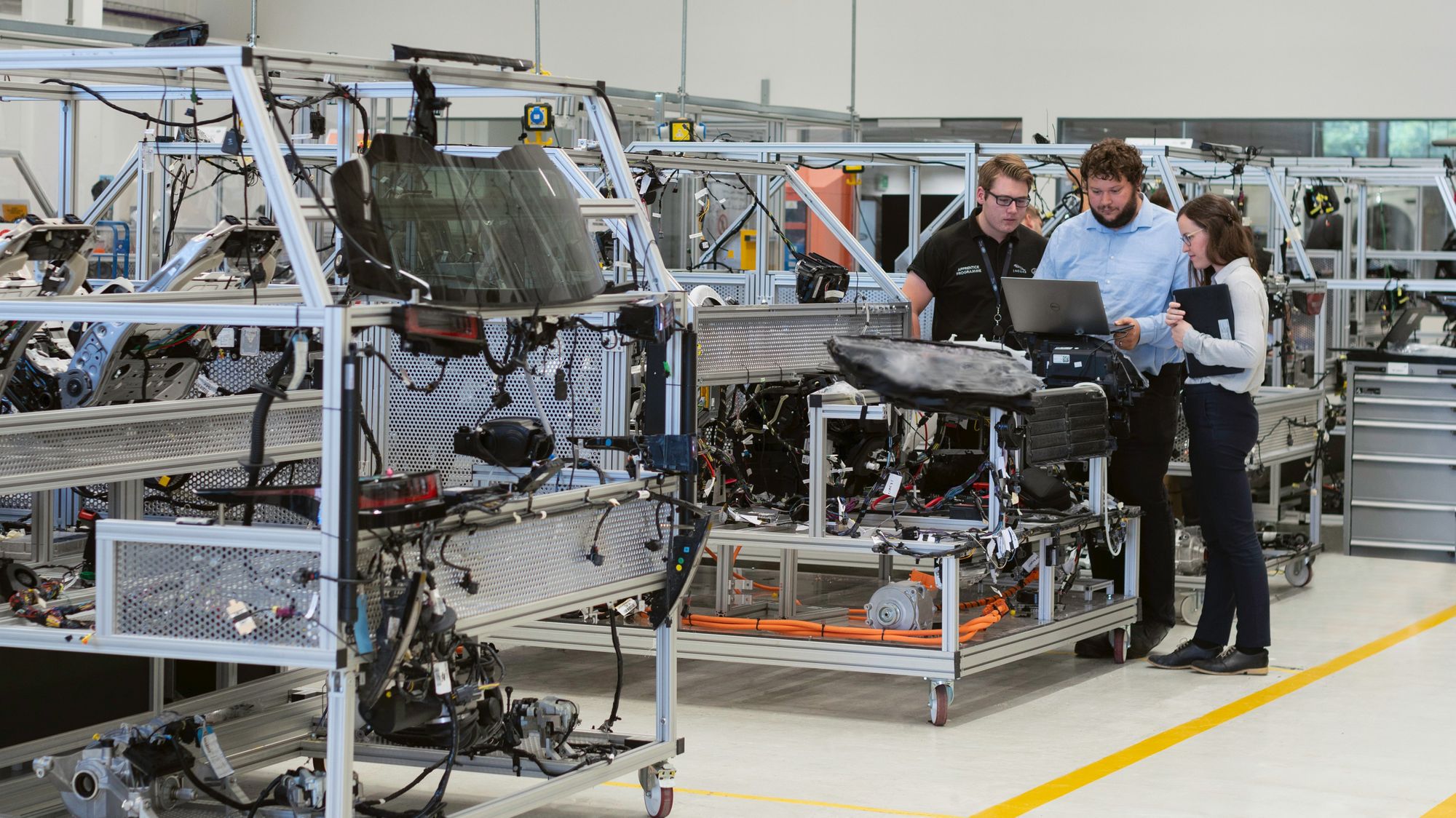
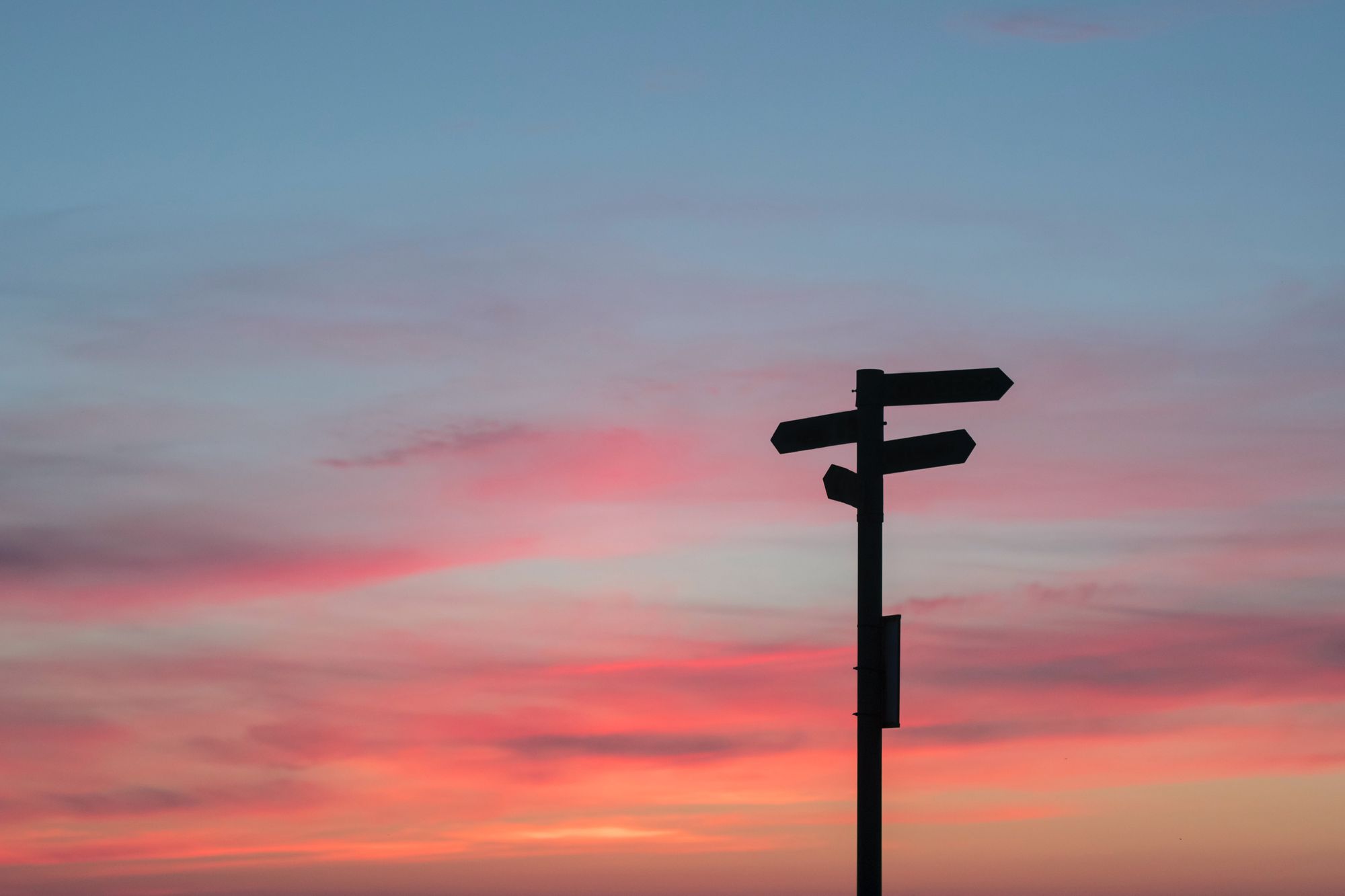
Bruno Unfiltered
Subscribe to get the latest posts delivered right to your inbox. No spam. Only Bruno.